Si parla moltissimo di Industrial Internet of Things, Industry 4.0 e di iniziative per facilitare l’adozione di nuove tecnologie per trasformare le nostre realtà industriali. Considerato che il tessuto industriale italiano è in gran parte formato da piccole e medie imprese, diventa fondamentale comprendere cosa può essere abilitato con investimenti contenuti. Quando infatti non si può fare leva su dipartimenti R&D di grandi gruppi industriali, vanno ricercate e perseguite nuove strade, in modo che anche piccoli investimenti possano sfruttare le nuove tecnologie e la loro capacità di avere basse barriere di ingresso e allo stesso tempo essere in grado di poter scalare operativamente in volumi col crescere dell’adozione dei servizi. È proprio in questo contesto che il connubio tra cloud e manufacturing trova naturale collocazione: il cloud, infatti, abbatte le barriere di ingresso per piccole realtà industriali creando opportunità solo un decennio fa riservate a grandi realtà industriali. Con il termine cloud manufacturing si intende la convergenza delle tecnologie cloud con la Industry 4.0.
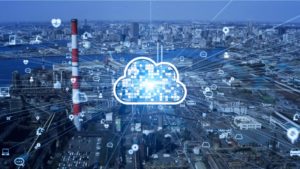
Indice degli argomenti
Cloud computing per la PMI
Il cloud come abilitatore
Per realtà industriali di piccole dimensioni, spesso solo fino a qualche anno fa i costi di setup (server, reti, sicurezza) erano proibitivi anche solo per piccole sperimentazioni e questi investimenti richiedevano volumi tali da giustificare appieno l’uso delle risorse, di fatto bloccando l’innovazione per questi attori. Con l’avvento del cloud è possibile invece avere a disposizione “datacenter” scalabili con conseguente flessibilità dei costi, fatto che per la PMI si traduce nella possibilità di innovare con investimenti minimi per poi “scalare” nella gestione di volumi crescenti nel momento in cui il business case sia stato validato. Diventa quindi decisivo, una volta risolto il tema della connessione della fabbrica al cloud (e quindi lo step IoT come vedremo nei prossimi paragrafi), utilizzare una soluzione cloud per poter accedere ai dati raccolti ed elaborarli. I passi una volta connessa la fabbrica sono:
- esplorazione dei dati raccolti (nota come EDA – Exploratory Data Analysis);
- costruzione di insights: una volta compreso come elaborare i dati è possibile costruire insight sulle componenti più significative, es. unità prodotte, stazioni con più alto grado di criticità, movimentazione asset in fabbrica, etc;
- modelli predittivi: in alcuni casi è opportuno non solo monitorare e agire in modalità reattiva ma procedere in modo proattivo con la determinazione di un modello predittivo al fine di ottimizzare la gestione della fabbrica 4.0.
La dimensione cloud per la Fabbrica 4.0 rappresenta un punto di partenza che abilita la creazione del valore, non di arrivo: come vedremo, le potenzialità di estrazione del valore sono sugli use case che possono essere abilitati dalla elaborazione dei dati raccolti e non sui dati in sé che, se non utilizzati opportunamente, rappresentano una fonte potenziale sprecata, un po’ come una miniera scoperta ma non sfruttata.
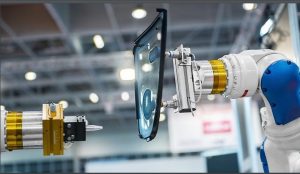
Due realtà diverse: OT vs IT
Chiunque abbia lavorato in ambito manufacturing sa che l’integrazione tra OT (Operational technology) e IT (Information technology) non è assolutamente un dato di fatto, ma va costruita anche da un punto di vista organizzativo per poter esprimere le potenzialità delle tecnologie emergenti in ambito cloud manufacturing. Infatti, come anche discusso ampiamente (Zuffada 2017), il tema è radicato in separazioni organizzative, figlie di un’epoca dove la separazione tra mondo IT e Operations era netta: con un IT a supporto del business/uffici gestito da un responsabile informatico (CIO, responsabile ICT) e con l’OT a supporto della fabbrica controllato da personale inquadrato nel comparto produttivo (tipicamente da un responsabile dei sistemi informatici di produzione). In questo contesto diventa a volte difficile una collaborazione tra i mondi fortemente polarizzati di OT e IT, che va alimentata tramite progetti volti a chiarire il valore del cloud manufacturing per l’azienda.
Anche a livello di modelli di finanziamento esistono differenze spesso sostanziali: per le iniziative Industry 4.0 l’IT è quasi sempre priva di budget strutturale e quindi fa leva su iniziative progettuali, mentre i dipartimenti OT possono fare tipicamente riferimento a risorse per garantire l’evoluzione della operation di fabbrica. Nel momento in cui tecnologie prettamente inserite in contesti IT come il cloud computing, AI, IoT, blockchain vanno a supportare e a integrarsi con il mondo del manufacturing, diventa facile comprendere come la spinta verso la convergenza tra queste due realtà organizzative diventi sempre più concreta per un approccio di successo.
Le reti per OT e IT
Nei paragrafi precedenti si è affrontato il tema di OT e IT: questa distinzione diventa evidente nell’approccio al tema delle reti all’interno della fabbrica. Se per i dipartimenti IT l’attenzione è focalizzata verso la segregazione dei dati, il controllo degli accessi e altri aspetti legati alla riservatezza e integrità delle informazioni, per la componente OT quello che è un punto fondamentale è la disponibilità dei dati, che rappresenta l’operatività della fabbrica e ha impatto diretto sulla produzione. Spesso questo si riflette sulla diversa concezione di rete: non è infatti strano trovare configurazioni di reti di fabbrica “piatte” e a volte prive di contromisure di sicurezza necessarie, ma allo stesso tempo performanti per lo scopo preposto per l’OT.
Spesso, inoltre, lo scopo dell’OT è quello di utilizzare direttamente i dati di produzione raccolti, sul campo mediante visualizzazione e cruscotti in tempo reale, mentre con le componenti IT il passo è quello di portare i dati in cloud e analizzarli insieme ad altre sorgenti dati per poter avere un approccio anche strategico oltre che operativo.
Questa dinamica OT vs IT se non opportunamente gestita a livello organizzativo può produrre situazioni critiche: ad esempio si trovano situazioni in cui OT fa affidamento su fornitori esterni per la componente IoT che “connettono” apparati direttamente ai backend dei fornitori. In questi casi dati sensibili a livello di produzione vengono inviati ad aziende terze e non vengono né opportunamente protetti, né monetizzati. Si pensi ad esempio a robot (che spessissimo hanno connettività M2M tramite embedded SIM) e conseguenti pattern di produzione di uno stabilimento. Se è vero che i fornitori dei robot hanno necessità di accedere a dati per la manutenzione preventiva degli apparati stessi, è anche vero che è necessario preservare il segreto industriale e le informazioni sensibili del committente, come i tassi di produzione e lo specifico utilizzo delle configurazioni della macchina rispetto ai competitor.
Come mostrato in figura è possibile ottenere un buon livello di integrazione tra reti presenti su sistemi OT e IT mediante componenti border router altrimenti detti IIoT gateway che, pur mantenendo una separazione tra le componenti permettendo il mantenimento dei processi as-is, consente il corretto scambio di dati tra i sistemi OT e IT.
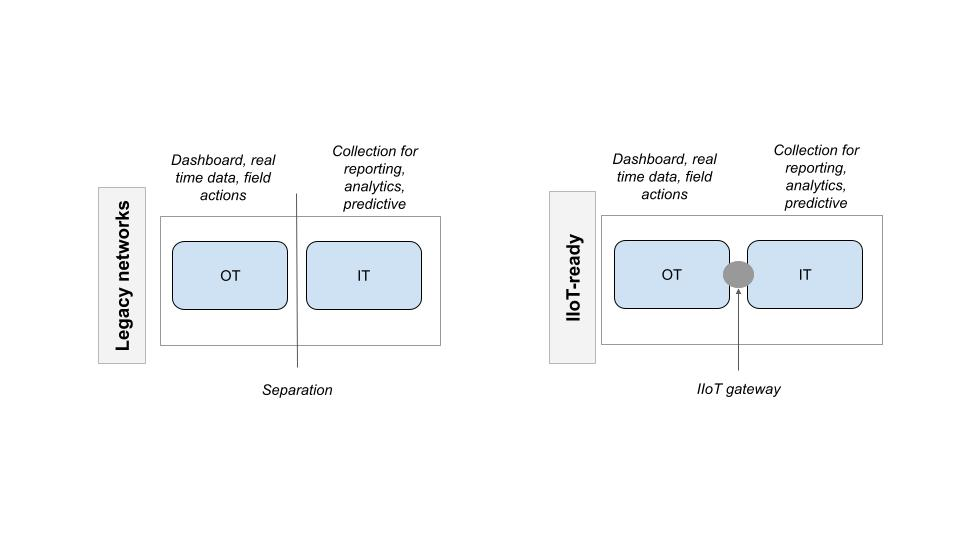
I “mattoni” tecnologici
Connettere la fabbrica al cloud: architetture
Un elemento essenziale per poter abilitare il cloud manufacturing è la capacità di connettere la fabbrica al cloud. Questo diventa possibile attraverso un elemento definito IIoT Gateway, talvolta border router o edge gateway, dispositivo in grado di prelevare le informazioni dalla rete della fabbrica (la OT come visto in precedenza) e comunicare con il cloud di riferimento (tipicamente con protocollo MQTT). In molti contesti applicativi diventa necessario integrarsi con soluzioni esistenti in OT, diventa pertanto molto importante avere un elemento di adattamento per potersi integrare facilmente a sistemi esistenti e quindi operare un retrofit.
Esempi di questi sistemi sono descritti nel prossimo paragrafo e possono essere soluzioni di adattamento a protocolli industriali, come (COPADATA 2021) e (SOTEC 2019) o in caso di presenza di sistemi come Kepware con integrazione su OPC Server come in esempio di (Google Cloud Platform 2020).
Esempio di questa architettura IIoT e i suoi componenti sono rappresentati in figura seguente, dove si può notare come, a seguito dell’adattamento e della trasmissione in cloud dei dati raccolti dalla fabbrica, sia possibile ricostruire un gemello digitale o Digital Twin della fabbrica stessa. Diventa quindi possibile procedere con i seguenti passi:
- analisi dello stato degli apparati;
- costruzione e conseguente applicazione di modelli predittivi.
Mentre le componenti di response realtime sono tipicamente lasciate ai sistemi OT (real time dashboard, allarmi di linea etc), la componente cloud può integrare le informazioni raccolte con altri dati industriali rilevanti (stato approvvigionamenti, vendita, ordini) e di conseguenza fornire una visione a 360 gradi degli impatti e del valore diretto di interventi di ottimizzazione.
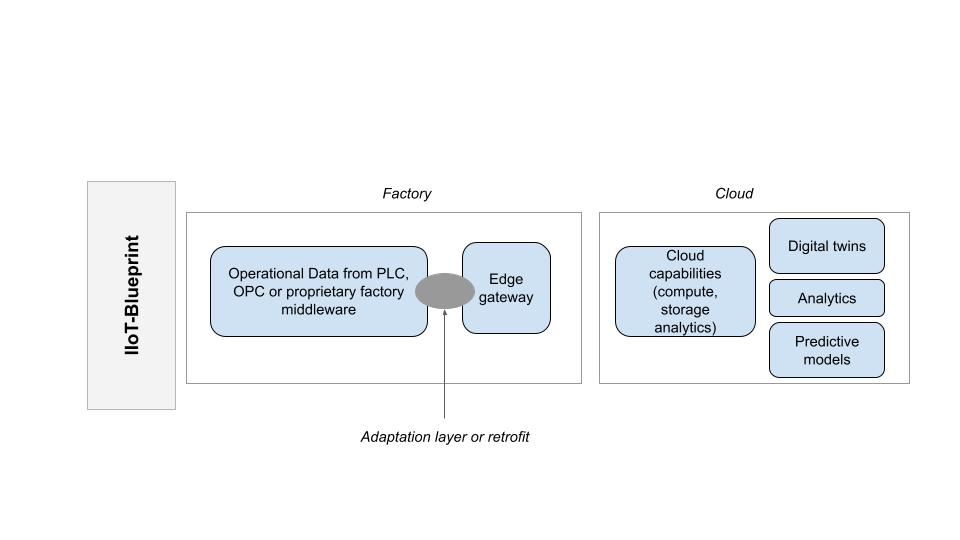
Una “radiografia” della fabbrica: PLC connessi
Elemento fondamentale per la Fabbrica 4.0 è il fatto di poter avere lo stato degli apparati della fabbrica rappresentato digitalmente (spesso definito Digital Twin): elemento imprescindibile per abilitare questo scenario è spesso quello di avere lo stato dei PLC trasmesso in cloud. Ci sono soluzioni disponibili sul mercato per retrofit di apparati esistenti, una di queste è quella CloudPlug (SOTEC 2019) o Copadata (COPADATA 2021). Tipicamente il tema in una prima fase di sperimentazione è quello di introdurre la capacità di esportare dati in cloud senza interferire con il funzionamento già definito della OT (caso cosiddetto “brown-field”, differente da un caso “green-field” dove è possibile l’adozione di soluzioni nativamente integrate col cloud).
Componenti come IIoT gateway sono in grado di interfacciarsi con la rete OT e la pletora di protocolli e sistemi supportati (OPC UA, ModeBus, FiledBus, Kepware). In alcuni casi come quello illustrato in (Google Cloud Platform 2020) è possibile connettere sistemi come Kepware (eventualmente già presenti in OT) in cloud. Una volta connessi i PLC, ad esempio mediante un IIoT gateway, in base ai tag raccolti dal dispositivo i dati sono inviati al cloud e consentono la ricostruzione dello stato della linea produttiva.
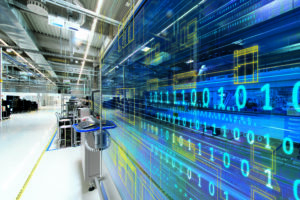
AI e modelli
Come discusso al paragrafo precedente, una volta connessa la fabbrica, diventa possibile lavorare sui dati al fine di definire modelli in grado di portare valore diretto e indiretto sulla produzione. Esempi tipici di questi scenari sono:
- modelli predittivi per rilevazione anomalie e previsione di potenziali guasti: in questi casi vengono riconosciuti “pattern” di anomalia e intercettati potenziali problemi prima del manifestarsi degli stessi in fasi successivi con incremento della difettosità e conseguentemente dei costi;
- analisi per ottimizzazione della produzione: avendo dati in tempo reale e molto capillari è possibile analizzare gli impatti potenziali sul processo produttivo.
Scenari più evoluti utilizzano inoltre oltre ai dati del machinery della fabbrica 4.0 informazioni sulla movimentazione degli asset all’interno della fabbrica stessa, degli operatori sul campo o immagini prelevate al fine di elaborare automaticamente analisi per identificazione preventiva di difetti, come descritto nella sezione dedicata agli use case.
Alcuni use case
Rilevazioni difetti nei cerchi in lega con AI
Un caso che si trova declinato in modo leggermente diverso in diverse realtà industriali è la rilevazione dei difetti mediante elaborazione digitale di immagini catturate ed elaborate tramite modelli di AI. Attraverso la disponibilità di fotocamere ad alta definizione a basso costo e mediante tecnologie cloud diventa infatti possibile allestire stazioni che operano una fotografia su componenti ed elaborare queste informazioni per allestire in modo molto rapido sistemi AI di rilevazione delle anomalie. Mediante sistemi come la Visual Inspection AI (Google Cloud 2021) è infatti possibile operare rapidamente un training delle immagini raccolte. Si pensi ad esempio a un caso di rilevazione di graffi su cerchi in lega di vetture in fase di assemblaggio. Rilevare questo problema tardivamente, a seguito del completo assemblaggio o addirittura dopo la spedizione al cliente finale ha un impatto molto significativo sui costi.
Equipaggiando invece una stazione di una fotocamera azionata opportunamente (es. da PLC a seguito di stazionamento in area) è possibile acquisire le immagini e, con un sistema su cui è stato operato training, è possibile rilevare il problema in tempo reale.
Per incrementare la velocità delle elaborazioni localmente, se necessario, è possibile utilizzare acceleratori locali (es. TPU o Tensor Processing Unit).
Tracking device-less
Un altro caso tipico è quello del tracking di asset industriali all’interno della fabbrica. A questo problema si è spesso risposto mediante introduzione di RFID (attive o passive) per il tracciamento, con conseguenti costi di infrastruttura ed equipaggiamento, oltre che impatto sui processi di produzione. Una possibilità è quella di utilizzare il tracking operato mediante WiFi o bluetooth del dispositivo. Si pensi ad esempio a realtà di produzione automotive, dove sistemi di bordo per infotainment sono dotati di WiFi e Bluetooth. Azionando nelle fasi di produzione questi dispositivi diventa possibile tracciare dispositivi in aree di fabbrica spesso già completamente coperte da WiFi per altri scopi. Nel caso di utilizzi di apparati access point location-ready es. (Cisco 2014) è possibile, senza investimenti aggiuntivi di tipo infrastrutturale, sfruttare le reti WiFI esistenti e asset già equipaggiati di WiFi o BTLE per il tracciamento, limitando in modo importante i costi necessari.
Blockchain per incident management
Un altro settore emergente è quello della certificazione della produzione mediante uso di blockchain in ambito Industry 4.0. Sempre di più, infatti, diventa necessario certificare i processi seguiti e gli step produttivi, e in questo l’utilizzo di blockchain come libro mastro per certificare automaticamente gli step seguiti assume un valore sia per gli stakeholder della realtà produttiva, che potenzialmente per il cliente finale. Un caso d’uso in questo senso è la certificazione di tutti i gate di qualità superati durante la catena produttiva e la conseguente generazione a fine processo produttivo di una lista completa consultabile e certificata di tutti i quality step eseguiti, da associare al prodotto.
Conclusioni
Considerando le caratteristiche principali del cloud (dinamicità, pay-as-you-go, scalabilità, AI as a service) diventa importante per le PMI capire come avvantaggiarsi di queste possibilità senza necessità di investimenti massivi ma sfruttando le economie di scala offerte dal cloud stesso. Sono stati illustrati alcuni casi d’uso dove è possibile anche per le PMI utilizzare tecnologie esistenti (image recognition, tracking device-less, blockchain) per l’abilitazione di servizi a valore aggiunto, senza necessità di investimenti importanti, ma con un approccio volto ad avvicinarsi al mondo del cloud manufacturing “salendo sulle spalle dei giganti”.
Bibliografia
Cisco. 2014. “Location-Aware Cisco UWN Architecture.” Cisco. https://www.cisco.com/c/en/us/td/docs/solutions/Enterprise/Mobility/WiFiLBS-DG/wifich3.html#wp1049111.
COPADATA. 2021. “COPADATA – Industrial software for your digital transformation.” COPADATA -Manufacturing and energy automation solutions made easy. https://www.copadata.com/en/.
Google Cloud. 2021. “GCP – Visual Inspection AI.” Visual Inspection AI. https://cloud.google.com/solutions/visual-inspection-ai.
Google Cloud Platform. 2020. “Connecting KEPServerEX with IoT Core.” Google Cloud Platform – Cloud Architecture Center. https://cloud.google.com/architecture/connecting-kepserverex-with-iot-core.
SOTEC. 2019. “SOTEC CloudPlug edge for digital automation.” SOTEC CloudPlug. https://sotec.eu/en.
Zuffada, Roberto. 2017. “Il dualismo tra IT e OT nell’industria manifatturiera 4.0.” Ricomincio da… 4. .