Un digital twin, un gemello digitale che esplora mondi possibili e li comunica al suo analogo fisico perché possa migliorare i suoi comportamenti, fare meno fatica, risparmiare tempo ed energia, capire “cosa succederebbe se”. Un gemello per ogni persona, ogni industria, ogni città, strettamente connesso alla sua controparte fisica: dall’atomo al bit, e ritorno. Può sembrare fantascienza, ma a gennaio Samsung ha dichiarato di lavorare al progetto “Neon”, che crea avatar 3D realistici di un essere umano, cioè figure digitali personalizzate che compaiono su uno schermo e non sono progettate per essere assistenti digitali ma veri e propri alter ego dell’utente. A gennaio 2019, allo Spring Gala Festival in onda su China Central Television, quattro ospiti sono stati raggiunti dal loro gemello digitale creato da ObEN. E i dati fisici, sanitari, di preferenze che rilasciamo sulle diverse piattaforme, non sono tracce di un potenziale gemello digitale individuale? Concetto straordinariamente affascinante, il “digital twin” nasce in ambito accademico-industriale ed è proprio nell’industria che ad oggi trova le maggiori applicazioni: di impianto e/o di processo, gemelli digitali crescono.
Indice degli argomenti
Cos’è un digital twin: significato di gemello digitale
Un digital twin, o gemello digitale, è una copia perfetta digitale delle informazioni che descrivono un’entità reale, sia un prodotto, un processo o un sistema. Il concetto è nato da una presentazione del 2002 di Michael Grieves, oggi chief scientist for Advanced Manufacturing al Florida Institute of Technology, in occasione della costituzione di un centro di gestione del ciclo di vita del prodotto (Product Lifecycle Management – PLM). Dato che ogni informazione nello spazio reale può essere contenuta e rispecchiarsi in quello virtuale, una volta trovata la “porta” di comunicazione e di collegamento delle informazioni tra i due spazi, ogni prodotto (o processo) sarebbe stato formato da due sistemi interagenti tra loro, quello fisico e quello digitale. Due sistemi intrecciati per tutto il ciclo di vita del prodotto, in cui quello virtuale avrebbe aiutato il fisico a esplorare i “virtual subspaces”, ovvero le diverse possibilità di scenario, in tutte le fasi di creazione, produzione, funzionamento e smaltimento.
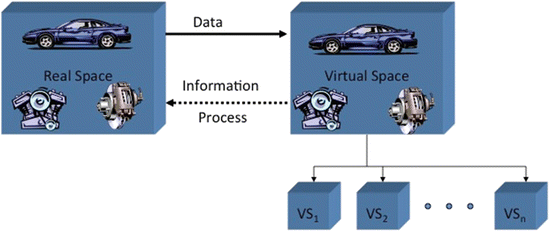
Un rispecchiamento dinamico di informazioni (Information Mirror Model) che è anche gemellaggio tra sistemi: dal 2009 si parla quindi di Digital twin model. Grieves distingue tra Digital twin Prototype (DTP) e Digital twin Instance (DTI), ovvero gli oggetti completi: entrambi operanti nel Digital twin Environment (DTE) che oggi è, sempre più spesso, il cloud.
Un’altra classificazione comune è tra digital twin di prodotto (progettazione efficiente), digital twin di produzione (pianificazione della fabbricazione) e Digital twin di performance (ottimizzazione dei dati). Il concetto è comunque lo stesso: il gemello digitale viene usato sia per prevedere/prevenire il comportamento futuro e le prestazioni del prodotto/processo fisico a un cambio di variabili, sia per monitorarne in tempo reale lo stato e intervenire tempestivamente in caso di guasti o ottimizzarne le prestazioni. In fase di progettazione, viene usato per dedurre la migliore configurazione di componenti per design e funzionalità in base ai requisiti necessari. Test, test continui senza “agire” sul prodotto/processo reale, con la possibilità di seguirne “a distanza” tutto il ciclo di vita e risparmiare tempo, energia, risorse. Un esempio? Pensiamo ai costi, nell’industria aerospaziale, di un test finito male, con l’esplosione di un razzo sulla rampa di lancio. Con il digital twin, la simulazione ha degli effetti reali, ma è tutta virtuale.
Come funziona il modello di gemello digitale
Il gemello digitale è generalmente una suite PLM in cloud, composta da diversi software che seguono le diverse fasi di vita del prodotto/processo. La “porta” che collega spazio fisico e spazio virtuale è l’Internet of Things: i sensori e i trasduttori (v.articolo) posizionati nel prodotto e/o nell’impianto e/o nella linea di produzione che inviano flussi di dati in tempo reale, rielaborati e archiviati grazie al machine learning. Ma come il digital twin incide su un oggetto o su una linea di produzione?
Nell’ambito dell’ingegneria di sistema, per la fase di progettazione 3D, si utilizzano librerie che generano scenari in un unico modello e parametrizzano i componenti dai fogli dati, così da simulare la configurazione personalizzata richiesta e accelerare il processo di sviluppo.
In settori come l’automotive e le gare automobilistiche quest’accelerazione è decisiva: le scocche della Dallara vengono progettate e testate con i digital twin, così come l’ala critica anteriore della Aston Martin Red Bull. Grazie alla simulazione multifisica con il digital twin del modello di batteria, due anni fa la Volkswagen Motorsport ha raggiunto il record di velocità per un’auto elettrica da corsa.
Un altro esempio: in una industria, a una maggiore produttività spesso corrispondono maggiori vibrazioni e quindi maggiore rumore. Se il digital twin è in grado di fare un’analisi acustica, attraverso le camere acustiche e gli hotspot posizionati sugli utensili, localizzerà le fonti di rumore, le monitorerà in tempo reale e genererà delle videomappe dalle aree di colore diverso per controllare se il sistema si comporta in modo corretto e, in caso contrario, suggerire verifiche strutturali.
Un’altra azione possibile è l’analisi modale: se nell’impianto e/o nella linea di produzione sono presenti utensili da taglio, che subiscono vibrazioni e sollecitazioni meccaniche, attraverso l’analisi automatizzata dei dati dei test si recuperano le frequenze e le modalità di vibrazione “naturali” per capire l’affidabilità dell’utensile stesso e si combinano con l’analisi 3D per vedere quali parti subiscono sollecitazioni effettive e verificare che il design sia compatibile con le condizioni operative richieste.
Un altro problema comune agli impianti industriali è l’interferenza elettromagnetica dovuta alla compresenza, nella linea di produzione, di macchine elettriche che integrano dispositivi IoT e cavi di alta tensione: un’analisi elettromagnetica consente di controllare la distribuzione del campo magnetico all’interno del singolo attuatore, ma anche le prestazioni dinamiche rispetto a diverse configurazioni e, qualora non fossero ottimali, di rimodellare le caratteristiche dell’attuatore grazie alle librerie di materiali del software.
Un’altra necessità che spesso si presenta è quella di garantire il corretto raffreddamento delle componenti di un impianto, che spesso, per motivi di sicurezza, è chiuso, con bassa portata di riciclo dell’aria: in questo caso, occorre garantire già in fase di progettazione che ogni componente non surriscaldi durante lo stato operativo, attraverso un’analisi termica che controlli anche la temperatura dell’aria quando l’impianto è in funzione. Senza digital twin, occorrerebbe costruire tanti prototipi per ogni variabile, mentre con il gemello digitale si testano i diversi parametri fino a trovare la giusta configurazione.
In fase di manutenzione, l’operatore può interagire con il digital twin, comunicare la diagnostica e valutare in tempo reale il comportamento della macchina/impianto/linea di produzione, visualizzando anche i documenti e lo storico dei dati relativi a ciò che sta controllando.
La forza del digital twin è poter garantire tutti questi processi insieme, all’occorrenza, e monitorare l’intero ciclo di vita del prodotto o dell’impianto, perché ogni dato ricevuto diventa un “engineering item”, un “oggetto” esplorabile, confrontabile, tracciabile e utilizzabile per prendere decisioni.
Vantaggi del digital twin per migliorare prodotto e offerta
Dal concept al post-vendita, passando per l’ideazione, l’engineering, il processo, la produzione, la logistica: con il digital twin un prodotto/processo può essere validato interamente nello spazio digitale, con una riduzione significativa dei costi e dei tempi di consegna, nonché un aumento della qualità dei prodotti/processi stessi.
Tra i maggiori punti di forza del digital twin troviamo proprio il Virtual Commissioning, la “messa a servizio virtuale”, cioè la simulazione del funzionamento di un macchinario o impianto che testa tutti gli elementi progettati e lo sviluppo software prima della messa in produzione reale. La simulazione può essere: “software-in-the-loop” o “hardware-in-the-loop”. In entrambi i casi, il digital twin comunica con un altro software di controllo, il PLC (Controllore a Programmazione Logica) che è l’elemento base del sistema di controllo di macchine e processi industriali. Tra i vantaggi del Virtual Commissioning: l’individuazione di eventuali colli di bottiglia nel processo, la riduzione dei costi, l’analisi sull’efficienza e sulla sicurezza dell’impianto, il supporto sia lato vendita (poter mostrare come l’impianto funziona davvero) che lato cliente (in caso di assistenza, grazie all’archivio dati c’è una maggiore facilità di verifiche).
La General Electric da qualche anno associa a ogni turbina venduta un digital twin, che riceve da quella fisica i dati di consumo e permette all’azienda di fornire monitoraggio e assistenza, nonché di continuare a testare il prodotto anche post-vendita e proporre eventuali aggiornamenti a pagamento. Anche le automobili Tesla inviano in tempo reale alla centrale operativa dati che consentono di verificarne funzionalità e utilizzo. Un produttore di compressori, la Kaeser, ha usato i digital twin per passare dalla vendita del prodotto alla vendita di un servizio: monitora le proprie apparecchiature h24 così come i livelli di consumo d’aria su cui applica le tariffe, tagliando i costi delle materie prime del 30%.
Alcuni esempi di digital twin
I digital twin possono essere potenzialmente applicati a qualsiasi prodotto/impianto industriale. Come già visto, possono essere utilizzati per perfezionare le prestazioni delle automobili di Formula 1 o per ampliare la gamma di servizi di (post)vendita.
È ancora il caso del produttore di trattori brasiliano Stara, che grazie ai sensori Iot installati sulle attrezzature e al monitoraggio delle prestazioni, fornisce agli agricoltori in tempo reale una visione delle migliori condizioni per piantare le colture e migliorare la resa, con un’ottimizzazione nell’utilizzo di sementi e fertilizzanti.
Il Gruppo abruzzese Fameccanica, player mondiale dell’industria delle macchine per la produzione di pannolini e assorbenti igienici, utilizza il digital twin come “virtual room” non solo di monitoraggio prestazioni ma anche di formazione ai manutentori. Manutentori che al momento di operare avranno un supporto tascabile dotato di app e fotocamera che, a distanza, inquadrando la parte della macchina da controllare, li farà interagire con il digital twin che fornirà tutorial, storico dati e istruzioni specifiche.
Anche ENI utilizza il digital twin in chiave formativa: gli addetti indossano occhiali speciali e un guanto sensorizzato per muoversi in realtà aumentata all’interno del gemello digitale di un impianto esistente e poter simulare interventi in supervisione e sicurezza.
Sempre nel settore energia, il gruppo EDF, principale player in Francia presente anche in Italia, ha annunciato lo scorso marzo di voler utilizzare digital twin dei turboalternatori delle centrali nucleari, per ottimizzare le prestazioni degli impianti, consentirne la manutenzione predittiva e ridurre le spese di riparazione.
Su larga scala, l’esempio più famoso di digital twin è Singapore: Virtual Singapore offre la modellazione semantica 3D della città, a cui associare dati come le caratteristiche del trasporto pubblico, del consumo elettrico, dei componenti degli edifici e delle infrastrutture, nonché informazioni su demografia, clima e traffico, utili sia in fase di pianificazione e sviluppo sostenibile urbano che di simulazione di emergenza e strutturazione di protocolli di evacuazione.
In architettura e ingegneria civile, il digital twin può essere visto come un’evoluzione del BIM, il Building Information Modeling basato su modelli 3D che forniscono informazioni per progettare, costruire e gestire edifici nel modo più efficiente. Ma il digital twin, a differenza del BIM, grazie all’IoT consente non solo la progettazione ma anche il monitoraggio in tempo reale della soluzione individuata. In Giappone, Kajima Corporation, una delle cinque società “super general contractor”, ha iniziato a usare i digital twin per la manutenzione delle infrastrutture e la verifica, anche in fase di progettazione, di eventuali problemi strutturali. In Italia, è stato annunciato che il costruendo viadotto di Polcevera, che sostituirà a Genova il ponte Morandi, avrà un gemello digitale, Cymon.
Un altro famoso esempio di digital twin su larga scala è il porto di Rotterdam, che si è dato l’obiettivo di essere il primo porto digitale entro il 2030: le pareti della banchina, le boe, le gru, le navi sono dotate di sensori che monitorano, tra l’altro, il livello delle maree nonché il movimento, la pressione, la torbidità e la temperatura dell’acqua. Informazioni che, elaborate dal digital twin, consentono di prevedere visibilità, consumo di carburante, arrivo sicuro dei carichi. In Italia sono stati annunciati i progetti di digital twin per i porti di Genova e Ravenna.
Non manca chi, come l’Associazione Liutaria Italiana in collaborazione con la Scuola Politecnica dell’Università di Genova, usa i digital twin dei violini per scoprire i segreti delle migliori performance acustiche, aprendo quindi alla ricerca storica e al restauro le funzionalità del gemello digitale.
Come realizzare un digital twin
Un digital twin è la copia perfetta in digitale delle informazioni che descrivono un’entità reale, sia un prodotto, un processo o un sistema. Per realizzarlo, quindi, prima di pensare alle soluzioni tecniche, un’azienda dovrebbe decidere da dove ricavare i dati relativi all’attività reale e alla produzione, ovvero quali dati di origine includere, oltre ai dati degli eventuali sensori: piani di processo di produzione, procedure operative, dati della catena di fornitura da un sistema MES-Manufacturing Execution System, il software che gestisce la produttività aziendale? Una volta definite le fonti dei dati, uno strumento utile per riunirle potrebbe essere il Business Process Model and Notation (BPMN), che rappresenta graficamente il flusso produttivo aziendale con i diversi processi. I dati vanno infatti organizzati e mappati per poter essere identificati in modo univoco dal futuro gemello digitale, che li assocerà agli obiettivi desiderati. Più si hanno chiari gli obiettivi di utilizzo del digital twin, più sarà facile “modellarlo” sulla base dei dati scelti, e viceversa. Su questi dati infatti andrà inserita l’analitica, che risponde a domande su prestazioni, cause del guasto o simulazioni di processi, che vanno definite in fase di programmazione. In base alla domanda, si innescherà nel gemello digitale l’analisi prima e l’azione conseguente poi. Da stabilire inoltre come le persone interagiranno con il digital twin: quale interfaccia? Dispositivi desktop, mobili, in realtà aumentata? In base alle domande di progettazione, sarà possibile costruire un digital twin adatto alle esigenze di evoluzione aziendale.
Ecco un esempio pratico in un’industria produttrice di taralli.
I software digital twin sul mercato italiano
Tra i software digital twin presenti sul mercato italiano segnaliamo:
3D Experience Platform, Dassault Systèmes
Suite che comprende: i software di progettazione 3D Catia e Solidworks; il software per l’innovazione collaborativa Enovia; il software per le operazioni globali Delmia; il software di simulazione Simulia; il software di simulazione e modellazione delle risorse naturali GeoVia; il software di PLM Analytics, Customer Support & Service Analytics Exalead; il software di pianificazione dello spazio 3D 3DVia; il software R&D per la ricerca chimica e la scienza dei materiali BioVia; il software per dashboard intelligence Netvibes; il software avanzato di visualizzazione 3D in tempo reale 3DExcite; il software per l’innovazione dei prodotti CentricPLM. Disponibile on-premise e in cloud pubblico o privato.
Teamcenter, Siemens
Disponibile anche in versione preconfigurata (Rapid Start), Teamcenter è una suite che ha diverse funzioni: combina tutti i dati MCAD in un singolo ambiente di gestione dei dati di prodotto per gestire anche il ciclo di vita dei materiali; fornisce una fonte di informazioni e di gestione sulle distinte base (BOM) dell’azienda; combina vari livelli dello sviluppo del prodotto (meccanico, elettrico, software) con costi, affidabilità e fattibilità (Systems Driven Product Development); automatizza il workflow interno di modifica e revisione; fornisce strumenti di documentazione avanzati; combina tutti i dati CAD elettrici in un unico ambiente di gestione dei dati di prodotto; fornisce framework di sostenibilità ambientale; crea prototipi virtuali a partire dai formati MCAD ma compatibili con i dispositivi in realtà aumentata; integra la gestione fornitori; gestisce i processi di simulazione; ha avanzati strumenti di ricerca, analytics e report. Disponibile on-premise, in cloud, SaaS.
Ansys Twin Builder
Suite dalle diverse funzioni che unisce le capacità di simulazione dei sistemi multidominio alla prototipazione rapida HMI, all’ottimizzazione dei sistemi e agli strumenti di convalida XIL. Supporta librerie specifiche dell’applicazione 0D, è facilmente integrabile con le piattaforme IIoT, sfrutta le collocazioni dinamiche della memoria per eseguire la manutenzione predittiva sul prodotto. Le funzionalità di Reduced-Order Modeling (ROM) generano modelli accurati ed efficienti a livello di sistema a partire da dettagliate simulazioni fisiche 3D. Twin Builder integra facilmente il software di controllo embedded e la progettazione HMI per supportare i flussi model-in-the-loop e software-in-the-loop per testare le prestazioni dei controlli embedded con i modelli del sistema fisico. Disponibile on-premise e in cloud.
Oracle PLM for Supply Chain Management and Manufacturing
Il software di PLM Oracle Product Lifecycle Management Cloud è integrato all’interno della suite Supply Chain Management and Manufacturing. Il software comprende: l’Innovation Management Cloud per simulare scenari possibili; il Product Development Cloud per migliorare la registrazione dei prodotti e la collaborazione con i fornitori; il Quality Management Cloud per definire, analizzare e ottimizzare la qualità di prodotti e servizi; il Product Data Hub Cloud per gestire le anagrafiche di prodotto e il commercio multicanale, con i dati raccolti e aggiornati in un’unica soluzione; il Configurator Cloud, per personalizzare e configurare prodotti e servizi testando la logica di business, il comportamento del modello e l’esperienza dell’utente prima del rilascio. Disponibile in cloud (Saas).
Gemelli Digitali Azure Microsoft
La suite di Azure Microsoft comprende: un linguaggio di modellazione aperto per costruire modelli di domini personalizzati di qualsiasi ambiente connesso; un ambiente di esecuzione live per dare vita a rappresentazioni grafiche in tempo reale; l’Hub IoT di Azure, che connette gli input provenienti da sistemi IoT e aziendali insieme ad app per la logica e Api Rest; output generato in Time Series Insights, nonché archiviazione e analisi con route di eventi verso servizi downstream come Azure Synapse Analytics. Disponibile in cloud.
IBM Digital twin Exchange
Il servizio IBM prende il nome dalla possibilità di condividere risorse digitali con produttori, OEM, fornitori di terze parti e utenti. Fa parte della suite di asset management Maximo, che consente le “journey to predict”, ovvero delle simulazioni alla scoperta degli scenari possibili: i dati inviati dai sensori IoT dell’oggetto/impianto vengono ospitati nelle architetture cloud dove i diversi software forniscono soluzioni di monitoraggio in tempo reale dei processi, sviluppando modelli predittivi sulle criticità dei singoli asset e collegandoli direttamente a un sistema di ottimizzazione dell’inventario e della supply chain. Maximo Asset Monitor consente un monitoraggio avanzato da remoto su larga scala, alimentato dall’intelligenza artificiale. Disponibile on-premise, Saas e Saas dedicato.