Grandi e medie aziende sono sempre più vicine almeno su un fronte: abbandonare l’inerzia derivante dal “pericolo asiatico” e concentrarsi su soluzioni e criteri che possono perseguire il vantaggio di una crescente competitività. Questa almeno è l’opinione di Domenico Netti, direttore Logistica di Lavazza e presidente Ailog, l’Associazione Italiana di Logistica che ZeroUno ha chiamato a testimoniare per capire quanto possa essere impattante l’innovazione tecnologica, anche a livello di supply chain, per rispondere alle sfide in corso sul mercato globale. “La crescente competitività internazionale ha stimolato le nostre imprese a realizzare impianti di produzione in aeree geografiche dove è possibile reperire alcuni dei fattori produttivi, vedi manodopera, materie prime ed energia, a costi contenuti. Il saving derivante dal basso costo di questi fattori produttivi non è però sufficiente – ha precisato Netti – per assicurare la competitività dell’impresa. Quando un piccolo imprenditore avvia rapporti di scambio con paesi esteri o costruisce impianti di produzione in questi stessi paesi, si trova costretto ad affrontare numerose difficoltà, il cui superamento richiede tempo e costi”. L’istantanea scattata da Netti ha quindi anche un altro punto critico: “Nell’era della globalizzazione dei mercati, delle produzioni e dei servizi, la parcellizzazione delle iniziative imprenditoriali, oltre ad essere sterile nel perseguimento degli obiettivi, impedisce alla logistica italiana di confrontarsi con dignità e autorevolezza con le strutture logistiche di altri paesi europei che, da tempo, hanno sostituito il micro-individualismo con approcci sistemici basati sulla strategia dell’azione aggregata”.
Entrando nel merito dell’esperienza Lavazza, quanto a livelli di adozione dell’It a supporto dei propri processi logistici e produttivi, Netti ha voluto sottolineare come l’aver sempre “puntato sull’innovazione tecnologica e sulla riorganizzazione dei processi all’insegna dei mutamenti e dell’espansione del mercato [Lavazza esporta su scala mondiale il 37% della produzione, ndr] sia stato un fattore determinante per lo sviluppo del business aziendale. Abbiamo uno stabilimento fra i più grandi d’Europa, con un altissimo livello di automatizzazione; la movimentazione delle merci è a zero addetti e l’handling è effettuato da trasloelevatori controllati e gestiti da un sistema informativo centrale. La tecnologia ha un ruolo fondamentale nella nostra supply chain e lo dimostra per esempio l’utilizzo di applicazioni Rfid negli stabilimenti di produzione di Settimo Milanese e di Gattinara per la movimentazione interna dei pallet. Un’azienda che aspira a competere sui mercati internazionali non può prescindere dall’essere pronta per recepire soluzioni avanzate da adottarte nella supply chain a livello di unità di produzione, il vero punto di vendita della distribuzione moderna”.
Il modello cui è ricorsa Lavazza per automatizzare i propri processi logistici è presto riassunto: il collegamento satellitare in essere fra mezzi di trasporto-stabilimento-punto di vendita consente di gestire la merce viaggiante con una sensibile riduzione delle scorte di sicurezza di materie prime e una qualificazione del livello di servizio offerto ai clienti. La conoscenza dei lotti di materie prime che sono in viaggio verso lo stabilimento ha permesso inoltre di controllare in tempo reale l’esatta posizione della merce che è in consegna verso i punti di vendita e, in caso di anomalie, la logistica Lavazza ha tutti gli strumenti per entrare in contatto con la logistica del cliente per risolvere il problema e prevenire di fatto i costi dovuti a soste o a spostamenti di consegne.
A Netti abbiamo quindi chiesto di entrare del merito delle problematiche di integrazione dei partner di filiera e dell’uniformità dei dati e la risposta ha confermato l’importanza strategica del fattore relazione: “Oggi l’efficienza si persegue attraverso l’integrazione con tutti i protagonisti della supply chain, è indubbio. Lavazza è stata pioniera nel realizzare un sistema Crp applicato al Multidrop [consegne multiple a distributori diversi effettuate dallo stesso automezzo con un unico carico ndr], grazie al quale si abilita l’acquisizione dell’ordine attraverso un collegamento Edi Lavazza-cliente e si garantisce nello spazio di poche ore consegne consecutive di pochi pallet a punti di vendita raggiungibili dall’automezzo. L’integrazione delle attività logistiche con tutti gli attori della filiera è stata successivamente estesa rispettando un preciso principio, quello di operare in perfetta sincronia con l’azienda perseguendo gli obiettivi che le direzioni vendite stabiliscono con i clienti”.
La relazione con i partner di filiera fra criticità e benefici
Anche ad
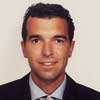
Alberto Lupano, Demand & Operations Planning Manager Coca-Cola Hbc Italia, società del gruppo che gestisce le fasi di imbottigliamento e distribuzione delle bevande, abbiamo chiesto quali sono i passi da compiere per raggiungere risultati significativi in un progetto di supply chain. “Occorre rispettare innanzitutto una regola ben precisa: prima vengono i processi, poi l’aggiornamento dei sistemi informativi. Adottare soluzioni software mirate alla gestione della filiera distributiva deve essere sinonimo di integrazione a livello di sistema, altrimenti si automatizzano attività di routine senza evolvere sotto l’aspetto dell’efficienza operativa e organizzativa. La flessibilità si raggiunge con progetti integrati di relazione fra fornitori e clienti, di scambio di informazioni in tempo reale: le tecnologie It devono intervenire in questo senso, per supportare miglioramenti a livello di processo che derivano da decisioni strategiche. Prendiamo la tecnologia Rfid, oggi ancora lontana dall’essere applicata su larga scala perché manca di fatto uno standard mondiale riconosciuto: è sicuramente un esempio di come strumenti innovativi potranno portare vantaggi sensibili alla catena di fornitura, ma pensare che la tecnologia sia adottata in tempi brevi da tutti gli attori presenti nel ciclo di vita del prodotto, dal magazzino di partenza allo scaffale di arrivo, è uno scenario solo futuribile se non ci si chiama Wall Mart”.
L’esperienza di Coca-Cola Hbc Italia è quindi una fotografia calzante di quali siano i rapporti in essere, oggi, fra i diversi attori della filiera. “Con i fornitori – ci ha spiegato Lupano – il terreno per avviare una relazione improntata all’innovazione è fertile, meno lo è con i retailer: solo le grandi catene possono vantare competenze dedicate e risorse tecnologiche utili a sviluppare un atteggiamento proattivo e non conservatore rispetto alla condivisone di dati critici”. Nella conta dei pro e dei contro, delle criticità incontrate e dei benefici ricavati, Lupano ha quindi rilevato come “implementare progetti di supply chain avanzati, dinamici o demand driven, comporti necessariamente il mettere in preventivo anche una serie di problematiche quali la disponibilità dei partner a condividere il progetto, sistemi dati che si parlano poco fra di loro e che quindi richiedono investimenti ad hoc aggiuntivi per uniformare gli stessi fra tutti gli attori della filiera, clienti poco disposti a intervenire sui propri ambienti informativi. Per contro, quando questi ostacoli vengono meno e la gestione di alcuni processi è automatizzata in modo sistemico, emergono in modo evidente vantaggi quali una maggiore visibilità della supply chain stessa, il poter creare una catena capace di fornire informazione in tempo reale, la possibilità di arrivare a scelte più oculate e tempestive e di reagire più rapidamente agli eventuali problemi”. Il ruolo dei vendor It, infine, viene salutato da Lupano sempre e comunque strategico per vari motivi: “Nelle aziende di medie e grandi dimensioni l’Erp gioca spesso un ruolo centrale e determinante e una piattaforma come Sap, che in Coca-Cola HBC Italia gestisce il ciclo passivo e in tempi futuri sostituirà il vecchio sistema legacy per quello attivo, diventa piattaforma di riferimento per gli attori della supply chain e fa da volano all’implementazione di moduli aggiuntivi nativamente integrati nell’ambiente operativo esistente. Altre aziende, invece, hanno concentrato l’utilizzo di risorse informatiche per abilitare soluzioni distribuite via extranet che fungono da interfaccia fra azienda e mondo esterno”.
Ailog: La logistica italiana guarda ad Est
La sede di Ailog è a Milano e sono operative sezioni territoriali a Torino, Venezia, Roma e Bari. Per affrontare le esigenze delle imprese locali impegnate in progetti di internalizzazione delle proprie attività, l’Associazione sta creando, in collaborazione con il Ministero delle Attività Produttive e dell’Istituto per il Commercio Estero, sedi di riferimento e di supporto in Romania, Russia, Ucraina, Moldavia, Bielorussia e, prossimamente, Serbia. Una menzione particolare merita l’iniziativa in corso d’opera per Idc (Italian Distribution Council) che ha come fine ultimo la definizione delle infrastrutture tecnologiche a supporto del nuovo corridoio nei Balcani che dovrà collegare il porto di Bar con Belgrado. All’estero Ailog realizza corsi di formazione manageriale in logistica e gestione della supply chain ma l’obiettivo prioritario è lo sviluppo di partnership fra imprese italiane ed estere cui è indirizzata la vendita di servizi di logistica dedicati. L’utilizzo delle tecnologie It per gestire e migliorare i processi logistici e supportare gli associati nella sperimentazione e nella scelta di nuovi strumenti e metodologie è uno dei punti focali dell’azione di Ailog e lo conferma il fatto che di recente è stato costituito un gruppo di lavoro con l’obiettivo di sperimentare l’utilizzo dei tag Rfid nella distribuzione dei beni di largo consumo con riferimento anche alle tematiche della tracciabilità obbligatoria per i prodotti alimentari. (G.R.)