“Nel percorso verso la trasformazione digitale l’elemento fondamentale è l’incremento del capitale umano”, esordisce Luca Luigi Manuelli, Senior Vice President and Chief Digital Officer, Ansaldo Energia (AE), intervenendo all’incontro “Industry 4.0: competere nel nuovo scenario manifatturiero”, organizzato di recente da Sda Bocconi.
La trasformazione digitale di AE va collocata all’interno dello scenario in evoluzione della power generation e delle scelte strategiche dell’azienda negli ultimi 4-5 anni “che sono state l’input per accelerare la trasformazione digitale in corso, forse inconsapevolmente, da tempo”, come sottolinea in manager AE.
Il settore dell’energia si sta muovendo sotto la spinta di alcune forze quali la decarbonizzazione, la decentralizzazione, la digitalizzazione: “Nei prossimi anni crescerà il consumo di energia, ma si modificherà la sua composizione con un ruolo centrale delle rinnovabili e prevarrà la tendenza al decentramento anche grazie alla tecnologia digitale e all’IoT- dice Manuelli – In prospettiva ciascuno di noi consumerà, produrrà, immagazzinerà e commercializzerà l’energia prodotta”.
Who's Who
Luca Luigi Manuelli
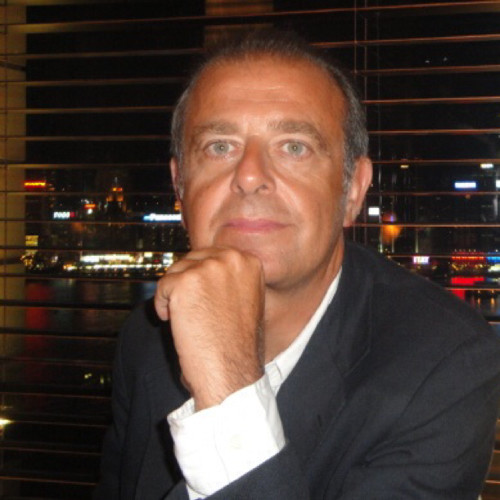
AE, nata 160 anni fa e unica azienda ancora sul mercato con il marchio Ansaldo che fino al 2014 produceva turbine su licenza, oggi, grazie ad acquisizioni (Alstom da GE) e ad accordi (Shangai Electric), produce su tecnologie proprietarie. Con centri di ricerca a Genova, in Cina, in Usa e Olanda e impianti produttivi in molti Paesi, AE è il terzo produttore mondiale nel settore della power generation, grazie a un modello integrato che va dalla progettazione e produzione di apparecchiature (turbine a gas e a vapore, generatori e microturbine) fino alla fornitura di centrali chiavi in mano.
“Attualmente la trasformazione digitale è innanzi tutto finalizzata al supporto dei processi chiave e a migliorare la competitività dei prodotti puntando all’integrazione con i servizi – spiega Manuelli – Il mercato di nuove turbine è sempre più limitato mentre il mercato dei servizi è in fortissima accelerazione anche grazie alla tendenza alla ‘servitizzazione’ (la tendenza a trasferire il valore dal prodotto al servizio, ndr), favorita dalla tecnologia digitale”.
Ansaldo Energia: il percorso degli ultimi 2 anni
L’azienda ha introdotto le tecnologie digitali più recenti in diversi ambiti all’interno di una visione complessiva di trasformazione. “Non ci siamo limitati ad aumentare la competitività, che resta il driver principale, ma abbiamo anche cominciato a ragionare su nuovi business model”, ha sintetizzato il manager AE, illustrando le novità.
Un elemento fondamentale della trasformazione in AE è il concetto di digital twin, ossia l’utilizzo della tecnologia digitale per replicare i processi industriali reali; si è anche lavorato sullo sviluppo del prodotto, con l’adozione di un PLM in grado di garantire tutto il ciclo di vita; sul manufacturing con un utilizzo intensivo dei big data; sull’attività di cantiere, dal montaggio e all’avviamento dell’impianto.
Sul tema della sicurezza si è posta una crescente attenzione per garantire la difesa degli asset industriali dai rischi che derivano dalla pervasività di connettività e IoT.
“Uno degli ambiti fondamentali di utilizzo della tecnologia è il miglioramento della sicurezza del lavoro, indispensabile anche per il dialogo con uno stakeholder fondamentale come il sindacato – aggiunge – L’attenzione riguarda tutti gli scenari operativi (fabbrica, cantieri dei nuovi impianti, service), dal controllo della postura a dispositivi di protezione individuale (DPI) alla gestione di situazioni di emergenza”.
La digitalizzazione ha investito anche lo sviluppo del prodotto, grazie al lavoro nei centri di ricerca con l’obiettivo di rendere intelligente la turbina e metterla in grado di generare le informazioni che rappresentano l’input per il miglioramento delle nuove versioni del prodotto.
A livello di fabbrica il principale elemento di novità è, non tanto la robotica o l’automazione, quanto l’utilizzo dei big data per migliorare la qualità e le prestazioni del processo, siano essi dati già esistenti o generati tramite IoT. Fondamentale anche l’utilizzo dello smart tracking, indispensabile in un processo molto complesso che necessita la sincronizzazione dei fattori di produzione.
Per supportare la progettazione e la realizzazione di centrali chiavi in mano, composte non solo da elementi come le turbine e i generatori progettati da AE, ma anche da altri componenti acquistati su specifica, è stato creato un configuratore di impianto che offre una visualizzazione reale basata sulle variabili tecniche e gestionali allineate con l’evoluzione della progettazione da parte dall’ingegneria.
“Stiamo inoltre sperimentando sistemi di ottimizzazione degli asset e IT maintenance grazie alle informazioni acquisite dai componenti intelligenti – aggiunge Manuelli – L’uso dei robot è integrato con l’attività umana. I robot sviluppati con l’Istituto Italiano di Tecnologia (IIT) sono per esempio in grado di entrare nel generatore e fare ispezioni diagnostiche senza smontare il rotore o entrare nella camera di combustione 48 ore prima di quando potrebbe fare un tecnico umano”.
Un uso alternativo è riservato anche all’additive manufacturing che viene impiegato per le riparazioni e permette il fast patching con la riduzione dei tempi da mesi a pochi giorni.
Lo sviluppo della realtà virtuale è infine dedicato soprattutto alla riduzione dei tempi necessari per il training.
Lavori in corso: i principali progetti
Due fra i progetti in corso esemplificano il percorso di trasformazione digitale di AE.
Bytes2energy va nell’ottica dell’integrazione fra prodotto e servizio: “Stiamo passando da un modello di manutenzione tradizionale, basato sulla pianificazione dell’attività, alla possibilità di acquisire le informazioni per poter intervenire quando effettivamente un componete critico della centrale rischia di rompersi – spiega – La riduzione del tempo di stop porta vantaggi a noi in termini di minori costi per la manutenzione e al cliente che riesce a evitare la discontinuità degli impianti”.
Il progetto, sviluppato in collaborazione con il Politecnico di Milano, l’Università di Genova e IIT , è stato finanziato dal MISE all’interno del capitolo Agenda Digitale (con DM15 ottobre 2014 e DM24 luglio2015), con un investimento di circa 12,5 milioni di euro per la durata di 36 mesi (2018-2020).
Il progetto in corso più significativo è la realizzazione di un Lighthouse plant. “Utilizzando le linee guida del cluster tecnologico Fabbrica Intelligente, sono stati individuati gli impianti dove si stanno raddoppiando le capacità produttive per produrre le turbine GT”, ricorda Manuelli, riferendosi ai siti produttivi genovesi di Campi e Cornigliano. Si ricorda che il Cluster Tecnologico Nazionale “Fabbrica Intelligente” è un’associazione riconosciuta dal MIUR che include imprese di grandi e medio-piccole dimensioni, università e centri di ricerca, associazioni imprenditoriali e altri stakeholder attivi nel settore del manufacturing avanzato.
Il piano R&D, della durata di tre anni a partire da luglio 2018, prevede di utilizzare per il processo di produzione tutte le tecnologie previste nel Piano Industria 4.0, con partner di ricerca come Politecnico di Milano e l’Università di Genova e partner tecnologici come Siemens, Sap, Tim, Ericsson, 5G, Leonardo.
AE investirà 14 milioni di euro con un finanziamento a fondo perduto del MISE e della Regione Liguria che coprirà il 25%, oltre alla possibilità di utilizzare l’iper e il super ammortamento previsti nel Piano Industria 4.0 (figura 3).
“Si tratta di un investimento che avremmo fatto comunque – spiega Manuelli – Il business case prevede infatti un payback di 4 anni che diventano 3 grazie ai finanziamenti e agli incentivi”.
Il progetto prevede affrontare temi quali:
- L’implementazione di una soluzione MES (Manufacturing Execution Systems)-MOM (Manufacturing Operations Management) che consentirà la tracciatura in tempo reale delle operazioni dello shopfloor officina, indispensabile per supportare un andamento del mercato molto variabile. AE prevede una media di circa 35 release di un piano di produzione, con cambiamenti drammatici del mix.
- Lo smart tracking, necessario per poter garantire la sincronizzazione tramite tecnologia digitale in una realtà che utilizza una grande quantità di materiali componenti e attrezzature.
- L’asset optimization, realizzato in collaborazione con il Politecnico di Milano, che prevede di rendere intelligenti una serie di macchine utensili per generare informazioni; questo consentirà di passare da un modello di manutenzione pianificata a uno di manutenzione predittiva.
- L’utilizzo di big data e di business analytics sia nella gestione della produzione e della qualità. La qualità sta particolarmente a cuore a Manuelli che, oltre al ruolo di Chief Digital Officer è Responsabile Qualità, IT e Miglioramento Processi. In questo campo l’obiettivo è ridurre i costi di accertamento automatizzando il processo di raccolta e in parte di analisi delle informazioni e intensificando le attività di prevenzione. “Stiamo sviluppando un algoritmo che, in funzione degli scenari commerciali e produttivi, ci permetta di valutare i componenti a maggior rischio di errore su cui indirizzare le attività di correzione”, spiega ancora Manuelli.
- Particolare attenzione sarà dedicata alla cyber security: è in fase di realizzazione una soluzione per gli Scada (i sistemi di controllo di supervisione e acquisizione dati di fabbrica) con la possibilità di replicarla e renderla portabile nelle centrali elettriche e nelle infrastrutture critiche dei clienti.
Il progetto prevede un fortissimo coinvolgimento della supply chain, sia i fornitori di macchine utensili e di attrezzature sia le PMI della filiera. “È noto il digital gap di tante aziende medio piccole, pure eccellenti nell’area di loro competenza, che vanno aiutate e supportate nella digitalizzazione”, commenta il manager AE. L’attenzione alla filiera si spinge alle startup, 160 delle quali hanno risposto alla call for innovation (Digital X Factory, 31 ottobre – 1 dicembre 2017) contribuendo con 90 proposte: 11 fra startup e Pmi selezionate lavoreranno all’implementazione del progetto.
La prospettiva è creare una piattaforma tecnologica per sviluppare digital twin con i clienti e sperimentare con loro la possibilità di gestire in modo digitale la centrale. “Non si dovranno più gestire asset fisici, ma coordinare, grazie a piattaforme integrate, il mondo della domanda e dell’offerta di energia che cambierà in modo drammatico – conclude Manuelli – Un salto non facile per un’azienda il cui mestiere attuale è soprattutto produrre turbine nel modo migliore”.
Se questa è la prospettiva. il primo obiettivo da perseguire è l’incremento delle capacità digitali delle persone, la capacità di creare per loro nuovi ruoli, imparare a lavorare in modo più agile con clienti, fornitori, PMI e startup innovative in un ecosistema 4.0.