Indice degli argomenti
Definizione di lean manufacturing
La Lean Manufacturing o Lean Production, è, letteralmente, la “produzione snella”: nata in Giappone, è una metodologia di gestione di impresa che punta ad “alleggerire” i processi eliminando gli sprechi (muda), i sovraccarichi per persone e risorse (muri), le variazioni del flusso produttivo (mura).
Il modello di lean manufacturing tradizionale si basa su due pilastri: il Just in Time (JIT), sistema di gestione del flusso di produzione che ha come obiettivo “produrre solo quando serve”, e il Jidoka, l’ “autonomazione” o “l’automazione dal tocco umano”, che consiste nella ricerca della Qualità Totale e passa dalla cooperazione uomo-macchina per fermare la produzione e correggere il problema al primo segnale di anomalia rispetto agli standard di qualità.
Le fondamenta della lean production sono il Heijunka, il lavoro standardizzato e il Kaizen.
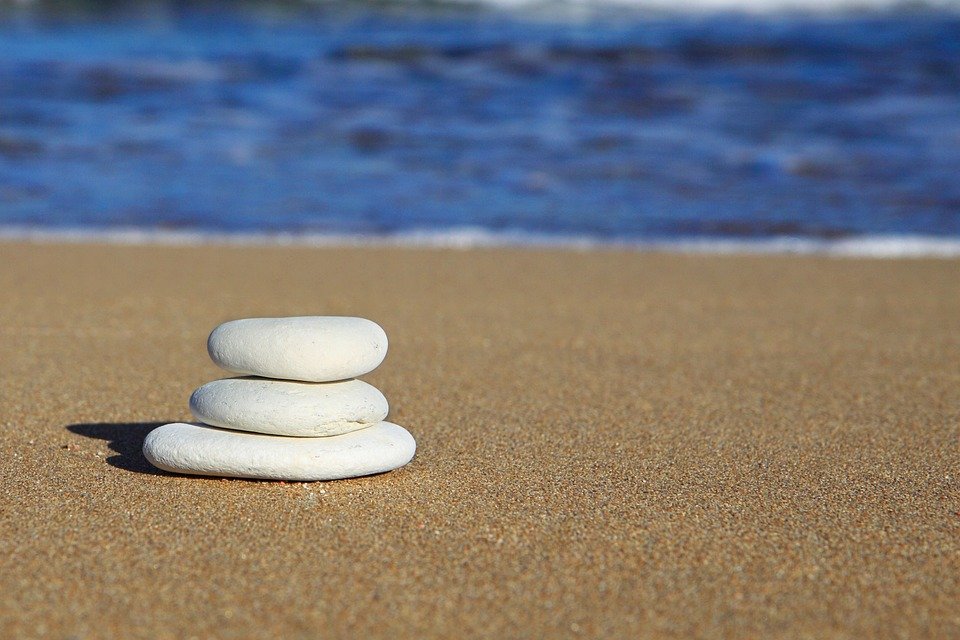
Il Heijunka è il livellamento del volume e del mix di produzione che equilibra il carico di lavoro in ogni cella produttiva. Il lavoro standardizzato è il lavoro organizzato secondo una specifica sequenza di produzione che comprende: il Takt Time, il tempo utilizzato per produrre un pezzo; lo Standard In-Process Stock cioè la quantità minima di componenti da avere per la produzione e la Working Sequence, la sequenza vera e propria delle operazioni univoche svolte per lo stesso processo.
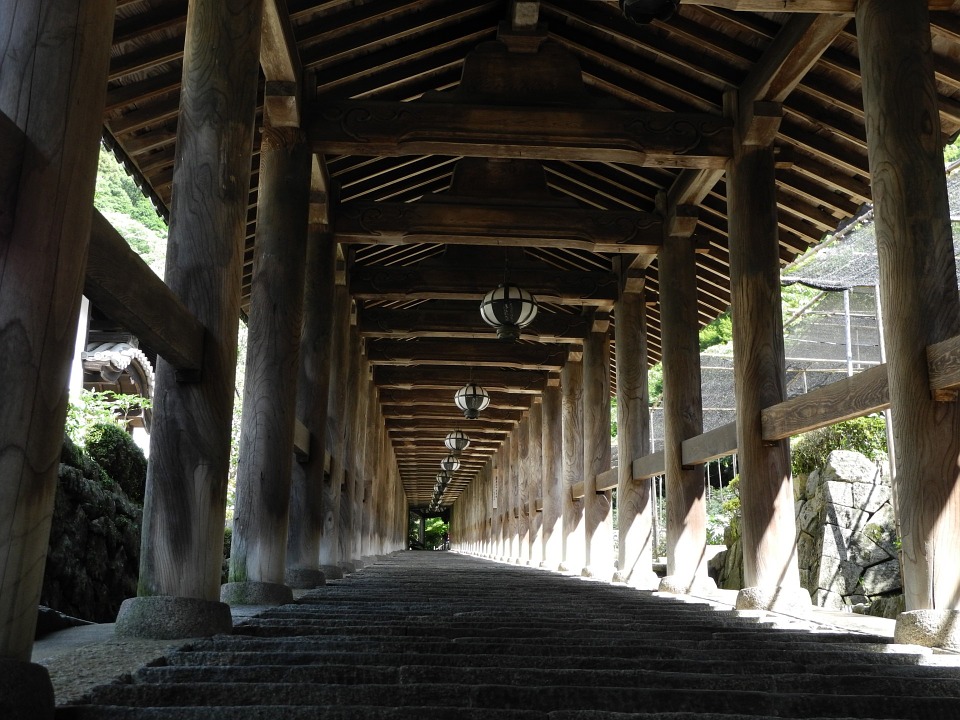
Il Kaizen è la base filosofica della lean production: unione delle parole Kai, “cambiamento” e Zen, “meglio”, è l’approccio del “miglioramento continuo” a piccoli passi.
Video di introduzione alla lean production – Confindustria Club dei 15
Da dove nasce la produzione snella?
Il termine “Lean Production” è stato coniato da un ex ingegnere della Toyota, John Krafcik, in un articolo dell’autunno del 1988, “Il trionfo del sistema della Lean Production” ma deve la sua fortuna al libro uscito nel 1990 a cura degli esperti MIT James P.Womack, Daniel T. Jones e Daniel Roos, “La macchina che ha cambiato il mondo”. Un bestseller che ha analizzato il “Sistema Toyota” all’interno di uno studio sul futuro dell’industria automobilistica e che ha fatto conoscere il “Toyota Production System” associandolo alla “Lean Production”.
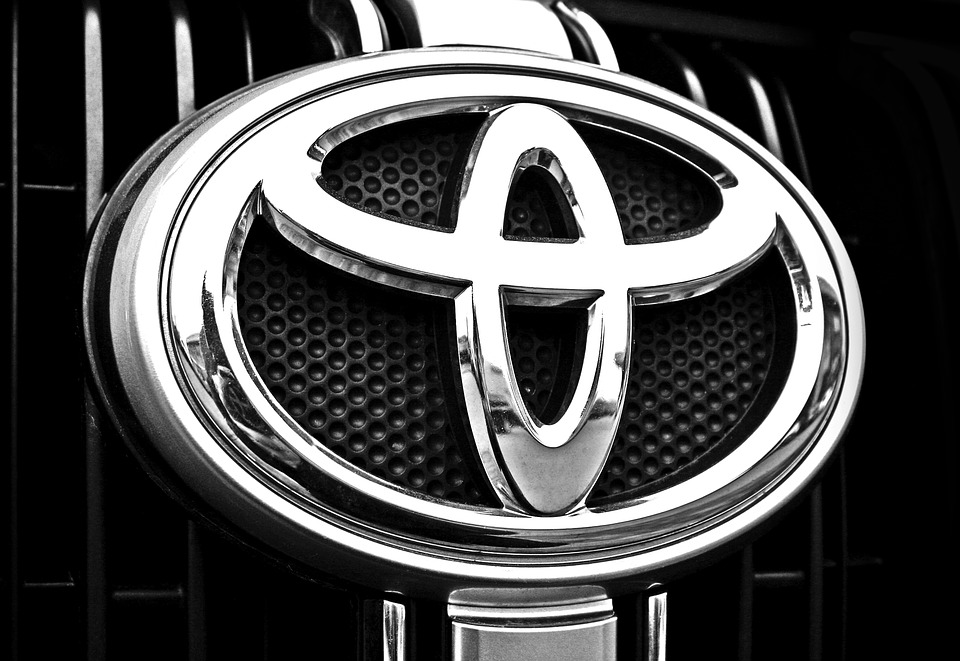
La storia della Lean Production è iniziata infatti nel Giappone degli anni ’50, un paese uscito sconfitto dalla Seconda Guerra Mondiale dopo due bombe atomiche sganciate sul proprio territorio. Un contesto in cui era difficile applicare il metodo di produzione fordista in serie e su larga scala, basato su catena di montaggio e parcellizzazione del lavoro. Un contesto in cui “fare di più con meno” si imponeva come necessità per poter competere sul mercato.
Il sistema Just in Time, produrre solo quando serve
Il fondatore della Toyota, Kiichiro Toyoda, pensò quindi a un sistema differente da quello fordista, il sistema Just in Time, e il suo direttore, Taiichi Ono, lo rese operativo: macchinari più flessibili, piccoli lotti in tempi brevi, un sistema basato non sull’offerta ma sulla domanda, sulla cooperazione uomo-macchina e sul miglioramento continuo del prodotto e dei processi. L’ingegnere Taiichi Ohno, consigliere esecutivo dell’azienda, perfezionò e ampliò quello che, nei decenni, sarebbe diventato il Toyota Production System.
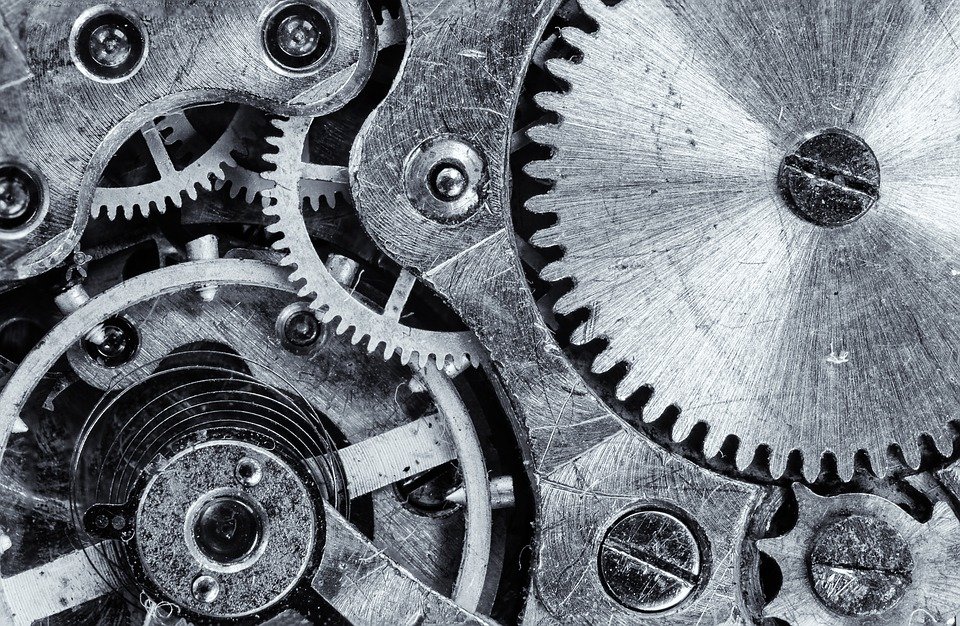
Nello specifico, il sistema Just in Time è un sistema pensato per produrre solo quando serve. È un sistema “pull”, cioè “tirato” dal cliente che richiede il prodotto e organizzato visivamente sui Kanban, i “cartellini” di movimentazione/prelievo o di produzione che contengono una serie di istruzioni. Ogni centro di produzione del sistema è infatti fornito di due punti di stoccaggio: all’ingresso, per i materiali, e in uscita, per il prodotto finito. Lo stoccaggio avviene in contenitori su cui viene applicato uno dei 2 tipi di kanban.
Un kanban di movimentazione autorizza il movimento di un componente da un centro all’altro: è una scheda redatta dal centro di rifornimento e inviata al centro di stoccaggio in entrata. Il kanban numerato è associato ad un contenitore e ne riporta il numero identificativo e la capacità; segna inoltre il codice del componente, i codici dei centri di produzione di partenza (fornitore), di arrivo e dei rispettivi punti di stoccaggio, il numero e il tipo di componenti da ritirare. Una volta ricevuto, il kanban viene staccato e archiviato. Verrà riutilizzato al momento della richiesta di un altro contenitore: il centro di stoccaggio in entrata diventerà quindi il centro di rifornimento in uscita.
Un kanban produzione autorizza invece l’ordine di produrre un contenitore di parti che rimpiazzi quello prelevato: è una scheda usata tra il centro di produzione e il punto di stoccaggio in uscita. Il cartellino contiene il codice della componente da produrre, la capacità del contenitore, il numero del centro fornitore.
Per funzionare, il sistema richiede che i contenitori abbiano sempre lo stesso numero di componenti e vengano parcheggiati sempre nella stessa area. Inoltre, è necessario che ogni kanban contenga sempre la stessa quantità base e che venga associato ad un contenitore. Contenitore che, se pieno, verrà spostato solo se dotato di cartellino.
Il Sistema Just In Time è inoltre One-Piece Flow, cioè organizza l’avanzamento dei materiali uno alla volta, con la possibilità di cambiare modello del prodotto ad ogni passaggio, e si basa sul Takt Time, il tempo in cui deve essere ottenuta una unità di prodotto per soddisfare la domanda del cliente.
Il Jidoka, l’autonomazione
Il Jidoka è l’“autonomazione”, ovvero il processo che mette insieme l’autonomia dell’operaio e l’automazione della macchina. È anche detta “l’automazione con tocco umano”. Consiste nella ricerca della Qualità Totale, e si realizza nell’obbligo di fermare la produzione quando gli standard non sono garantiti e di correggere immediatamente l’anomalia. Si ottiene sia dotando i macchinari di dispositivi di fermo che si attivano automaticamente al variare di parametri stabiliti, sia attraverso il controllo da parte degli operatori, autorizzati, in caso di non conformità, a sospendere la produzione.
Il Jidoka, come il Just in Time, è organizzato sulla cella di produzione, un team di dipendenti che controlla e assembla il prodotto cooperando, diversa dalla catena di montaggio di tipo fordista. Uno strumento o una procedura a prova di errore viene chiamata poka yoke. Se ne distinguono tre tipi: il metodo del contatto, che si basa sulle caratteristiche fisiche dell’’oggetto che permettono di riconoscerne la posizione corretta di assemblaggio; il metodo del valore fisso, basato sul numero di operazioni effettuate; il metodo delle fasi di lavoro, basato sul controllo del loro ordine corretto di esecuzione.
Qual è l’obiettivo del Lean Manufacturing System
L’obiettivo del Lean Manufacturing System è “fare di più con meno”: migliorare la produttività e la sua qualità eliminando tutto ciò che non consente di creare valore attraverso un’accorta organizzazione dei processi.
In particolare, il sistema produttivo viene alleggerito dalle tre “M”: gli sprechi (Muda); i sovraccarichi (Muri) sia del lavoro delle persone che delle risorse; le fluttuazioni (Mura) della domanda.
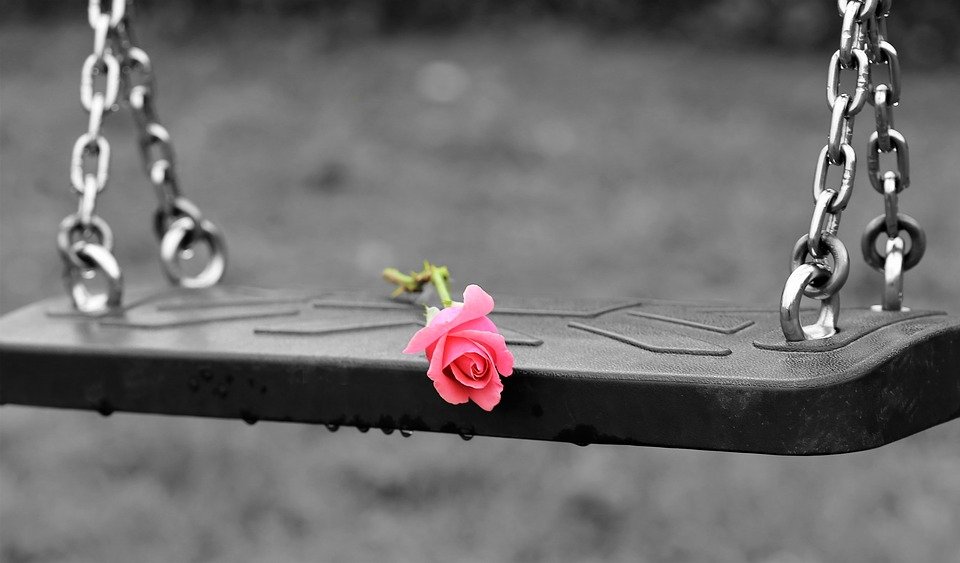
I sovraccarichi sono strettamente legati alla sicurezza aziendale: per le persone, si traducono in un aumento del rischio infortuni per sforzi eccessivi che causano danni, insoddisfazione e assenze dal lavoro; per le macchine, i sovraccarichi portano ad un aumento del rischio usura e costi aggiuntivi di manutenzione ed eventuale sostituzione. Anche ridurre le fluttuazioni della domanda punta a minimizzare gli sbalzi tra momenti di sovraccarico (muri) e sprechi di risorse (muda).
Gli sprechi principali individuati dal Lean Manufacturing System sono 7: primo fra tutti, la sovrapproduzione, cioè una produzione superiore alla domanda, che comporta sprechi di risorse aziendali, scorte, tempo.
Seguono le attese, ovvero i “tempi morti” che riguardano sia le materie prime e i semilavorati fermi in attesa di lavorazione che gli operatori fermi in attesa di materiale o mezzi.
Un altro potenziale di spreco è la logistica inefficiente: non solo perché i trasporti aumentano il rischio di danneggiamento del prodotto e della sua qualità, ma perché spesso la movimentazione dei materiali avviene in spazi eccessivi rispetto alla necessità, con attrezzature non ottimizzate per i trasporti interni, procedure senza precise sequenze e imballi con quantità superiori al fabbisogno reale.
Si arriva alle scorte, considerate come tutto ciò che è in attesa di qualcosa (una lavorazione, una vendita), in un tempo in cui non viene aggiunto al prodotto alcun valore e che aumenta il rischio di peggioramento della qualità. Le scorte, prodotte in eccesso rispetto alla domanda, sono considerate sprechi di spazio e di risorse finanziarie.
Nella revisione degli sprechi non mancano i processi non ottimizzati, cioè non dotati di risorse e procedure commisurate alla domanda di produzione. Si tratta, ad esempio, di processi che utilizzano macchinari con capacità superiori alla richiesta o operatori che eseguono operazioni inferiori alle proprie capacità. Operazioni che possono essere automatizzate.
Un altro muda sono i movimenti improduttivi, che non producono valore: spostamenti inutili per strutture sovradimensionate o procedure non ottimizzate.
Non manca un focus su difetti e rilavorazioni: se gestita all’interno dell’azienda, una non conformità comporta comunque costi finanziari e di immagine, oltre che rallentamenti al flusso produttivo e dilazioni nei tempi di consegna. Se proviene da segnalazioni esterne, una non conformità richiede l’attivazione e il mantenimento di una struttura di gestione reclami.
Le 5S del Lean Manufacturing: cosa sono
Le 5S sono cinque termini giapponesi che rappresentano i punti di partenza per applicare la metodologia lean in azienda.
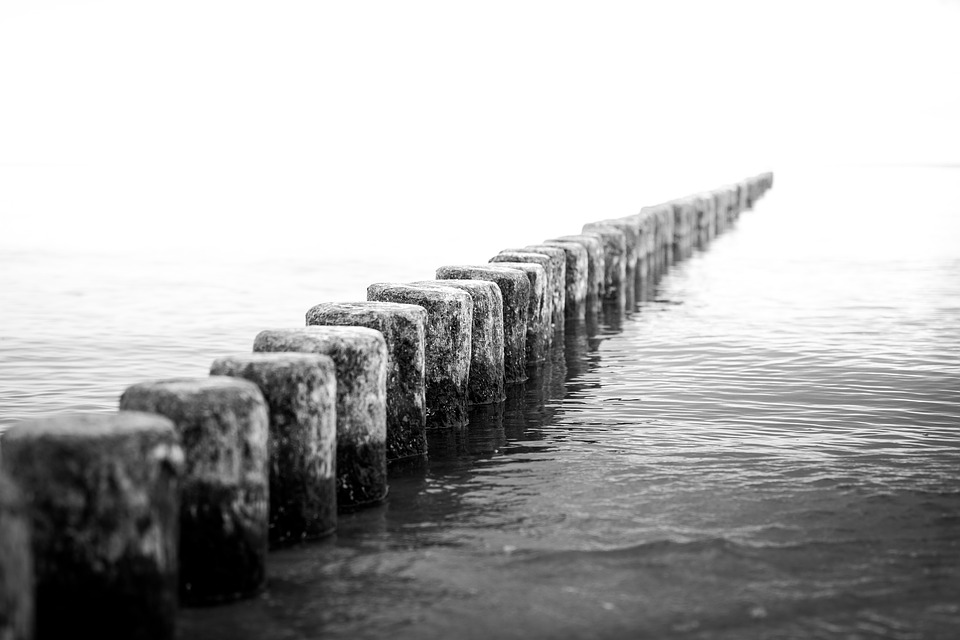
Seiri, o del fare spazio
Seiri significa “scegliere, separare”, un significato simile all’italiano “discernere”, quindi distinguere ciò che è importante ed eliminare il superfluo. Operativamente, si può applicare ad una scrivania, ad un’area produttiva o a tutta l’azienda con il metodo dei “cartellini rossi”.
Dopo una valutazione che include funzionalità e frequenza di utilizzo, la procedura richiede di produrre e fissare dei cartellini rossi sugli oggetti potenzialmente non necessari. Dopo qualche settimana, se l’oggetto rimarrà con il cartellino senza essere utilizzato, verrà eliminato (dalla scrivania, dall’area di sosta).
Video: Come applicare un sistema kanban in fabbrica (inglese) – LeanVlog
Seiton, o del riorganizzare
Una volta rimossa la strumentazione inutile, occorre riorganizzare l’area di lavoro. Seiton significa “sistemare, organizzare” ciò che serve. Studiare quindi una disposizione che faciliti l’identificazione e l’utilizzo di ogni attrezzo. Tutto a vista, raggiungibile, con gli spazi ben delimitati.
Seiso, o del verificare
Seiso significa “ordine, pulizia”: il terzo passaggio riguarda il controllo dell’ordine stabilito. Un’attività che riguarda non solo i responsabili per area della pulizia ma, trasversalmente, tutti i membri dell’azienda, a prescindere dal ruolo. La pulizia come pratica condivisa e ordine mentale, che consolida le abitudini funzionali e permette di consolidarle e ripeterle nel tempo.
Seiketsu, o del migliorare
Seiketsu significa “standardizzare”: definire le attività che servono a mantenere nel tempo l’ordine stabilito. Operativamente, in questa fase si nominano i responsabili operativi dei processi, si integrano i processi individuati nella routine produttiva, si cerca di migliorarli: è il kaizen, il miglioramento continuo a piccoli passi.
Shitsuke, o del mantenere
Shitsuke significa mantenere. Il quinto e ultimo passo prevede il mantenimento del tempo dello stato raggiunto. Una costanza che può essere favorita da specifiche pratiche di formazione, ma soprattutto dai risultati raggiunti in termini di qualità del prodotto e del lavoro.
Quali vantaggi porta la produzione snella nelle aziende?
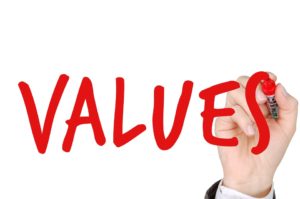
La lean manufacturing, la produzione snella, consente di produrre meglio con meno risorse. Aumenta la creazione di valore riducendo al minimo gli sprechi e ricercando la qualità totale nel prodotto e nel lavoro.
Elimina le sovrapproduzioni, il tempo speso in processi inutili, i ritardi, i sovraccarichi di lavoro attraverso un’organizzazione efficace, efficiente e proporzionata alla domanda reale di produzione.
Le attrezzature e i macchinari così come le attività diventano, appunto, proporzionate ai volumi richiesti, gli spazi adeguati, la supervisione integrata, la formazione continua.
Intervenire sulla gestione della progettazione, della produzione e della qualità con l’approccio “lean” consente di minimizzare i movimenti, gli sforzi, il disordine, l’accumulo di scorte, le distanze, le spese impreviste e di massimizzare l’impiego delle persone, degli spazi, delle attrezzature disponibili nonché la flessibilità, la comunicazione, la cooperazione all’interno dell’azienda.