Il Supply chain management, si può definire come un “sistema di gestione della fornitura” completo, dalla fonte dei prodotti, servizi o informazioni oggetto della fornitura sino al cliente-utente finale, e che apporta valore per quest’ultimo. Questo sistema è evidentemente diverso da industria a industria e da impresa a impresa, in funzione dei processi tipici del settore d’industria e di quelli particolari delle imprese interessate. Se consideriamo ad esempio tre società, una di ‘utilities’ (elettricità, gas, acqua…) una della distribuzione (vendita al dettaglio) e una di produzione (manifatturiera, chimica, alimentare…) vediamo che oltre alle esigenze comuni per gli aspetti amministrativi, di procurement e quant’altro, avranno diversità significative dipendenti dal diverso rapporto con i loro partner a monte e con i loro utenti a valle. Considerando per semplicità solo il rapporto con i clienti, la prima, non “vede” i suoi utenti, e quindi punterà al corretto rilevamento dei consumi e alla rapida conoscenza dello stato dei pagamenti; la seconda, avendo invece con essi uno stretto rapporto, porrà attenzione ad altri aspetti, quali ad esempio il marketing; la terza infine sarà più interessata alla relazione nei suoi aspetti di procurement, di qualità dei materiali da lavorare e così via. Avremo quindi dei processi di business diversificati e di conseguenza applicazioni con caratteristiche peculiari: le verticalizzazioni.
L’Scm in rapporto agli altri processi di business
Un processo di Scm implica la continuità della relazione tra i componenti della catena del valore, ed è in questa prospettiva che diventa indispensabile poter interagire con gli altri processi di business che riguardano l’operatività di ogni singola impresa della catena, dal calcolo dei fabbisogni, alla gestione della domanda, alla produzione e via via fino ai processi più tipicamente amministrativi
L’interazione verso l’esterno (clienti, fornitori e partner), assume poi il profilo della relazione quando da un semplice rapporto di domanda e offerta si espande a comprendere forme di collaborazione nello scambio d’informazioni, quali le previsioni di domanda e i contratti quadro, che investono non solo aspetti amministrativi ma anche di pianificazione. Questa relazione può anche maturare in rapporti relativi al contenuto (ad esempio, la progettazione congiunta per l’ingegnerizzazione del prodotto), il tutto sempre a comune vantaggio degli attori coinvolti. Non a caso alcuni parlano, anziché di ‘supply’ di ‘value’ chain management, proprio per evidenziare il concetto di un valore che non è solo per l’utente finale, ma è un vantaggio distribuito, sia pure in modo diverso, su tutti gli attori della catena.
Il fenomeno di apertura del rapporto lungo la catena dei fornitori che sfocia nell’Scm si sviluppa dopo quello, rivolto all’interno dell’impresa, che dà origine all’Erp. Ed entrambi, Erp ed Scm, si sviluppano comunque prima del Crm, relativo alla gestione del rapporto di relazione con i clienti a sostegno del mercato, fenomeno che nel suo aspetto di “relationship” si trova applicato anche al rapporto con i partner. L’automazione dei processi di business si è rivolta quindi prima all’interno dell’impresa (anni ‘60 e ‘70 in Italia), poi alla relazione tra questa e i suoi fornitori (anni ‘80 e prima metà anni ‘90) e successivamente alla relazione con i clienti e il mercato (dalla seconda metà anni ‘90 ad oggi). In queste ultime due fasi si razionalizza ed ottimizza anche il processo della logistica che da una prima fase di attenzione rivolta all’interno dell’azienda (movimentazione dei materiali) si estende a considerare le consegne e il ricevimento (logistica intera).
I tempi di consegna si sono ridotti del 10% e gli inventari dei componenti dePartner e funzioni di un sistema di Supply chain management
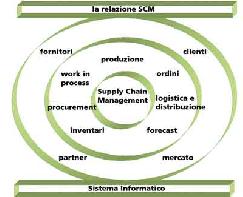
fonte:ZeroUno 2004
Fornitori ed acquirenti: alla ricerca di un equilibrio
L’evoluzione dell’Scm è marcata da precise definizioni. Una prima fase si può identificare con il periodo del calcolo dei fabbisogni dei materiali (Mrp, Material requirements planning) per ottimizzare acquisti e inventari all’interno all’azienda, ma dove era già implicita l’esigenza dell’inizio del rapporto con la catena dei fornitori. Questa prima fase era anche estesa alla pianificazione del fabbisogno di risorse (macchinari, spazi, personale e così via.).
Una seconda fase è quella dell’Eoq e dell’Moq (Economic order e Minimum order Quantity). La prima è la quantità necessaria al cliente, e determina quanto è di sua convenienza procurarsi in base alle sue esigenze. La seconda riguarda invece i processi di business del fornitore, che tenendo conto della sua convenienza a produrre in funzione della sua struttura d’impresa mira ad ottimizzare i costi e il sistema di produzione. Moq ed Eoq si contrappongono quindi in una logica dialettica, ed è in questo momento che emerge il primo tentativo di razionalizzare, tra acquirenti e fornitori, almeno la gestione degli inventari. In questo tentativo si evidenzia la divergenza d’interesse tra le parti, tanto maggiore quanto più sono rigidi i sistemi di produzione dei partner coinvolti. L’Scm non è quindi solo un fatto di gestione degli ordini o d’integrazione delle informazioni, ma anche un fatto di gestione del sistema della produzione. A livello di Eoq/Moq il focus del sistema di gestione riguarda particolarmente lo stato degli inventari. Questi sono sempre stati di difficile ottimizzazione in quanto i componenti fast-moving (pensiamo ai prodotti deperibili), si avvantaggiano dell’equilibrio tra l’ordine minimo e l’ordine economico grazie all’elevata movimentazione in ingresso e in uscita, mentre alla gestione dei prodotti slow moving (come i beni industriali) il calcolo dell’Eoq e dell’Moq non apporta che minimi vantaggi.
L’Ict base tecnologica della catena di interessi
Negli anni ’70, essendosi oramai dimostrati i vantaggi di efficienza e di efficacia derivanti dall’automazione dei processi rispetto alla loro esecuzione manuale, i responsabili Edp delle imprese più avanzate (e anche dotate di un maggior peso contrattuale nei confronti del loro partner) iniziavano ad avviare accordi unilaterali con i maggiori fornitori per scambiarsi in modo semi automatico le informazioni. Ma è negli anni ‘80 che si sviluppa ed emerge l’Edi (Electronic data interchange) che introduce uno standard di comunicazione tra i sistemi Ict dei partner, conseguendo una semplificazione ed un’uniformità rispetto ai precedenti modi di operare. L’Edi evidenzia subito sostanziali problemi di accettazione da parte delle imprese minori della catena della fornitura; è solo il potere prevalente, quando non di imperio, dei grandi costruttori a contribuire all’implementazione dell’Edi anche presso i piccoli costruttori e che rende il sistema accettabile a questi ultimi. Un approccio che, peraltro, anche oggi sostanzialmente non è cambiato e si sta ripetendo con l’applicazione delle tecnologie RFId, per l’identificazione dei prodotti via radio, di cui parleremo più avanti e che saranno oggetto di un approfondito servizio previsto nei prossimi numeri di ZeroUno.
L’industria automobilistica è stata la prima ad adottare l’Edi, con sistemi e standard suoi specifici che sono successivamente confluiti nei sistemi più evoluti in termini di contenuti e di modalità di comunicazione. quali Ansi-X12 ed Edifact.
Integrare comunicazione e processi aziendali
L’Edi, pur risolvendo problemi di comunicazione e di standard, non riesce però a risolvere gli interessi contrapposti tra le parti in catena, in particolare tra il grande e il piccolo produttore.
Negli anni ‘90 trova applicazione il concetto, nato in Giappone, del Just-In-Time, il cui scopo è di fare giungere sulla linea di produzione il componente giusto, nel luogo giusto, al momento giusto. Un concetto “dinamico” di disponibilità che supera il concetto “statico” di inventario rivolto alla pianificazione dei componenti in stock per il magazzino (o presso i fornitori esterni) e lungo le linee di produzione. In effetti questi obiettivi ambiziosi si sono poi ridotti nella realtà a garantire un rifornimento costante al magazzino, in modo da evitare la mancanza delle parti e mantenendo la continuità operativa sulle linee di produzione, senza aspirare ad una grande ottimizzazione degli inventari. Sotto il profilo dell’Ict il sistema si limitava ad una “just in time communication”, in quanto le informazioni inviate non venivano trasferite in tempo reale al sistema di gestione del ricevente e le elaborazioni, prevalentemente di tipo batch, soffrivano dei tempi dovuti alle scadenze dei lavori e dei tempi di accumulo delle informazioni tra le elaborazioni successive.
Causa di ciò erano le difficoltà derivanti dalla scarsa o nulla integrazione delle applicazioni. Possiamo quindi dire che, a questo punto della storia, alle difficoltà generate dalle diverse regole di business dei produttori e dalla diversa dimensione dei costruttori, si aggiungono quelle conseguenti alla difficoltà di integrazione delle applicazioni sui sistemi informatici.
Ma queste difficoltà e questi limiti sono superabili se la relazione lungo la catena viene vista nell’ottica del vantaggio reciproco e della collaborazione. Ed è questo il vero aspetto nuovo: un cambiamento di mentalità nella cultura del rapporto di relazione che, lungi da ogni ottica entusiastica ed emotiva, deve, con concreto senso del business, almeno prendere in considerazione il “vantaggio reciproco” della collaborazione.
Lo stato odierno e le prospettive emergenti
Oggi le aziende più qualificate operano con un modello d’integrazione delle applicazioni che rappresenta un affinamento del Just in Time, ovvero con il Just In Sequence. Questo prevede la consegna sul posto di lavoro dei pezzi nella sequenza necessaria nel momento in cui occorrono e, dove è stato implementato con successo (vedi ad esempio il caso-utente Lear Corporation, pubblicato su Prospettive’, supplemento a ZeroUno n 261) è in grado di reagire in tempi variabili dai 10 ai 20 minuti ad un eventuale cambio dei programma delle lavorazioni.
Le difficoltà tecniche di natura Ict connesse a tale modello sono superabili, nella grande maggioranza dei casi, grazie alla capacità di integrazione delle applicazioni e dei sistemi oggi disponibili, che vanno dal semplice Edi su protocolli Internet ai più complessi ed avanzati servizi Web.
Il rapporto tra i partner della supply chain può essere valutato in funzione del livello di penetrazione dell’informazione che dal partner a valle della catena va al sistema informatico del partner a monte. Questo livello cresce in contenuto da una semplice gestione amministrativa degli ordini fino alla pianificazione e all’esecuzione delle operazioni, secondo le esigenze specificate dai parner coinvolti (tipo d’imballaggio, qualità dei lotti, livello tecnico richiesto, disposizioni di trasporto, quantità delle consegne parziali e così via). E’ intuibile che più tale penetrazione è spinta, più le applicazioni dei partner vanno verso la verticalizzazione, per rilevare, comunicare, elaborare e gestire in modo adeguato le informazioni relative alle esigenze specifiche del rapporto Scm in atto.
Ad un livello sempre più elevato d’integrazione, un ordine verrà gestito nel processo di business dei partner della supply chain in maniera diversa a seconda che sia originato da una richiesta di parti di ricambio (attenzione al livello tecnico e all’urgenza), oppure che sia il primo ordine di un cliente nuovo (attenzione a tutto il ciclo dell’amministrazione e della pianificazione della produzione) o ancora ad un ordine di parziale consegna all’interno di un contratto quadro già emesso ed elaborato (attenzione limitata all’amministrazione, imballaggio, spedizione e trasporto).
Legare la gestione delle informazioni a quella dei materiali
Il fondamento per un efficace sistema di Supply chain management dipende dalla capacità di gestire da un lato le informazioni e dall’altro i componenti fisici della catena (materiali, semilavorati, prodotti finiti), in modo da sapere dove si trovano, in quale quantità, di quale livello qualitativo e così via. Purtroppo, non è raro che il riferimento reciproco tra il sistema virtuale (la trasmissione delle informazioni) e quello reale (la movimentazione delle cose) s’interrompa, con tutte le conseguenze del caso. Ad evitare questi inconvenienti, e quale parte integrante del processo di Scm, intervengono i sistemi di etichettamento, o “tagging”. In quest’area vi è stata la rivoluzione dei codici a barre e, attualmente, è in atto quella dei sistemi di identificazione via radio (RFId, Radio Frequency Identification), che consentono in maniera sempre più efficace e certa di rilevare l’ubicazione dei materiali. Infatti la tecnologia RFId permette non solo di realizzare, analogamente alle tecnologie precedenti, un sistema passivo, ma anche un sistema attivo, che segnalando i movimenti dei materiali al software di Scm aumenta il grado di coincidenza della gestione delle informazioni con quella delle cose.
Un caso significativo di soluzione RFId in fase di realizzazione è quello di Wal-Mart, che ha lanciato l’ambiziosa iniziativa di chiedere ai suoi 100 principali fornitori di adottare per l’inizio del 2005 etichette RFId a livello di casse e di pallet. Analogamente, ma su una scala cento volte maggiore, il Dipartimento della Difesa degli Stati Uniti ha annunciato che richiederà l’applicazione delle etichette in radiofrequenza per l’inizio del 2005 ai circa 10.000 fornitori della più grande macchina militare del mondo.
Rimane da valutare il vantaggio concreto derivante da sistemi così sofisticati, ma certi settori d’industria e certe imprese ne trovano certamente un beneficio. Estremizzando, un sistema RFId attivo permette in teoria di evitare parte della movimentazione fisica dei materiali tra i diversi depositi all’interno dell’azienda, in quanto il cambiamento di stato sul tag RFId informa il software Scm e gli operatori della nuova situazione. Questa possibilità di ‘movimentazione virtuale’ dei materiali richiede però un sistema molto efficace di gestione dei loro vari stati e un’infrastruttura Ict a prova di assoluta continuità di servizio, pena il caos più totale. Quasi a conferma della validità dell’approccio RFId, Sun Microsystem ha aperto un mese fa un centro in Scozia dove le aziende sue clienti possono provare soluzioni d’identificazione radio e verificarne la compatibilità tecnologica con i propri sistemi. Il centro aiuterà le società produttrici delle ‘etichette’ RFId, ad integrare le informazioni nei sistemi di back end e a condividerle con i partner della supply chain.
In conclusione, anche se oggi si parla molto di Scm, si tratta di un processo che è stato sempre presente nei rapporti tra le aziende nella catena della filiera produttiva e distributiva. Cresce e cambia però il livello di coinvolgimento dei partner per aumentare l’ottimizzazione dei reciproci processi di produzione, ridurre l’obsolescenza dei materiali e dei prodotti e migliorare l’efficacia dell’intera catena della produzione e della logistica. Il tutto allo scopo di ridurre i costi di ciascuna delle aziende della catena e, in ultima analisi, quelli del prodotto finale. Alcuni casi-utente in ambito manifatturiero (sintetizzati in tabella) dimostrano come da un sistema di Scm strettamente integrato ad un efficace Erp si possano sempre ottenere vantaggi oggettivi, anche se talvolta diversi dagli obiettivi che si intendeva originariamente perseguire.
Esperienze di Supply chain
CHI E COSA FANNO
Davis Controls. Distributore e assiematore di strumentazione e prodotti per il controllo della produzione
Weldon Machine Tool. Produttore di rettifiche e relative tecnologie per elevata qualità di produzione
Scotia Technologies. Lavorazioni meccaniche di precisione per industrie aerospaziali, medicali e difesa
Vicor. Convertitori di potenza build-to-order per l’industria
LE ESIGENZE
Migliorare il contatto giornaliero con i clienti rendendo disponibili ai dipendenti informazioni sui clienti, i budget, gli obiettivi e i requirement sui prodotti
Usare un sistema capace di adattarsi ai processi aziendali
Migliorare la soddisfazione del cliente
Ridurre i tempi di consegna e poter ordinare i componenti solo al bisogno
I RISULTATI
Miglioramento dei flussi di lavoro in azienda e nei rapporti con clienti e fornitori. Aumento di efficienza con soluzioni self-service operanti in real-time
Un costing accurato e che permette di usare metodologie standard; un miglioramento di competitività e maggiori margini di guadagno
Riduzione personale del 50% (da 12 a 6 persone). Gestione lavori e persone sui luoghi di lavoro