In un contesto di incertezza economica, globalizzazione, cicli di vita dei prodotti sempre più brevi e compliance sempre più severe, le aziende manifatturiere nei processi operativi sono chiamate a reagire in tempo reale alle eccezioni, e nel contempo a ottimizzare le performance. Secondo Aberdeen Research, per rispondere nel modo migliore a queste due sfide occorre una gestione unificata di asset, produzione, qualità e magazzini nei vari stabilimenti: tesi di cui la società di ricerca ha cercato conferma con un’indagine su oltre 200 aziende manifatturiere di ogni dimensione in tutto il mondo.
Il primo responso è che la principale priorità di business è nettamente la riduzione dei costi (77%) che, parlando di aziende manifatturiere, si concentra soprattutto sulle attività operative con una serie di best practice (figura 1).
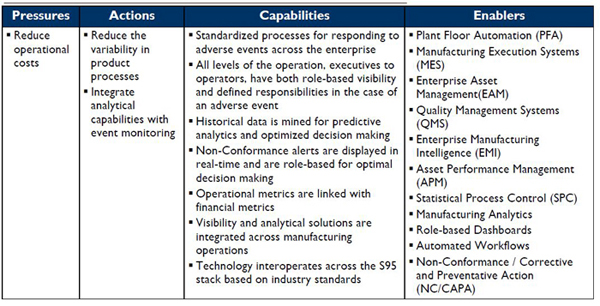
Figura 1 – Lo scenario strategico (Pressures, Actions, Capabilities, Enablers) per le imprese Best-in-class
Aberdeen quindi prima di tutto definisce tre Kpi: Otd (On Time Delivery: percentuale di prodotti consegnati entro la scadenza promessa al cliente), Oee (Overall Equipment Effectiveness, un indice che tiene conto della disponibilità degli impianti e della qualità dei loro output) e Oy (Overall Yield: rapporto tra il volume di produzione reale e quello ottimale ottenibile con gli stessi input). Quindi esamina le prestazioni del campione su questi tre indici, e classifica il primo 20% di imprese come Best-in-class, il seguente 50% come Average (prestazioni medie) e l’ultimo 30% come Laggard (ritardatari). In media, le Best-in-class hanno prestazioni migliori di circa 20 punti rispetto alle Laggard: 97% contro 78% sull’indice Otd, 91% contro 70% sull’Oee, e 98% contro 76% sull’Oy. Ma l’aspetto più interessante è la relazione diretta dimostrata da Aberdeen tra le performance sui tre Kpi e la profittabilità: le Best-in-class hanno margini operativi medi del 33% più alti rispetto alla media del resto delle aziende.
Ciascuna delle tre fasce Best-in-class, Average e Laggard, mostra poi comportamenti omogenei in cinque aree: Processi, Organizzazione, Knowledge management, Tecnologie, Performance management (figure 2 e 3).
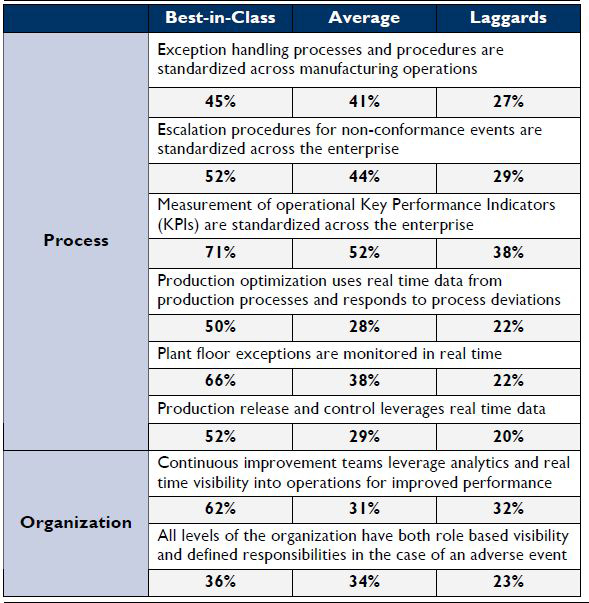
Figura 2 – Le best practice nelle aree Processi e Organizzazione
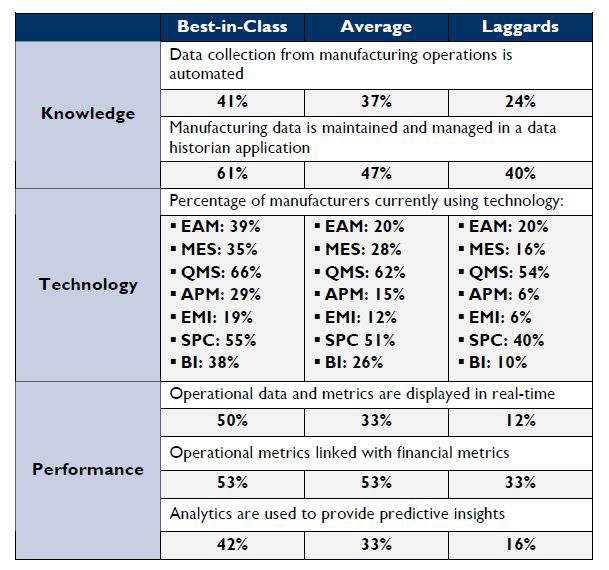
Figura 3 – Le best practice nelle aree Knowledge management, Tecnologie e Performance management
Nei processi, le Best-in-class si differenziano soprattutto per l’impegno nel ridurre le variabilità (standardizzazione) e nell’integrare controllo in tempo reale e analisi. Più in dettaglio, le Best-in-class standardizzano soprattutto le procedure di gestione delle eccezioni, l’escalation di tali eccezioni verso livelli più alti della gerarchia e la misurazione dei Kpi: “Il 72% delle Best-in-class misura l’efficienza delle macchine o i tempi di ciclo nello stesso modo nella fabbrica a Seattle e in quella in Cina”, spiega Aberdeen. Quanto all’integrazione di tool analitici e di monitoring, la rilevazione in tempo reale di eccezioni negli impianti è molto più frequente nelle Best-in-class, che usano questi dati come input per l’ottimizzazione della produzione. Qui la tecnologia ideale per Aberdeen è l’Emi (enterprise manufacturing intelligence), per ora ancora poco diffusa (è presente nel 19% delle Best-in-class e nel 6% delle Laggard) sia per la difficoltà di sfruttare insiemi di dati diversi e dispersi nei vari repository di stabilimento e aziendali, sia per la bassa conoscenza di queste soluzioni. Ben il 50% delle aziende però pianifica di adottare soluzioni Emi nei prossimi 12-24 mesi.
Dal punto di vista organizzativo, invece, le Best-in-class si distinguono per il fatto di avere team di miglioramento continuo e decisori (dagli operatori di macchina ai top manager) dotati di soluzioni di visibilità ed event monitoring dei processi. Qui rientrano anche le aree Knowledge e Performance Management, perché le Best-in-class mostrano una propensione molto più alta ad automatizzare la raccolta dei vari tipi di dati di produzione real-time, e ad analizzarli integrandoli con dati di business come quelli di contabilità industriale e di vendita.
Infine l’area tecnologie. Per avere una visibilità completa su produzione, manutenzione, qualità e magazzini, sottolinea Aberdeen, occorre un ambiente informativo capace di far interoperare in tempo reale molti sistemi It diversi: Enterprise Asset management (Eam), Manufacturing Execution System (Mes) e Quality Management Systems (Qms), a livello della gestione della produzione e dei relativi asset; Apm (Advanced Performance Management), Emi e Spc (Statistical Process Control) a livello di performance e analisi; e Business Intelligence per integrare dati operativi e corporate. Le Best-in-class in particolare investono molto di più nell’integrazione tra lo strato analisi-performance (Apm, Emi, Bi) e quello di visualizzazione; nella differenziazione delle console decisionali in funzione dei ruoli; e nell’automazione dei workflow tra le attività di produzione, magazzino, manutenzione e qualità, soprattutto per gestire le eccezioni.
l report si conclude con le raccomandazioni: ai Laggard, Aberdeen consiglia di iniziare a raccogliere dalle varie fonti tutti i dati di produzione archiviandoli in un repository (“historian”), e di standardizzare le procedure di gestione delle eccezioni. Compiuti questi due passi, si può iniziare a lavorare sui dati raccolti con soluzioni analitiche. Agli Average, il suggerimento è di investire in strumenti di Emi e Spc, ampliando la visibilità in tempo reale sui processi operativi e differenziando le relative dashboard per ruoli; alle Best-in-class è di unificare il più possibile le soluzioni di event e performance management su una unica piattaforma di Mom (Manufacturing Operations Management).