Il mondo dello smart manufacturing è basato su tecnologie, software e componenti hardware che devono integrarsi tra loro per generare le informazioni che permettono alla fabbrica 4.0 di essere competitiva, efficiente e sostenibile. Come si possono raggiungere questi risultati? La risposta sta nel mix di IoT e Industrial IoT (IIoT).
Indice degli argomenti
Cos’è l’Industrial IoT
L’IoT è in continua espansione e diffusione verso più settori, diventando un pilastro dell’interazione nella gestione della produzione. Dall’IoT nasce la sua evoluzione: l’IIoT, che permette di connettere tra loro le macchine intelligenti e sviluppare quei dati preziosi per l’intero processo aziendale. L’IIoT identifica nuove soluzioni tecnologiche come, ad esempio, piccoli sensori ambientali fino ai cobot – robot collaborativi industriali. Ciò sottolinea l’importanza e la stretta relazione tra IoT, IIoT e tecniche di produzione avanzate verso una rivoluzione industriale che vede protagonista una fabbrica interconnessa, capace di comunicare, analizzare e utilizzare le informazioni per guidare le azioni necessarie.
I vantaggi dell’IIoT
Il beneficio che deriva dall’utilizzo dei sistemi IIoT è rendere disponibile una mole di dati che può rivelarsi cruciale; se associata alle interfacce di controllo e cloud per l’archiviazione, le aziende sono in grado di gestire e storicizzare i dati in modo agile, accelerando il processo decisionale.
Come afferma Douglas Gates di KPMG: “La capacità di spostare rapidamente la direzione del business è un imperativo strategico nell’era dell’Industria 4.0, dove le nuove tecnologie stanno trasformando le industrie”. Questa necessità nasce dall’avere a disposizione dati strutturati, che consentono di prendere decisioni nel minor tempo utile, aprendo la strada all’agilità aziendale.
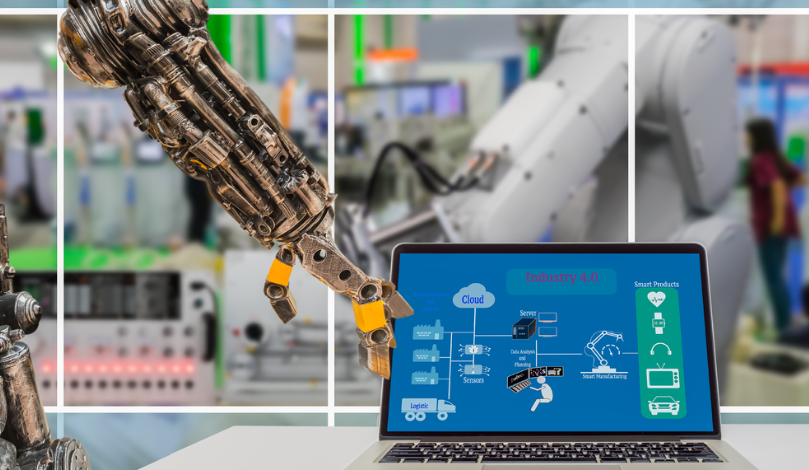
Esempi di applicazione in fabbrica
Le nuove soluzioni tecnologiche, come i sensori combinati ai sistemi di automazione, modificano e danno vita a processi più coerenti con una qualità del prodotto superiore. Le informazioni generate grazie all’IIoT, creano nuove logiche di analisi degli indici di efficienza da applicare alle prestazioni dei processi e con la possibilità di scoprire potenziali problemi.
Se consideriamo l’integrazione delle informazioni di processo con i sistemi ERP (Enterprise Resource Planning) è evidente che è possibile avere una migliore pianificazione e quindi determinare un utilizzo efficiente della capacità produttiva e una maggiore puntualità nelle consegne.
Un’altra applicazione, sempre più strategica nelle imprese di produzione, è legata alle attività di manutenzione preventiva e predittiva grazie all’utilizzo di sensori che permettono l’identificazione e la riparazione di situazioni potenzialmente critiche. Verificando le condizioni di utilizzo delle macchine, prima che causino danni significativi, questi sensori consentono l’intervento immediato che si traduce in una riduzione dei tempi di fermo e una migliore efficienza.
Il ruolo del digital twin nella fabbrica 4.0
Il digital twin è un profilo digitale, in evoluzione, del comportamento storico e attuale di un oggetto o processo fisico che aiuta a ottimizzare le prestazioni aziendali. I digital twin possono modellare macchinari e processi complicati, comprese le loro interazioni con l’ambiente, per prevedere comportamenti e risultati durante l’intero ciclo di vita.
L’interazione tra sistemi digitali di fabbrica e software crea, in tempo reale, connessioni tra il mondo fisico e quello digitale durante i cicli di sviluppo e commercializzazione.
Questo nuovo modello strategico d’impresa mette in condizione i produttori di analizzare e prevedere i problemi, realizzando, tramite processi avanzati, prodotti migliori. I sensori inviano un flusso continuo di dati che analizzato, quasi in tempo reale, permette di valutare le prestazioni del processo e le caratteristiche del prodotto. Un aspetto importante dei digital twin è la capacità di generare un valore tangibile per le aziende, creare nuovi flussi di entrate e aiutarle a rispondere a domande strategiche chiave.
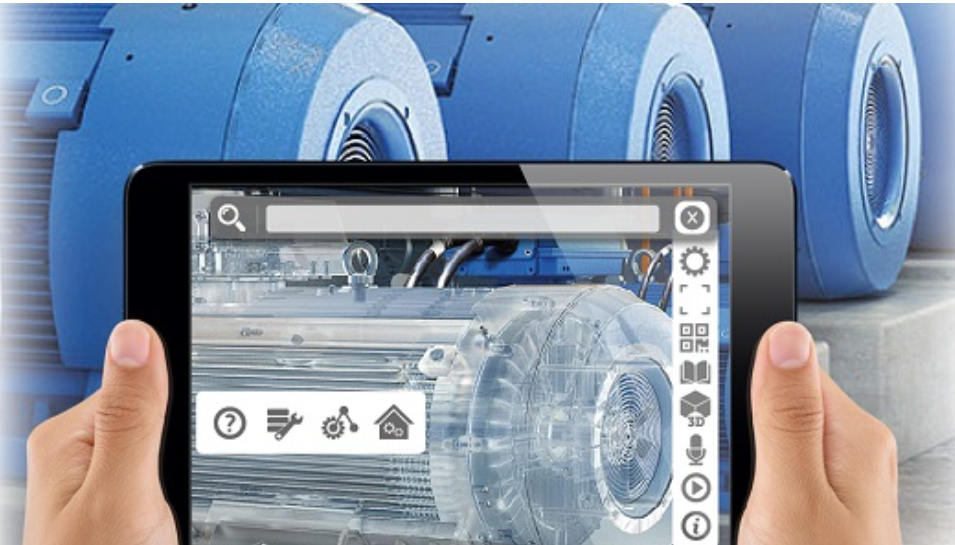
Un nuovo tipo di valore dalle tecnologie connesse
Si può affermare che queste tecnologie connesse, intelligenti e digitali daranno ai produttori l’opportunità di acquisire un nuovo tipo di valore.
Secondo il rapporto curato da Forrester e incentrato sulle previsioni del 2021, entro il 2025, il 55% dei dati in tutto il mondo sarà generato dall’IoT. Lo scenario futuro sarà un microcosmo di dispositivi collegati da tecnologie di comunicazione che consentono di monitorare, raccogliere, scambiare, analizzare e fornire nuove preziose informazioni, offrendo nuovi modelli decisionali e aziendali più intelligenti e rapidi per le aziende manufatturiere.
Interconnettendo sistemi machine-to-machine nascono modelli di strategia aziendale che consentiranno di raggiungere nuovi livelli di efficienza, produttività e prestazioni dando nuovi impulsi tecnologici e di sviluppo alle imprese.
Il futuro dell’IIoT verso il 5G
Sempre secondo il rapporto Forrester – già citato – l’edge computing rivestirà un ruolo chiave che passerà dalla fase sperimentale all’applicazione concreta, sotto la spinta dell’intelligenza artificiale e del 5G.
Il 5G aprirà nuovi e importanti scenari nell’applicazioni di sensori IoT e IIoT. Infatti, va considerato che questi sensori produrranno immensi volumi di dati tra cui video, immagini, clip audio e così via. L’intelligenza artificiale e la realtà aumentata saranno due fattori trainanti per gestire questi flussi che dovranno essere analizzati molto più rapidamente.
Questi cambiamenti creeranno o consolideranno i leader di mercato. In conclusione, l’IoT e l’IIoT sono ormai una realtà nelle imprese evolute. Rappresentano tecnologie innovative che aprono nuovi scenari strategici d’impresa, consentendo di estrarre i dati dal proprio sito produttivo e sfruttarli aumentando l’agilità del processo decisionale e la sicurezza di prodotti, persone e ambiente.