Metodologie strutturate, coinvolgimento dei giusti stakeholder, scelta di tecnologie per l’industria: ecco tre indicazioni che possono facilitare il passaggio all’Industrial IoT. L’Internet delle cose e le tecnologie per l’interconnessione di impianti, processi e applicazioni sono senza dubbio, per l’industria, le più grandi opportunità degli ultimi decenni. Si può anche dire che a questo punto, in gran maggioranza, l’utilità di queste tecnologie sia stata compresa, se nel Vodafone Barometer 2019 il 95% degli adopter ha dichiarato di averne già misurato i vantaggi. Eppure, la maggior parte dei dati rimane ancora sommersa nei macchinari, c’è chi non va oltre la fase dei POC e permangono forti barriere. Le congiunture economiche e l’instabilità politica poi non aiutano.
L’Industrial IoT va affrontata con metodo. Il modello “5 C”
È significativa la storia di un prospect del settore manifatturiero, poi non convertito in cliente, che ci ha detto: “Voglio fare la fabbrica digitale”. È evidente che fare Industrial IoT dalla sera alla mattina senza affrontare un percorso non porta da nessuna parte. Le complessità di una fabbrica, di un building, o di un sistema idrico di una utility possono essere sufficienti per domandarsi con panico “Da dove si comincia?”. A questo proposito, può essere di aiuto una metodologia che passo per passo guidi un’attività industriale lungo un percorso. Partendo da sistemi il modello delle “5 C”. Che si tratti di una linea produttiva, di una facility industriale, o persino di un datacenter: connettere, controllare, condividere, customizzare e correggere sono gli aspetti che da un lato qualificano e dall’altro accomunano i progetti di Industrial Internet che hanno avuto successo.
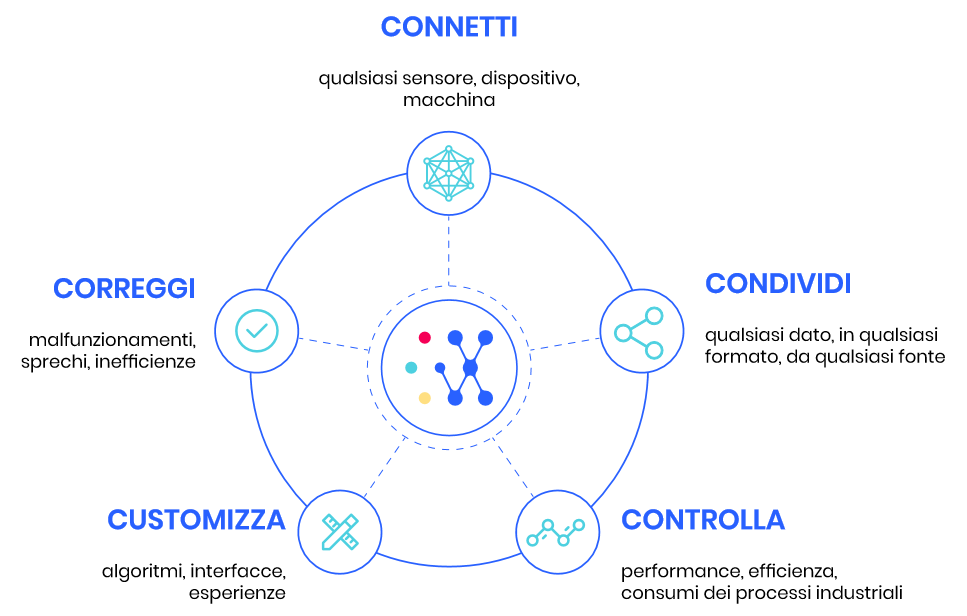
Il modello delle 5 C per realizzare progetti di Industrial IoT
Chi volesse approfondire l’argomento può consultare questo white paper. In sintesi, sembra una banalità ma non lo è, la prima cosa da fare per fare un building, un processo o una fabbrica connessa è… connetterla. Nella realtà non tutte le attività industriali hanno asset già in rete. Il primo passo dunque è realizzare una infrastruttura di rete e un impianto di sensori che, o direttamente raccogliendo dai macchinari e sistemi di nuova generazione o in logica di retrofitting, possa iniziare a raccogliere dati. Il fatto di connettere degli asset, dà già la possibilità di fare un passo avanti e iniziare a controllare.
Se il dibattito sull’innovazione tecnologica è molto incentrato sull’Intelligenza Artificiale, il semplice fatto di dare intelligenza (cioè raccogliere informazioni) agli impianti connessi può avere un impatto sul business. Controllare i consumi, le performance operative, lo stato dei processi produttivi, le condizioni di sicurezza degli impianti e degli stabilimenti è già un passo fondamentale per evidenziare aree di inefficienza, di spreco energetico o aree produttive insicure.
Nel tunnel dell’Industrial IoT il passo successivo è quello della condivisione, vale a dire dell’interconnessione di macchinari, impianti e sistemi diversi. Questa è la fase in cui trovare un meccanismo di trascodifica dei diversi protocolli e linguaggi che convivono nelle operations di una attività. Le piattaforme open protocol possono essere di aiuto.
Customizzazione: una volta che i diversi asset sono messi in condizione di interagire, si può pensare alle peculiarità di ogni organizzazione. Ad esempio, alla veicolazione di informazioni diverse ai differenti stakeholder in azienda (una dashboard sintetica al board di una multiutility, e una vista specifica su un ramo degli impianti all’addetto di zona responsabile delle manutenzioni). Oppure all’introduzione di un protocollo speciale e tipico di una attività, oppure all’integrazione di uno specifico CRM.
Infine, la correzione. Il fine ultimo delle tecnologie di Industrial IoT è proprio quello di migliorare le business performance. I dati, di per sé, servono a poco se non diventano input per decisioni aziendali che migliorino efficienza, produttività, sostenibilità e customer experience. In questa prospettiva, la forza di IoT sta anche nella possibilità di innescare azioni correttive automatizzate: ingaggiare una squadra di manutenzione prima che si verifichi una perdita, riordinare componenti / materiali prima che si vada in rottura di stock, dare feedback agli uffici R&D su un determinato comportamento di un macchinario connesso, abbassare il riscaldamento una sala riunioni quando nessuno la occupa, ottimizzare la rotta di un cargo in funzione delle condizioni ambientali.
La squadra IoT, fattore critico di successo
Accenture sostiene che il 76% dei manager concorda sul fatto che, nei prossimi cinque anni, gli ecosistemi saranno i principali agenti del cambiamento. Vale ancor di più in ambito di Industrial IoT, in cui le applicazioni sono per definizione multifunzionali, coinvolgono varie tipologie di stakeholder e, per essere parte del business, devono necessariamente integrarsi con i sistemi esistenti. Nella nostra esperienza, il successo di IoT passa dal mettere insieme questo assetto di lavoro: diversi partner, con diverse competenze che rientrino in un’ottica di ecosistema che racchiude anche il cliente, un progetto comune. Quali sono questi partner e che ruolo hanno? I vendor di tecnologie, che sicuramente hanno il ruolo di abilitatore. Le società di consulenza, che possono condurre le imprese verso la trasformazione digitale da un punto di vista strategico e svolgere un ruolo di evangelist e change agent. I system integrator, che hanno il compito fondamentale di calare IoT nei sistemi e processi aziendali. E, non ultimi, gli installatori evoluti; questo ruolo può in parte coincidere con i system integrator oppure risiedere all’interno di un terzo soggetto; non va dimenticato però che, a differenza di altre applicazioni, i progetti IoT riguardano il campo. È necessario mappare siti produttivi, configurare reti, dispositivi, aggiornare i firmware dei gateway da remoto, il tutto in ambienti spesso difficili e caratterizzati da fermi macchina il più delle volte inesistenti: acciaierie, produzione, etc… Pensiamo che questo sia stato fino ad ora l’anello debole della catena, la frontiera su cui molti proof of concept si sono arenati. Integrare sin dall’inizio nei team la parte di campo è garanzia di successo fattivo delle applicazioni.
Tre modi per favorire e facilitare la convergenza IT-OT
Questa è la sfida principale dell’Industrial IoT. Detto con un esempio, raccogliere i livelli delle scorte (mondo OT, tramite un sensore sul campo) e non poterle riordinare (mondo IT, tramite un ERP) compromette il fondamento stesso delle applicazioni IIoT. Rispetto a questo tema, ecco tre best practice che hanno dato dei risultati.
Ingaggiare le persone giuste
Una applicazione IoT non riguarda solo un CIO. Né solo un responsabile delle manutenzioni. Né solo un Innovation Manager. Il cliente di una applicazione IoT non è mai uno, ma tanti, tipicamente distribuiti in diverse funzioni aziendali, a partire dal CEO, che dovrebbe trainare la trasformazione digitale. Creare sin dall’inizio la squadra giusta, coinvolgendo almeno una persona del top management, una delle operations e una dell’IT è l’impostazione giusta per realizzare applicazioni con impatto reale sul business. È un rallentatore? Forse sì, in parte, all’inizio. Ma se al tavolo del progetto, oltre ai partner tecnici, siedono queste tre figure in rappresentanza del cliente l’impatto positivo sul business è garantito.
Scegliere tecnologie serie, nate per operare in ambienti industriali
La sperimentazione dell’IoT da cantina è sicuramente un sottobosco di sperimentazione interessante, ma creare applicazioni IoT industriali con piccoli tool proprietari, solo per il gusto di risparmiare qualche migliaia di euro, è controproducente. È rischioso, perché soluzioni che non adottino un approccio di security-by-design sono più vulnerabili ad attacchi che potrebbero mettere in ginocchio le linee produttive di un manufacturer o gli impianti di un building o il servizio di una utility. È limitativo, soprattutto quando dalla fase di POC le applicazioni scalano su numeri più importanti. È riduttivo, perché probabilmente risultano non fattibili progetti che tecnologie nate nell’industria e per l’industria potrebbero supportare.
Scegliere un approccio architetturale aperto
In ambito industriale l’IoT out of the box non esiste. Al netto di una serie di standard industriali (es. MQTT, OPC-UA e Modbus per il manifatturiero, BacNet per il building e NB-IoT per le aree remote) ogni processo produttivo è diverso dall’altro: una acciaieria non è lo stesso di un’industria automotive; ogni organizzazione ha una struttura diversa: chi ha squadre di manutenzione interne e chi si appoggia a tecnici esterni; ogni applicazione deve interconnettersi con ERP o sistemi differenti, chi SAP chi Dynamics; ogni azienda ha le proprie policy infrastrutturali, chi è ormai cloud native, chi lavora on premises. Per di più, l’evoluzione tecnologica è velocissima e vincolarsi a una scelta tecnologica è rischioso. Per questo le tecnologie e le architetture aperte che dialogano via API sono una buona scelta per tutelarsi da rischiosi lock-in che potrebbero ingessare l’innovazione.