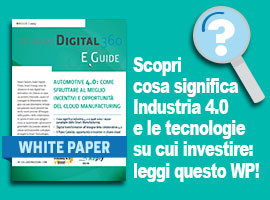
Si chiama Industria 4.0 il nuovo orizzonte di una produzione e di una distribuzione che diventano più smart vale a dire più intelligenti, più veloci e più efficienti. In che modo?
Grazie a un mix tecnologico di automazione, informazione, connessione e programmazione che stanno portando a un cambio dei paradigmi tecnologici e culturali che, coinvolgendo il sistema manifatturiero in tutte le sue forme, introduce nuovi concept di sviluppo e di servizio all’insegna di una digital trasformation sempre più spesso sinonimo di disruption.
Quel suffisso 4.0, infatti, corrisponde alle tappe di un’evoluzione estremamente precisa. Dall’introduzione della macchina a vapore all’uso sempre più pervasivo dell’automazione, dall’informatizzazione alla digitalizzazione, il passaggio alla quarta rivoluzione industriale traghetta le imprese verso una nuova dimensione detta bimodale, perché costituita da un ecosistema di risorse fisiche e virtuali.
Figlia di quella digital transformation che sta progressivamente cambiando usi e costumi, innescando una rivoluzione culturale su scala globale, l’Industria 4.0 è anche una nuova dimensione della comunicazione e del business.
Industria 4.0: storia ed evoluzione tecnologica
Nell’infografica sottostante ecco la road map che riassume le 4 tappe evolutive della storia industriale.
1784 – Industria 1.0
L’Industria 1.0 corrisponde a una rivoluzione della manifattura rispetto all’uso dell’energia: l’invenzione della macchina a vapore, infatti, consente alle fabbriche di abbandonare mulini e introdurre una meccanizzazione della produzione all’insegna di una maggiore velocità e potenza.
1870 – Industria 2.0
L’Industria 2.0 rappresenta la seconda generazione energetica, legata all’utilizzo dell’elettricità prima e del petrolio poi, che permettono di incrementare ulteriormente i livelli di meccanizzazione e di produzione. È grazie a questa rinnovata potenza che nella manifattura si afferma progressivamente quella catena di montaggio che inaugura l’era della produzione di massa.
1970 – Industria 3.0
L’industria 3.0 riassume l’ingresso in fabbrica dell’ICT di prima generazione: informatica ed elettronica incrementano ulteriormente i livelli di automazione non solo nell’ambito produttivo ma anche (e soprattutto) organizzativo. Si diversificano le infrastrutture e si avviano nuovi processi che, all’insegna della progressiva digitalizzazione, diversificano e agevolano il lavoro delle persone migliorando la qualità della produzione.
2011 – Industria 4.0
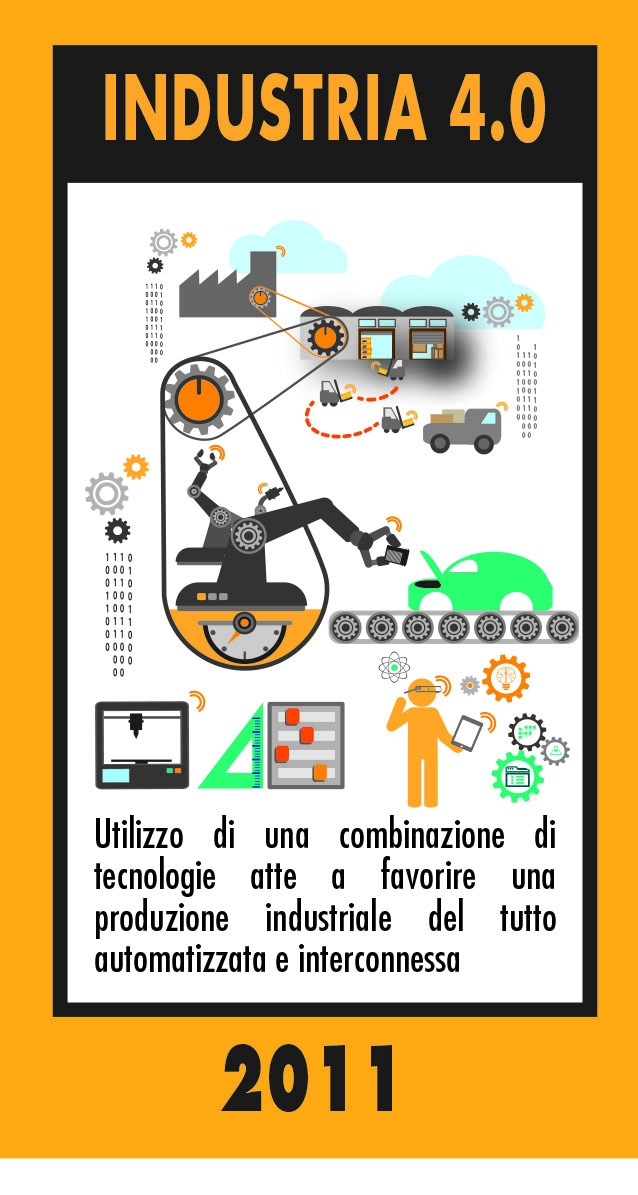
Industry 4.0 che cosa è
Industry 4.0, includendo un mix tecnologico di robotica, sensoristica, connessione e programmazione, rappresenta una nuova rivoluzione rispetto al modo di fabbricare i prodotti e di organizzare il lavoro. Come? Grazie a nuovi modelli di produzione sempre più automatizzati e interconnessi, asset e prodotti intelligenti e comunicanti, una tracciabilità e una rintracciabilità dei processi tale da portare a una gestione delle informazioni collettiva, condivisa e collaborativa a livello di filiera, nuove logiche di servizio all’insegna del cloud e della mobility. Il tutto incentrato su una Internet di ultima generazione (Industrial Internet), capace di portare dentro e fuori alle fabbriche più informazione, più integrazione, più interazione e più efficienza, rinnovando i processi e i sistemi ma anche portando nuove regole di comunicazione e di servizio. Software di nuova generazione da un lato e Big Data Management d’altro, è così che la produzione riesce ad arrivare a una personalizzazione di massa.
Da dove nasce il termine Industria 4.0
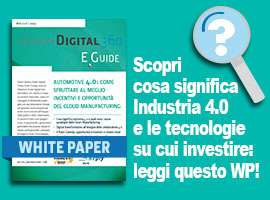
Termine di nuovo conio che ha dato l’abbrivio a una reinterpretazione della nostra cronistoria tecnologica, Industria 4.0 è stato usato per la prima volta nel 2011 alla Fiera di Hannover, in Germania, come ipotesi di progetto da cui è partito un gruppo di lavoro che nel 2012 ha presentato al governo federale tedesco una serie di raccomandazioni per l’implementazione del Piano Industria 4.0. L’8 aprile 2013, sempre alla Fiera di Hannover, è stato diffuso il report finale con una previsione degli investimenti necessari su infrastrutture, scuole, sistemi energetici, enti di ricerca e aziende per ammodernare il sistema produttivo tedesco e riportare la manifattura tedesca ai vertici mondiali rendendola competitiva a livello globale. Il modello è stato fonte di ispirazione per tutti gli altri Paesi.
In Italia il Piano Nazionale Industria 4.0 – 2017-2020 è stato presentato il 21 settembre 2016 dal Ministero dello Sviluppo Economico Carlo Calenda e prevede un insieme di misure organiche e complementari in grado di favorire gli investimenti per l’innovazione e la competitività.
Industria 4.0, smart fabric o smart manufacturing?
Le soluzioni coinvolte sono tantissime, organizzarle in maniera armonica e coordinata è una sfida che ha bisogno di competenze diversificate e di vision ampie e lungimiranti. Il denominatore comune? Un’integrazione dei processi e delle procedure che coinvolgono tutte le filiere, traghettando così le imprese verso nuovi modelli di sviluppo della produzione e del business, diversificati e complessi.
Gli esperti come Boston Consulting o McKinsey, per aiutare a capire, parlano di Smart Fabric, proponendo una ripartizione dei cluster tecnologici su tre livelli:
- SMART PRODUCTION: nuove tecnologie produttive creano interazione tra tutti gli asset legati alla produzione, favorendo la collaborazione tra uomini, macchine e sistemi.
- SMART SERVICES: una governance di nuova generazione delle infrastrutture informatiche e tecniche aiuta a gestire e presidiare i sistemi, sfruttando logiche di massima integrazione tra tutti gli attori della supply chain, clienti inclusi.
- SMART ENERGY: nuovi sistemi di alimentazione e un’attenzione al monitoraggio dei consumi energetici, rendono le infrastrutture più performanti, più economiche e più ecologiche.
L’innovazione tecnologica, infatti, migliora e rende più efficiente da un lato i processi di produzione e dall’altro i processi di gestione.
In questo senso, rispetto al Piano Nazionale Industria 4.0 declinato sul modello tedesco in 9 cluster tecnologici, va evidenziato come idealmente 4 siano più propriamente associati alla gestione della produzione (Smart Production) e 5 alla gestione delle informazioni e delle infrastrutture di servizio (Smart Governance).
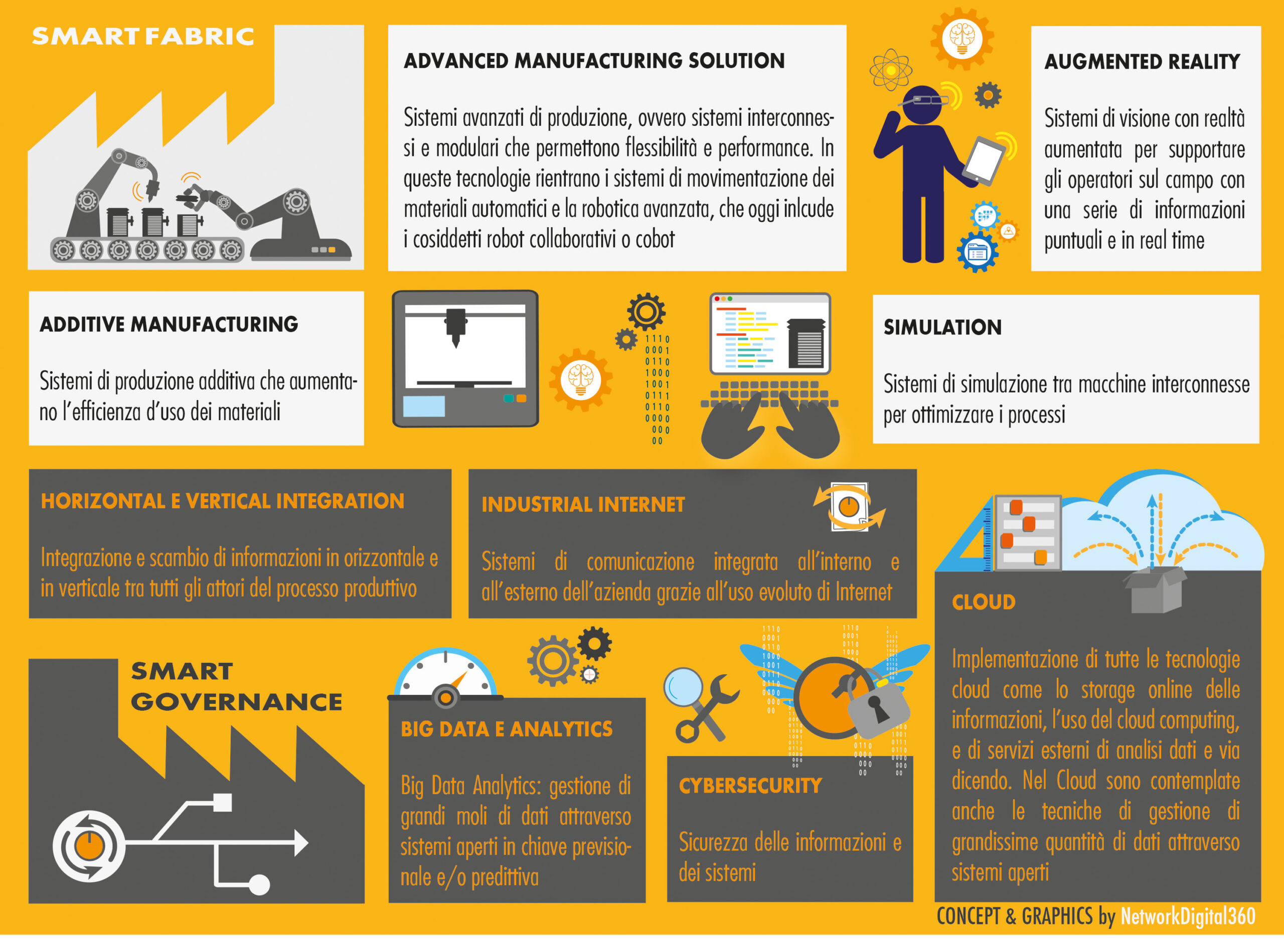
I cardini del Piano Nazionale Industria 4.0 sono incentrati su una serie di tecnologie abilitanti capaci di creare modelli di interconnessione e collaborazione tra le informazioni e i sistemi, integrando tecniche produttive capaci di migliorare le condizioni di lavoro, aumentare l’efficienza e la qualità produttiva degli impianti, diminuire il consumo di energia e gli sprechi per finalizzare un’offerta capace di rimanere sempre allineata alla domanda, favorendo una produzione predittiva.
Il manufacturing nell’era delle smart tecnologies
Gli analisti dell’Osservatorio Industria 4.0 del Politecnico di Milano entrano ancora più nel dettaglio, analizzando tutte le Smart Technologies del manufacturing, sottolineando come Smart Manufacturing non significhi adottare isolatamente questa o quella tecnologia innovativa, quanto mettere a fuoco il meccanismo complessivo attraverso cui la maggiore integrazione delle risorse genera del valore addizionale, riducendo le inefficienze, valorizzando la conoscenza, e migliorando la capacità di pianificare e reagire.
Gli esperti hanno schematizzato i tre ambiti in cui le tecnologie digitali stanno cambiando modelli e approcci nell’ambito dello Smart Manufacturing:
- SMART LIFECYCLE MANAGEMENT: Comprende l’intero processo di sviluppo di ogni nuovo prodotto, includendo la gestione dell’intero suo ciclo di vita
- SMART SUPPLY CHAIN: Include la pianificazione dei flussi fisici e finanziari nel sistema logistico-produttivo allargato a tutta la filiera
- SMART FACTORY: Abbraccia l’intera governance legata a infrastrutture e servizi: produzione, logistica interna ed esterna, manutenzione, qualità, sicurezza e rispetto delle normative
Nel futuro immaginato dallo Smart Manufacturing, dunque, gli impianti, i lavoratori, i materiali in input e i prodotti finiti saranno dotati di sensori che li identificano e ne rilevano costantemente posizione, stato e attività mentre i dati raccolti saranno analizzati per migliorare la capacità produttiva, l’efficienza, la sicurezza e la continuità operativa. Infine, tutta la fabbrica sarà connessa al resto del sistema logistico-produttivo e ai clienti tramite piattaforme cloud.
Cloud Manufacturing come abilitatore del cambiamento 4.0
Il cloud manufacturing sta affermandosi anche in Italia sia a livello delle Grandi Aziende che a livello di PMI. Gli analisti dell’Osservatorio Cloud del Politecnico di Milano hanno evidenziato come anche nel 2016 il Public Cloud sia cresciuto con una dinamica vicina al 27%, generando un valore di mercato pari a 587 milioni di Euro. Parallelamente, sta crescendo anche la Cloud Enabling Infrastructure, ossia l’insieme di investimenti necessari a creare le condizioni abilitanti per l’utilizzo del Cloud, che, con un incremento vicino al 14%, ha raggiunto quota 1,185 miliardi di euro. Le rilevazioni dell’Osservatorio permettono, sommando le due componenti, di stimare un mercato complessivo che tocca i 1,77 Miliardi di euro, con una crescita anno su anno pari al 18%. Gli Osservatori I4.0 del Politecnico di Milano hanno già classificato un campione di 300 piattaforme:
Smart Life Cycle, di cui il 51% Customer Relationship Management (CRM), il 36% di Supplier Relationship Management (SRM) e il 13% di Product LifeCycle Management (PLM)
Smart Supply Chain di cui 27% Production Planning, 20% Transportation/Distribution Planning, 25% Inventory Planning 28%, Sales/Demand Planning 28%
Smart Factory, di cui 38% Transportation & Internal Logistics, 21% Production, 22% Maintenance, 19% Quality
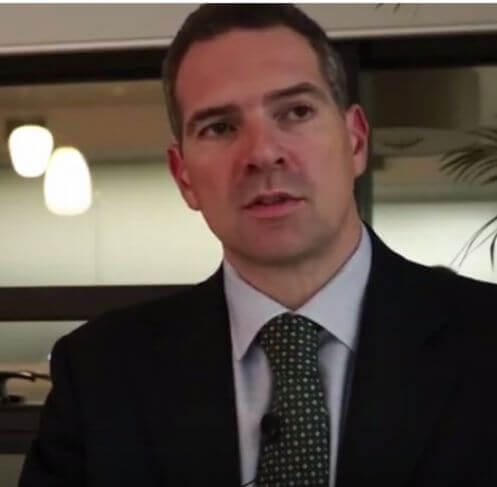
“Le piattaforme cloud sono già una realtà nelle imprese grandissime – sottolinea Giovanni Miragliotta, co-direttore Osservatorio Industria 4.0 del Politecnico di Milano – e sono in fase di introduzione per le aziende più piccole. L’esistenza di una molteplicità di piattaforme multifunzionali lascia aperto un tema importante che è quello della standardizzazione”.
Gli analisti del Politecnico a questo proposito tracciano un’evolutiva interessante rispetto all’innovazione delle logiche di servizio associate al cloud manufacturing parlando, idealmente, di un nuovo modello ipotizzato come Manufacturing As a Service.
“Al crescere dell’abitudine di usare risorse on demand – spiega Miragliotta -, potranno affermarsi modelli più spinti. Idealmente anche una parte del ciclo di progettazione e produzione del prodotto fisico potrebbe essere affidata al cloud, terziarizzando a un provider una parte dei processi”.
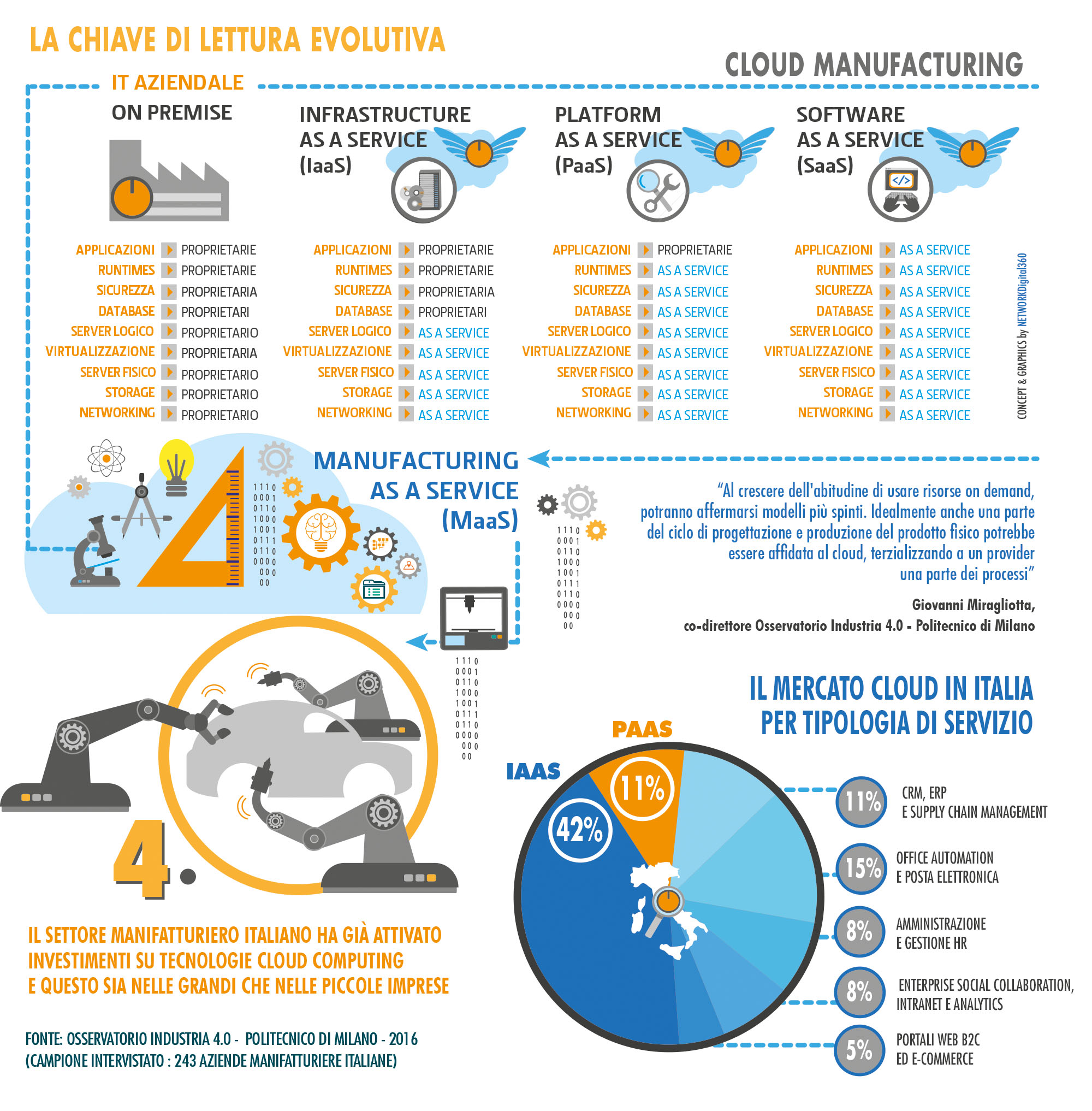