Cos’è la predictive maintenance
La predictive maintenance, in italiano manutenzione predittiva, è un tipo di manutenzione basato sull’IoT Analytics, l’analisi dei dati generati dalla rete connessa di dispositivi fisici abilitati ad Internet. I dati forniti dai sensori posti sul macchinario o sulla linea dell’impianto vengono elaborati da appositi software che consentono di “predire” un guasto, quindi intervenire prima che si verifichi.
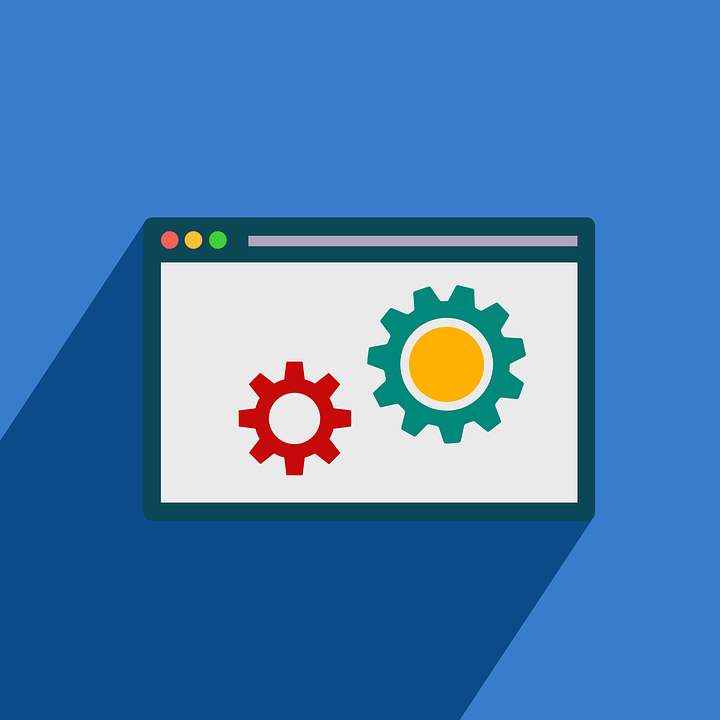
I software (tra i più comuni, i CMMS – Computer Computerized Maintenance Management System) sono basati su algoritmi di machine learning, apprendimento automatico: la “macchina” (il sistema informatico) “apprende” a correlare i dati ricevuti e a riconoscere schemi ricorrenti, quindi a segnalare eventuali anomalie rispetto agli schemi appresi o al superamento di “valori soglia”.
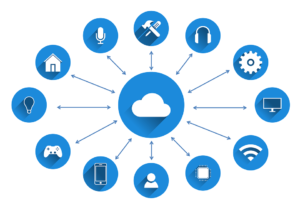
La manutenzione predittiva è l’evoluzione della manutenzione su condizione – Condition Based Maintenance proprio perché si esegue a partire dal monitoraggio in tempo reale delle condizioni delle attrezzature e degli impianti grazie alle soluzioni IIOT.
Qual è la differenza tra la predictive maintenance e la manutenzione preventiva
La manutenzione preventiva, o pianificata, viene anche detta “Time-Based Maintenance” perché si basa su una programmazione temporale che stabilisce i componenti critici da revisionare e/o sostituire (es. tagliando auto). La manutenzione preventiva è fissata “a priori”, quindi non sempre tiene in considerazione la specificità del macchinario, del processo o dell’impianto: nel momento in cui viene effettuata, da calendario, può non essere necessaria o arrivare in ritardo rispetto ad un guasto già avvenuto.
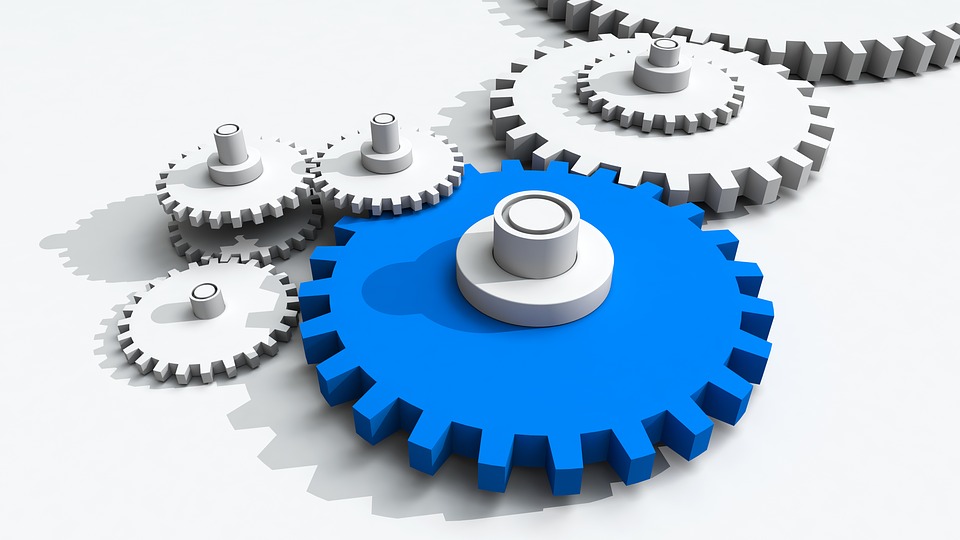
La manutenzione predittiva invece è frutto del monitoraggio costante, “sul campo”, dello specifico macchinario, della specifica linea di produzione, grazie ai sensori che generano dati unici, come unica è la storia dell’impianto a cui si riferiscono. L’elaborazione e l’analisi compiute dai software sono “su misura” rispetto alla realtà monitorata, così come le previsioni fornite su un possibile guasto o sulla vita residua di un macchinario e i relativi alert. La programmazione dell’intervento di manutenzione diventa più flessibile e più aderente alle reali necessità dell’impianto.
Quali vantaggi porta alle aziende
La manutenzione predittiva consente di ottimizzare tutte le operazioni di manutenzione con notevoli vantaggi in termini di riduzione dei costi e aumento della produttività.
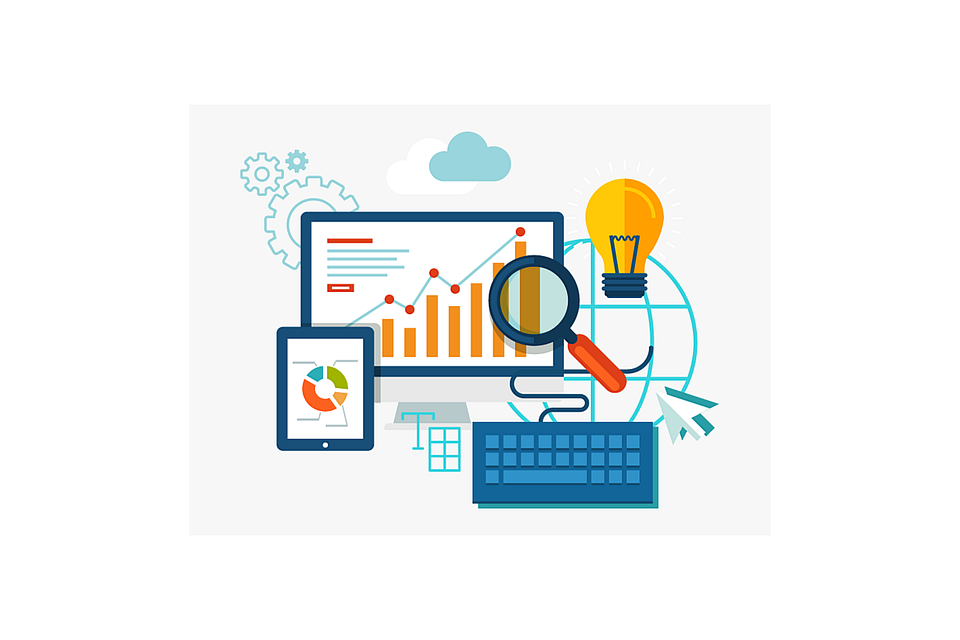
Un sistema di manutenzione predittiva, personalizzabile a seconda delle esigenze, può automatizzare la maggior parte dei processi di gestione della manutenzione, con risparmi considerevoli di tempo e risorse.
Intervenire solo se e quando serve comporta infatti la riduzione dei fermi macchine, dei costi di manodopera nonché di ricambio dei macchinari, con un conseguente incremento della continuità produttiva e dei ricavi.
Da non trascurare il miglioramento della sicurezza dei lavoratori, allertati in tempo utile di possibili anomalie, che comporta la riduzione del rischio infortuni e una migliore compliance normativa.
Il piano di manutenzione predittiva viene elaborato secondo le priorità aziendali e valutato secondo KPI-Key Point Indicator condivisi, dal tempo medio di malfunzionamento o guasto per le macchine (MTBF) al tempo medio di riparazione (MRT) o ripristino (MTTR) fino all’impatto dei costi di manutenzione e fermo macchine su produzione e fatturato: l’elaborazione di questi dati facilita la gestione degli ordini di lavoro generati da richieste di intervento con procedure chiare e assegnazioni automatiche. Inoltre, consente una migliore gestione del magazzino con il calcolo automatico dei tempi di approvvigionamento e gli avvisi di allerta automatica quando la soglia minima dei livelli di scorta dei pezzi di ricambio viene superata.
Il monitoraggio costante dei macchinari e delle linee di produzione consente di tracciare uno “storico” utile per capire, ad esempio, le più frequenti cause di fermo, correlarle a dei parametri e “prevedere” fermi futuri.
La reportistica accessibile in tempo reale è un valido strumento di supporto alle decisioni del management aziendale.