Da decenni l'It delle imprese manifatturiere sta cercando di utilizzare i dati di fabbrica insieme a quelli di business, per ricavare informazioni più complete a fini decisionali. In questo quadro, una decina d'anni fa hanno iniziato ad affermarsi le soluzioni software di Enterprise Manufacturing Intelligence (Emi), pensate proprio per aggregare dati forniti dalle fonti più disparate degli impianti produttivi, e integrarli con quelli degli altri sistemi aziendali. Ne abbiamo parlato con Pasquale Paolone, Information Solutions Sales Executive di Rockwell Automation, uno dei principali player mondiali di automazione di fabbrica e software per il manufacturing.
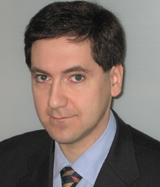
“Gli strumenti Emi lavorano su tutte le informazioni rilevanti d'impianto, provenienti da sistemi di automazione, supervisione, raccolta di dati storici di processo e di eventi (per esempio fermate di macchina), gestione qualità, Mes [Manufacturing execution systems, ndr] e anche Erp, spesso interfacciati con i sistemi di fabbrica”, spiega Paolone. “Un sistema Emi raccoglie queste informazioni, le organizza secondo opportuni modelli e le elabora restituendo indici sintetici del comportamento dell'impianto e fornendo strumenti di navigazione per il drill down dei dati e per la loro analisi”. L'analogia con la Business Intelligence (BI) è spontanea, soprattutto oggi che la BI deve affrontare l’analisi di grandi volumi di dati, sempre più frammentati e, da ultimo, in real-time. In effetti l’analisi in tempo reale fa parte della più recente frontiera della BI, mentre per l’Emi questo è sempre stato, e lo è tutt'ora, un aspetto imprescindibile: “L’Emi – spiega infatti Paolone – deve saper combinare informazioni istantanee d'impianto e dati storici, per esempio per confrontare lo stato d'avanzamento della produzione con il 'Golden Batch' [l'insieme di impostazioni d'impianto con cui si è ottenuta la produzione ottimale, ndr]”. Inoltre, sottolinea Paolone, nell'Emi è cruciale la capacità di gestire dati molto diversi: “Un'altra applicazione molto diffusa è la riduzione del consumo di energia per unità di prodotto, con input che vanno dalle distinte base alle tariffe di energia nelle diverse fasce orarie, da integrare per decidere la schedulazione ottimale di lotti e lavorazioni”.
Integrazione con l'Erp
Il prodotto Emi di Rockwell Automation si chiama FactoryTalk VantagePoint Emi, e fa parte della suite FactoryTalk, che comprende soluzioni di controllo di processo Scada, asset management di strumenti di campo e plc, gestione dei dati storici di processo, raccolta delle fermate di macchina, e Mes, nonché verticalizzazioni per vari settori. VantagePoint Emi, precisa Paolone, dispone poi di connettori verso altre soluzioni It, tra cui i più diffusi Erp: “Un esempio semplice: dalla fabbrica arrivano misure di consumo di energia e materiali, tempi di lavoro degli addetti, e tutte vanno tradotte in costi sulla base di dati contenuti nell'Erp, per decidere se, come e quando fare una produzione: l'Erp è la fonte principale per le informazioni di prodotto e di distinta base”.
Tirando le somme, l'Emi accelera la velocità di reazione rispetto a cambiamenti sia interni che esterni. “Dashboard del sistema permettono di individuare subito le criticità del processo produttivo e di analizzarne le cause, snellendo il processo decisionale e rendendolo più affidabile, perché lo basa su dati oggettivi e condivisi, e non su sensazioni o su fogli excel individuali; in modo analogo, anche rispetto all'esterno è possibile reagire subito a cambiamenti della domanda e del mercato”.
Il prerequisito principale di un progetto Emi è la chiara definizione dei suoi obiettivi di business: “Per esempio accelerare l'introduzione di nuovi prodotti o migliorare l'efficienza delle macchine o dei servizi post-vendita – sottolinea Paolone -. Questa è la parte più difficile perché occorre allineare le attese di varie aree dell'azienda”. In particolare è cruciale decidere l'ambito d'azione del sistema: “Si possono analizzare le cause delle fermate delle macchine per capire come fare meglio la manutenzione, o usare le stesse informazioni per capire la produttività dell'intero impianto e decidere dove investire per migliorarla. Per esempio in Parmalat sulla base dei Kpi sull'efficienza delle linee decidono dove e come intervenire. Oppure posso lavorare solo sulle eccezioni, impostando il sistema per inviare degli alert quando i Kpi scelti vanno fuori norma”.
Nelle aziende italiane, prosegue Paolone, “l'Emi è molto apprezzato per la visione completa dei processi e l'organizzazione delle informazioni, e anche per la capacità di eliminare la 'shadow It', cioè le soluzioni adottate fuori dal controllo dell'It”. Più in generale la tendenza è verso una maggior collaborazione tra manufacturing e It: “Tenere questi due mondi separati ormai è artificioso e non rispecchia l'evoluzione della tecnologia: il manufacturing ha capito l'importanza della strutturazione e organizzazione dei dati, e l'It ha ormai ben presente che oltre ai dati transazionali, sono decisivi anche quelli real-time di fabbrica”. Non è facile sul piano pratico realizzare questa convergenza, “ma un passo avanti per esempio è il lavoro che Rockwell Automation sta facendo con Microsoft per integrare i dati di Emi entro SharePoint, per rendere disponibili i Kpi di produzione a tutte le funzioni aziendali”.