L’industria manifatturiera, uno dei pilastri dell’economia europea, con 2 milioni di imprese e 33 milioni di posti di lavoro, può fare un salto di qualità sfruttando le opportunità che le tecnologie digitali possono offrire. L’Europa ha le competenze su Big data, IoT, sui sistemi cyber-fisici, la robotica per creare leadership in ambiti come la fabbrica automatizzata, il software di impresa, la robotica industriale, la manifattura basata su 3D e laser. Ma per garantire la propria competitività, i Paesi dell’Ue devono mantenere una forte base industriale e gestire la transizione alla manifattura intelligente e all’economia basata sui servizi, digitalizzando tutti i settori. Il 75% del valore aggiunto dalla digital economy verrà infatti dalle industrie tradizionali più che dalle imprese Ict, ma l’aspetto più critico sarà proprio l’integrazione delle tecnologie digitali in queste imprese.
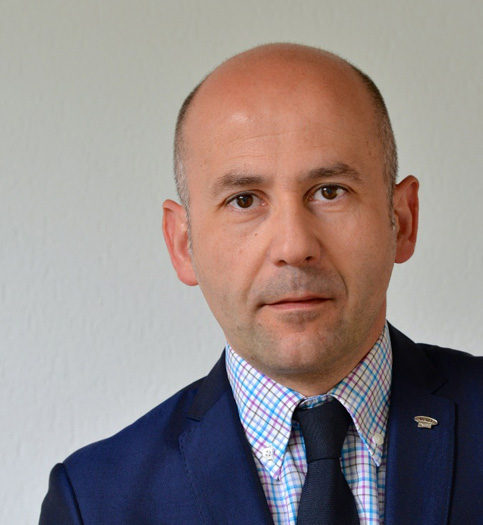
Gianluca Giovannetti, Cio di Amadori
“Il settore manifatturiero ha maggiori barriere all’ingresso rispetto ad altri più immateriali, dove la distruzione di valore è già avvenuta a favore di altri player – sostiene Gianluca Giovannetti, Cio di Amadori – Questo fatto può però essere rischioso: sentendoci in una comfort zone siamo portati a sottovalutare la trasformazione dei comportamenti e delle aspettative dei consumatori, gli stessi che oggi cambiano banca o provider di servizi con estrema facilità”.
Anche l’industria manifatturiera dovrebbe dunque tenere le “antenne dritte” perché da una lato quanto è avvenuto negli altri settori colpirà anche questa industry e dall’altro cogliere le opportunità che la digitalizzazione offre. Secondo una stima di Cisco Consulting Services, il risultato della digitalizzazione per una grande azienda manifatturiera che abbia un fatturato di 20 miliardi di dollari si traduce in un incremento dei profitti del 12,8% nei prossimi tre anni e del 19% nei prossimi dieci anni. Il 79% delle aziende coinvolte in uno studio della stessa Cisco che ha coinvolto 625 responsabili nel settore manifatturiero in 13 paesi, fra cui l’Italia, ritiene che la digital disruption avrà un impatto significativo sulle loro aziende nei prossimi tre anni, ma molte imprese del manifatturiero hanno difficoltà nella transizione verso nuovi modelli di business a causa della complessità del mercato o per la mancanza di competenze digitali al proprio interno. Il principale ostacolo verso la transizione a un modello centrato sui servizi è la difficoltà di gestire contemporaneamente i due fronti: quello sul versante dei prodotti e quello sui servizi.
Indice degli argomenti
Una fabbrica intelligente per creare prodotti e servizi intelligenti
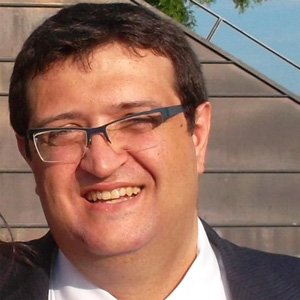
Gianbattista Gruosso, professore del Dipartimento di Elettronica e Informazione, del Politecnico di Milano
“La fabbrica intelligente, capace di gestire flussi di informazioni verso e dall’esterno, consente di creare prodotti intelligenti che possono abilitare i servizi – ha sottolineato Gianbattista Gruosso, professore del Dipartimento di Elettronica e Informazione, del Politecnico di Milano, in occasione del seminario “Smart Manufacturing, produzione e trasformazione digitale” di Dassault Systèmes – Creare servizi presuppone la riorganizzazione dell’azienda per poterli erogare: raccogliere i dati, gestire le informazioni, dotarsi di sistemi per gestire i contenuti e soprattutto creare cultura all’interno dell’azienda per abilitare processi collaborativi”. Un modello assimilabile a una rivisitazione in chiave moderna dell’artigianato per i forti contenuti di personalizzazione, creatività e interazione con l’ecosistema del consumatore.
Un esempio di successo è quello dei produttori di macchine industriali che sfruttano i servizi per creare modelli di business innovativi, che prevedono di farsi pagare in base a risultati concreti (ad esempio l’effettiva disponibilità degli impianti, se un impianto è fermo per un guasto non si paga), proprio come oggi si fanno pagare per i prodotti venduti. Grazie all’intelligenza dei prodotti e alla loro connessione, è possibile, ad esempio, utilizzare strumenti di manutenzione predittiva e controllo di performance as a service, che consentono di ridurre i down-time. Il produttore può così ottenere compensi ricorrenti commisurati alla disponibilità delle macchine. Le aziende che non sfruttano i servizi per ottenere fonti di ricavo ricorrenti rischiano invece di non stare al passo con uno scenario di mercato sempre più dinamico e competitivo. Secondo lo studio Cisco, l’86% delle aziende del settore manifatturiero considera centrale per la propria crescita una strategia che preveda un’evoluzione dei modelli di ricavo dagli attuali, centrati sul prodotto, a modelli orientati al servizio. Ma solo il 29% si aspetta che l’offerta di servizi cresca più rapidamente dei prodotti nell’ambito del proprio business. Gestire l’impatto della digitalizzazione nel manifatturiero non è banale, secondo Giovannetti, visto che richiede sia un intervento rivolto all’esterno verso il consumatore finale sia verso l’interno per ripensare i processi produttivi e organizzativi, per capire dove la digitalizzazione possa essere un acceleratore, uno strumento di recupero di efficienza, un elemento di ulteriore competitività. “La vera sfida è la realizzazione dello smart manufacturing che, uscendo dagli slogan, significa ripensare sales, operation planning, supply chain, operation, una scommessa grande che pone un grande problema di skill”, aggiunge Giovannetti, il quale suggerisce di creare le competenze partendo da lontano: da un lato reclutando giovani talenti e dall’altro aprendosi per abbracciare processi in grado di costruire ecosistemi per l’innovazione. Tutto questo richiede anni per realizzarsi: “Si tratta di trasformazioni che impiegano tempo per realizzarsi – sottolinea e suggerisce il Cio di Amadori – Il tema della digitalizzazione del manifatturiero dovrebbe diventare centrale nei piani industriali, visto che l’Italia è il secondo paese manifatturiero a livello europeo”.
Una strategia industriale basata sulla trasformazione digitale è stata da tempo avviata dalla Germania con Industrie 4.0, un programma ministeriale con l’obiettivo di rilanciare e far diventare competitivo il manifatturiero tedesco e punta alla leadership della Germania sulle tecnologie e sui processi, come ha ricordato Gruosso che per questa ragione ritiene più appropriato parlare di fabbrica intelligente. “Il modello di fabbrica intelligente può essere compreso per analogia con il comportamento di uno stormo – ha spiegato – I singoli componenti sono intelligenti e autonomi all’interno di un’organizzazione che abbandona il modello piramidale a favore di un controllo distribuito e processi molto più fluidi, grazie a un aumento dei canali comunicativi e collaborativi”. Ad esempio se un singolo operaio introduce migliorie di processo direttamente sul flusso di prodotto, può trasmettere le informazioni, attraverso software e strumenti dedicati, direttamente alla progettazione, alla qualità o al marketing, a seconda della competenza su quell’aspetto.
Secondo Gartner Industrie 4.0 è un’iniziativa ambiziosa che offre grandi promesse ma rappresenta un salto quantico per molte organizzazioni. “Crediamo che per i Cio sarebbe meglio interrompere il grande sforzo richiesto da Industrie 4.0 dedicandosi ad aspetti più contenuti e gestibili, concentrando i loro investimenti su piccoli passi incrementali”, sostiene Stephen Prentice, VP di Gartner. Questi i passi identificati dall’analista: combinare i dati che provengono da sorgenti esterne e interne per migliorare le decisioni, creando un feedback circolare per migliorare i disegno dei prodotti e dei processi; sviluppare competenze e fiducia reciproca per integrare It e operation (OT) all’interno dell’organizzazione, inclusa l’integrazione della sicurezza e del risk management all’interno di entrambi i domini; fare l’inventario del support It esistente per la fabbrica e identificare dove sia necessaria un’ulteriore digitalizzazione; capire come le tecnologie sottostanti di Industrie 4.0 possono impattare su una scelta di localizzazione (in alternativa alla globalizzazione) delle operazioni di fabbrica per determinare il tradeoff ottimale fra costo, innovazione e fornitura. Il caso Alstom evidenzia per esempio come la digitalizzazione e l’ottimizzazione del technology transfer possa consentire di realizzare stabilimenti locali di assemblaggio più snelli e, di conseguenza, ridurre notevolmente i costi.; lavorare in direzione dello sviluppo al tempo stesso di prodotti intelligenti e processi intelligenti di produzione, ma su una base focalizzata e incrementale dove l’investimento può essere chiaramente giustificato e i benefici evidenti.
Le tecnologie in campo
Le aziende manifatturiere su cui si è basato lo studio Cisco hanno indicato, come tecnologie digitali che avranno il maggiore impatto sulla produzione industriale nei prossimi tre anni, il cloud (37%), Internet of Things (33%) e analytics (32%), mentre non sono state particolarmente evidenziate tecnologie tipicamente “manifatturiere” come la robotica o la stampa 3D e così via. Risultati non dissimili sono evidenziati da un’indagine del Politecnico di Milano condotta fra le aziende manifatturiere italiane. Queste considerano tecnologie disruptive il cloud (quasi 75%), le nanotecnologie (circa il 50%), la stampa 3D (55%), mentre un terzo ritiene l’IoT disruptive e il 50% lo considera interessante, ma non chiaro; stesso giudizio per il 75% in relazione al social. Le posizioni cambiano sensibilmente quando si va a verificare cosa effettivamente si utilizza o si sta valutando. Solo la stampa 3D supera il 50% sommando utilizzo effettivo e fase di analisi, mentre il cloud è in fase di analisi solo per il 25% e non utilizzato dal 50% e social in fase di studio per il 50%. “Per assurdo le tecnologie più conosciute sono le meno utilizzate”, commenta Gruosso. È evidente che si tratta di progetti ancora immaturi dove il Cio abituato a mettersi in gioco, e non a stare in difesa, può giocare un ruolo di primo piano. “Lo smart manufacturing può rappresentare un elemento di snodo nevralgico, attorno a cui possono nascere iniziative e progetti per definizione non strutturali e con modalità organizzative non definite”, sottolinea Giovannetti.
Per maggiori informazioni: IoT, il mercato in Italia e gli strumenti del fare