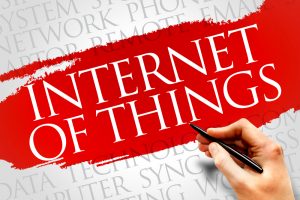
Il fenomeno della digital transformation sta vivendo grazie nella diffusione dell’Internet of Things una straordinaria accelerazione. L’Internet delle Cose contribuisce fattivamente sempre di più a determinare il modo stesso in cui le aziende di produzione progettano, realizzano e supportano i loro prodotti. Un fenomeno questo che si è saldato in quest’ultimo periodo con lo sviluppo di progettualità Industry 4.0 a loro volta frutto della diffusione di soluzioni IoT.
C’è tuttavia un passaggio che, secondo un’analisi pubblicata da EY lungi dall’essere semplice da mettere in pratica potrebbe rappresentare un importante vantaggio competitivo soprattutto per le aziende del manufacturing che sta diventando Smart manufacturing: non limitarsi a portare l’intelligenza a bordo dei prodotti, ma “ascoltare” ciò che i prodotti connessi hanno da dire, trasformando i dati raccolti in azioni concrete.
Dalle connected factory ai connected products
Stiamo entrando nell’epoca della connected factory e dei connected products e occorre prendere atto del fatto che diventa necessario stabilire nuove forme di governance per gestire lo sviluppo. Le aziende del manufacturing devono riuscire a mettere a frutto l’intero potenziale dell’IoT.
E per farlo è importante implementare tre componenti chiave.
Tre strumenti chiave per sbloccare il potenziale dell’IoT
- In primo luogo EY sottolinea l’importanza di porre la massima focalizzazione a livello di infrastrutture e di repository dei dati: per poter trarre gli insight necessari dalla grande quantità di dati provenienti dai prodotti intelligenti e connessi, le aziende di produzione devono poter disporre di un robusto framework hardware e software, ad esempio Hadoop, in grado di processare grandi quantità di dati.
- In secondo luogo soluzioni di analytics avanzate, necessarie per gestire gli insight dai dati al fine di migliorare la qualità e l’affidabilità dei prodotti, riducendo i costi associati alla non conformità.
- Parimenti, ed è questa la terza componente chiave suggerita da EY, occorre porre attenzione alla reliability analysis e alle analisi di affidabilità, che consentono di misurare la possibilità che un dispositivo svolga la propria funzione a certe condizioni per un determinato tempo.
Gli strumenti da soli non bastano, è evidente.Per questo EY indica anche una metodologia di azione, riassumibile in cinque azioni.
I cinque passi verso l’affidabilità secondo EY
- Per prima cosa è importante partire con una lista di domande alle quali dare risposte. Ad esempio è fondamentale sapere quali sistemi hanno le peggiori performance nelle prime 100 ore di servizio o da quale sequenza di eventi si genera un guasto.
- In secondo luogo, le diverse fonti di dati, dalle garanzie ai dati provenienti dagli strumenti di diagnostica, sono importanti per stabilire metriche di affidabilità.
- L’affidabilità, è il terzo punto consigliato da EY e deve diventare una linea guida. Si possono in questo xaso utilizzare strumenti e processi per creare relazioni tra i sistemi, i loro componenti, i software, le parti di ricambio, la diagnostica, così da misurare e identificare ogni possibile errore, evidenziando le possibili criticità prima che si manifestino dando origine a reclami o richieste di interventi in garanzia.
- Non sembri lapalissiano il quarto consiglio: disporre di cosiddetti “actionable insights” non significa automaticamente aver risolto il problema. Mettere in campo azioni correttive là dove necessarie, richiede l’allocazione di risorse e investimenti a qualunque stadio del processo di realizzazione di un prodotto: le azioni correttive potrebbero essere necessarie a livello di progettazione, oppure a livello di strumenti di produzione. Ma devono essere apportate.
- L’ultimo consiglio non tocca direttamente i dati, ma le strategie: non fatelo da soli, suggerisce EY. Il supporto dei partner è indispensabile sia nelle fasi di sviluppo sia in quelle di messa in opera delle policy di analisi sui dati.
Leggi il contributo originale di EY
Immagine fornita da Shutterstock