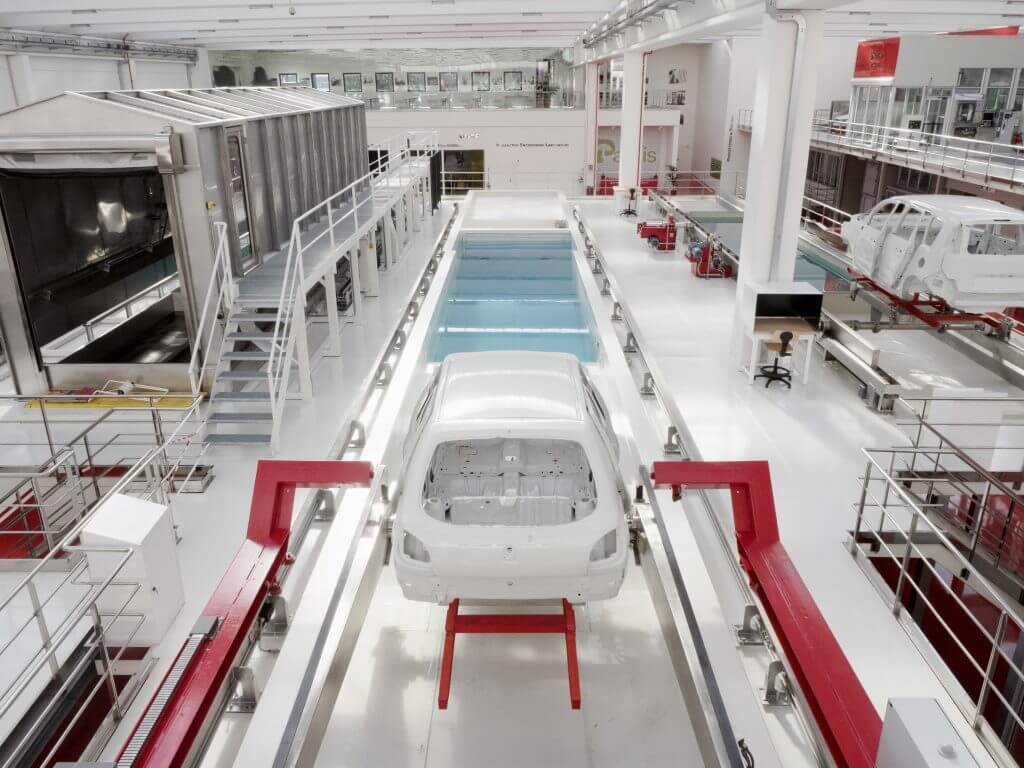
Presente sul mercato da oltre 50 anni, Geico opera come general contractor per gli impianti di verniciatura per il mercato automotive.
Impianti complessi, ci spiega Daryush Arabnia, COO della società: “Nella realizzazione di una automobile, si passa attraverso quattro impianti fondamentali. In primo luogo il PressShop, vale a dire lo stampaggio: è l’area in cui vi sono le presse per la realizzazione delle diverse forme della scocca. Si passa poi al BodyShop, per la saldatura, al PaintShop, per la verniciatura, infine l’AssemblyShop”.
In particolare, il PaintShop, l’area oggetto di questa case history, “ha la responsabilità di trattare e pulire bene le scocche che arrivano porche di oli e polveri metalliche, prima di passare alla fase vera e propria di verniciatura”.
E anche qui, si parla di cinque mani di vernice, delle quali solo una, quella del colore vero e proprio, non ha che una funzione estetica, mentre tutte le altre hanno tutte funzioni meccaniche, di protezione e sigillatura”.
Soprattutto, sottolinea Arabnia, un impianto di verniciatura, oltre a essere una struttura molto grande in termini dimensionali, gestisce situazioni complesse, con problematiche di tipo fisico, chimico, energetico: “È, di fatto, un laboratorio, che Geico fornisce chiavi in mano ai suoi clienti nel mondo”.
Indice degli argomenti
In Geico la digital transformation inizia nel 2008
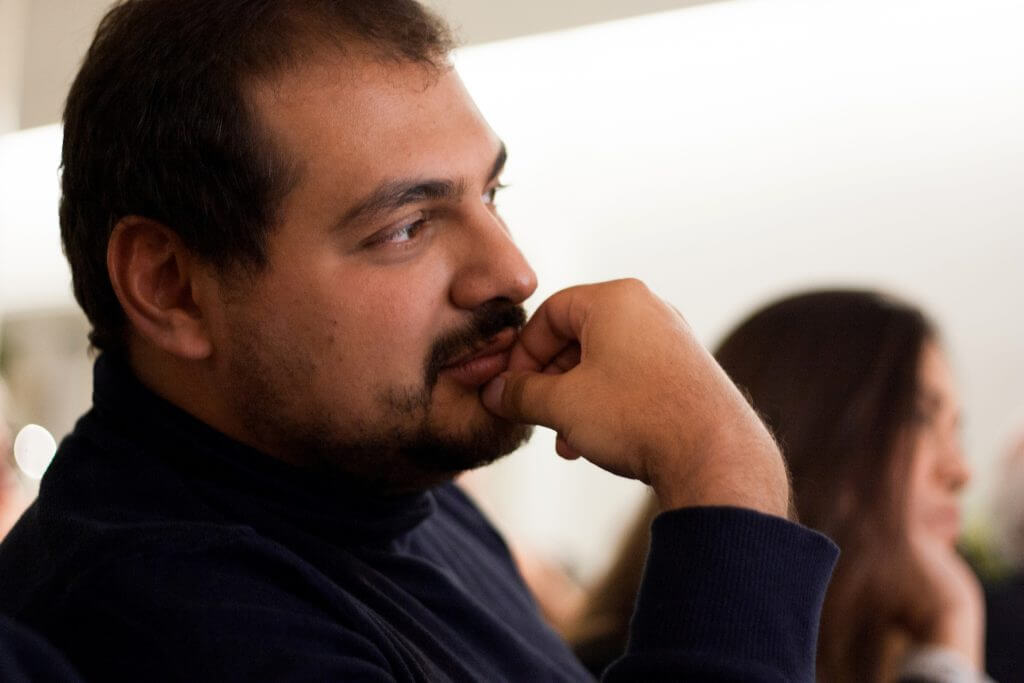
È proprio nell’ambito del PaintShop che si inserisce un importante progetto di digitalizzazione in ottica Industria 4.0 fortemente voluto da Geico.
“Si tratta del progetto Smart PaintShop, con il quale puntiamo a offrire massima flessibilità a chi gestisce l’impianto, portando IoT e intelligenza sulle apparecchiature e sui macchinari”.
La digital transformation non è una novità per Geico, che fin dal 2008 ha puntato alla digitalizzazione dei suoi impianti, ma dal 2011, anno in cui viene siglato l’accordo che porta il 51 per cento delle azioni in mano a Taikisha, colosso giapponese specializzato nella realizzazione di impianti di verniciatura delle scocche automobilistiche, sempre maggiore attenzione è stata posta ai temi dell’innovazione, della ricerca e dello sviluppo.
L’Industria 4.0 inizia dalla formazione dei dipendenti
Per quanto riguarda Industry 4.0, Arabnia sostiene che “la primissima azione che abbiamo intrapreso è stato lavorare alla formazione dei dipendenti, per creare una nuova cultura aziendale, per capire come muoversi. A novembre dello scorso anno abbiamo presentato poi il progetto Smart PaintShop, il cui lancio è avvenuto nel mese di giugno di quest’anno”.
Al progetto Smart PaintShop Geico ha destinato un team, guidato da un digital transformation manager. “Questa è una funzione che abbiamo creato in azienda sin dal 2012. Inizialmente era un IT Innovation manager, poi lo abbiamo portato a diventare digital transformation manager con un riporto non all’IT, ma all’Innovation, che a sua volta riporta direttamente al Ceo”, spiega Arabnia.
Il team, del quale fanno parte anche un esperto di verniciatura e una figura junior che si occupa di marketing industriale, è stato affiancato da una società di consulenza specializzata nello sviluppo industriale.
“Per i primi mesi – prosegue Arabnia – compito del team è stato visitare tutte le fiere dedicate all’IoT in giro per il mondo e al di fuori del nostro mercato, per portare a casa idee. Solo dopo questa prima fase, e dopo aver condotto una ricerca di mercato ad hoc, abbiamo creato la struttura portante del nostro progetto Industria 4.0”.
Il digital twin dell’impianto di verniciatura
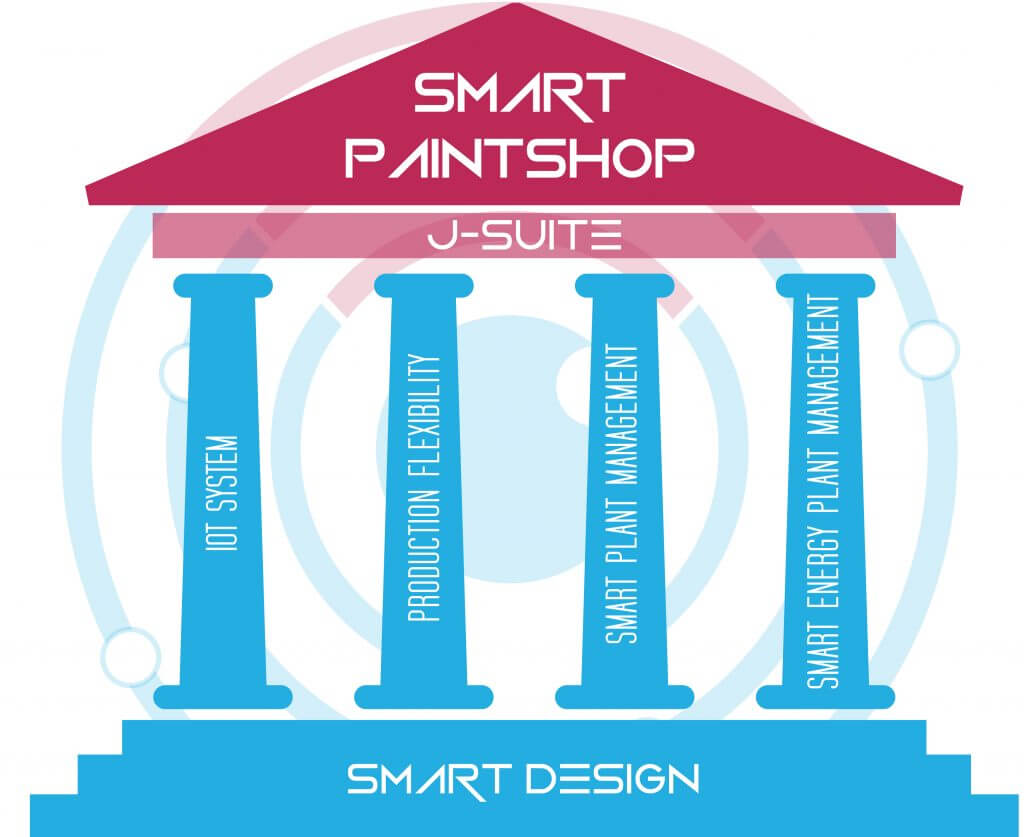
Arabnia la definisce “una struttura a tempio greco”: alla base lo smart design, su cui poggiano quattro colonne che rappresentano le soluzioni IoT, la production flexibility, lo smart plan management e lo smart energy plant management; su tutto questo un ulteriore layer, la J-Suite, che costituisce l’avatar digitale dell’impianto.
“J-suite è l’anima dell’impianto, è il digital twin della parte fisica del’impianto: prima si studia il cervello, poi la parte fisica”, spiega.
I tavoli di lavoro guardano alle aree applicative del progetto
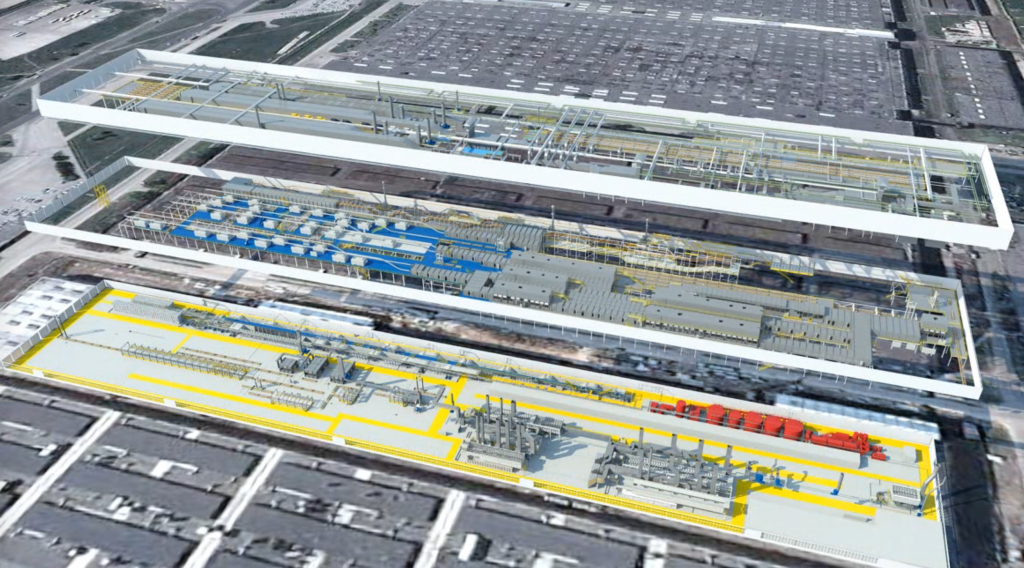
Sulla base di questa struttura, si sviluppano poi i diversi tavoli di lavoro.
Collegato allo smart design è ad esempio il tavolo dedicato allo smart engineering. “Stiamo parlando di un progetto ancora in corso, che parte però da un assunto chiave: noi realizziamo impianti sempre nuovi e diversi, in base al produttore e in base al modello di auto, è davvero impossibile parlare di standard? Oggi noi lavoriamo su disegni 3D e su quelli sviluppiamo l’impianto. La nostra idea è avere una modellazione 3D intelligente, che sulla base di poche informazioni sia in grado di generare una prima idea di layout, accelerando di conseguenza i tempi per la presentazione delle offerte e per lo sviluppo ingegneristico vero e proprio”.
Si parla anche di smart quality control, che va ad aggiungersi ai sistemi tradizionali, basati sull’occhio umano o sull’utilizzo di telecamere.
“Il sistema che abbiamo sviluppato si basa sulla qualità topografica della scocca e ha l’obiettivo di eliminare quelle attività ripetitive che non aggiungono valore. Non possiamo tenere le persone per un’intera giornata a osservare le scocche. Il sistema che abbiamo sviluppato segnala le criticità e l’operatore, con l’aiuto di un visore per la realtà aumentata, valuta il difetto. Abbiamo previsto un terzo passaggio nel quale l’operato dell’operatore viene valutato in logica machine learning: la macchina impara proprio dalle scelte e dalle azioni messe in campo dall’uomo”.
Un terzo ambito di applicazione guarda alla geolocalizzazione interna; serve a sapere dove si trova ogni scocca e per ciascuna sono raccolte tutte le informazioni: per chi è realizzata, a quale temperatura è stata cotta, in quale fase di lavorazione si trova. “La geolocalizzazione è importante anche per la safety degli operai: wifi e radar ci consentono di sapere chi si trova in aree pericolose. Ma questo utilizzo della geolocalizzazione, in logica di tracciabilità, in futuro aprirà le porte alla mass personalization”.