- La manutenzione predittiva o predictive maintenance è un’attività che si basa sull’analisi dei dati raccolti dai macchinari al fine di è prevedere quando un componente o un sistema potrebbe guastarsi.
- Startup come Quick Algorithm stanno sviluppando soluzioni di monitoraggio intelligente che utilizzano sensori IoT per prevenire guasti nei macchinari. Progetti innovativi come GD 4.0 di Dradura Italia puntano a migliorare l’efficienza e ridurre l’impatto ambientale dei processi industriali.
- L’implementazione di sistemi di manutenzione predittiva porta vantaggi economici significativi, come la riduzione dei costi operativi e dei tempi di fermo e miglioramenti nell’efficienza operativa.
Industria 4.0
Manutenzione predittiva: cos’è e quali sono le sue applicazioni
La manutenzione predittiva si basa sull’analisi dei dati raccolti dai macchinari, al fine di convertire tali informazioni in un valore che possa contribuire al miglioramento della produttività degli stessi, ridurre i rischi connessi a un potenziale malfunzionamento e minimizzare l’impatto dei costi di manutenzione
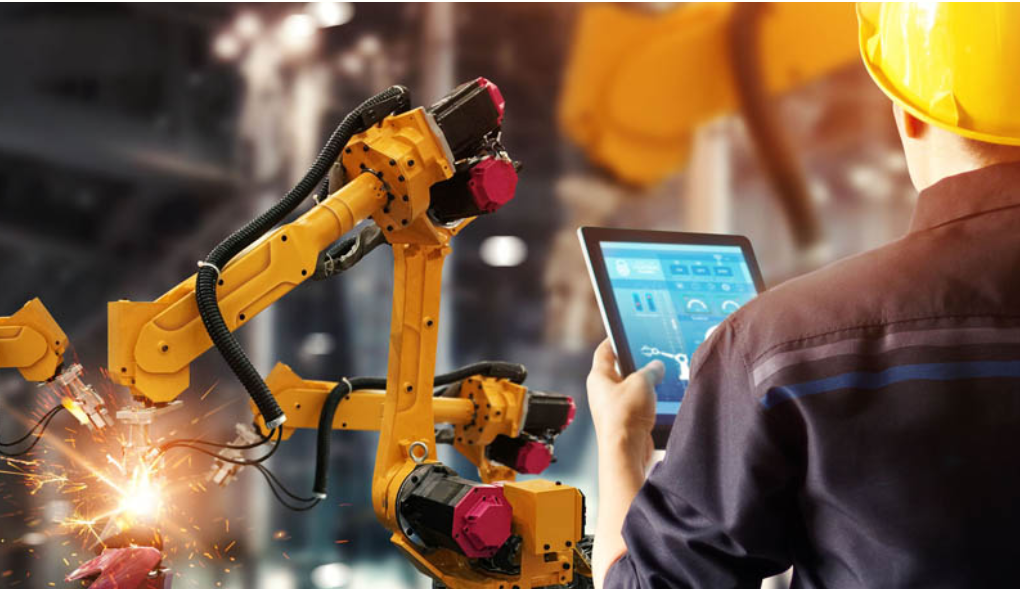
Continua a leggere questo articolo
Aziende
Argomenti
Canali
Speciale Digital Awards e CIOsumm.it