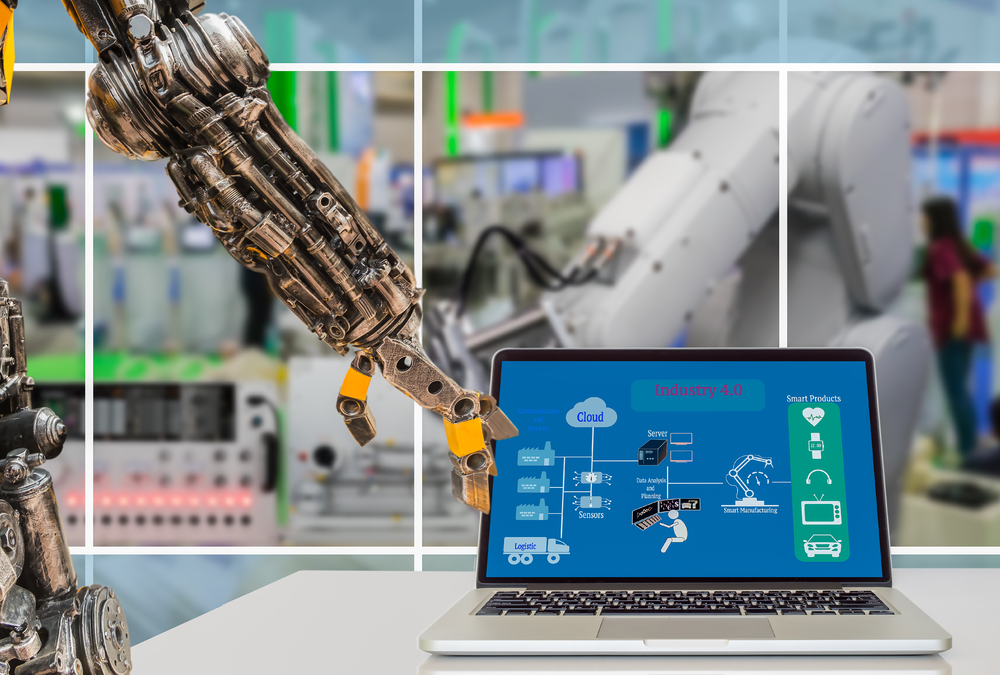
Che la si chiami Industria 4.0, Smart Factory, o che si scelga di parlare di Smart Manufacturing, non v’è dubbio alcuno che il comparto manifatturiero abbia ormai intrapreso un percorso di profonda trasformazione.
Un cambio di passo importante, che nasce sotto la spinta di uno scenario economico sempre più competitivo e abilitato da leve tecnologiche come IoT e Cloud, cui si accompagna una profonda revisione dei processi, della cultura e perfino dei modelli di business aziendali.
Un cambio di passo promosso dai responsabili di produzione, cui sono richiesti sempre maggiori livelli di efficienza operativa: riduzione dei guasti, riduzione dei fermi macchina, riduzione delle difettosità, ottimizzazione nell’approvvigionamento delle materie prime e nella filiera logistica.
Un cambio di passo voluto anche dal top management dell’azienda, che da un lato ha l’esigenza di ottimizzare i propri asset produttivi, dall’altro vuole esplorare nuovi modelli di business, nei quali la componente di servizio e di “recurring revenue” (business ricorrenti) assume un ruolo sempre più determinante.
Indice degli argomenti
Cosa è la smart factory
Senza dubbio, con Smart Factory e smart manufacturing si fa riferimento a un ambiente nel quale è possibile migliorare i processi attraverso l’automazione e l’automatizzazione, con effetti positivi che riescono ad estendersi oltre la realizzazione fisica del bene e impattano sulle funzioni pianificazione, logistica, supply chain, ricerca e sviluppo.
La smart factory rappresenta un vero e proprio salto quantico rispetto al passato: dalla semplice automazione si passa a sistemi connessi e flessibili, in grado imparare dai dati e dall’esperienza e adattarsi a nuove condizioni ed esigenze.
Il percorso che conduce da un approccio tradizionale al manufacturing alla nuova visione della fabbrica abbraccia tutte le fasi e tutti gli aspetti del ciclo di vita del prodotto, dall’idea inziale alla progettazione, dalla produzione alla manutenzione, dall’assistenza fino al fine vita. È dunque un processo che richiede una integrazione orizzontale del flusso di dati e informazioni tra tutti i partecipanti alla filiera e una integrazione verticale con l’intera organizzazione aziendale.
Dal Machine 2 machine al digital twin
Il primo equivoco da chiarire, quando si parla di smart manufacturing, è che non ci si può fermare alla sola automazione.
L’automazione, di per sé, non è nulla di nuovo nel mondo manifatturiero. Definire regole in base alle quali una macchina possa cambiare la propria operatività o il proprio status (accensione, spegnimento, apertura o chiusura) al verificarsi di determinate condizioni (temperatura, velocità, umidità) non è una novità. È dall’inizio degli Anni Duemila che si parla di Machine to Machine , ovvero della capacità delle macchine sensorizzate di comunicare i propri dati ai software che ne regolano il funzionamento.
Quando si parla di smart manufacturing si pensa piuttosto a sistemi complessi, nei quali decisioni complesse, tradizionalmente in capo all’operatore umano, possono essere automatizzate grazie all’applicazione di algoritmi di intelligenza artificiale.
Così la smart factory può essere descritta come un sistema flessibile, in grado di ottimizzare le proprie performance, adattarsi a nuove condizioni anche in tempo reale, gestire in modalità autonoma interi processi di produzione.
Ecco allora che al Machine2Machine si sostituisce il concetto di Digital Twin, letteralmente il gemello digitale, vale a dire la copia virtuale di un prodotto o di un servizio sulla quale è possibile effettuare sperimentazioni e test per riprodurre e verificare il comportamento dei sistemi. Il Digital Twin vive e interagisce solo nel mondo digitale: è in grado di raccogliere e processare grandi quantità di dati e consente dunque di analizzare e testare il funzionamento di un prodotto o di una soluzione, così da capire come migliorarlo o come modificarlo.
Il Digital Twin è un elemento chiave in ogni percorso di trasformazione nel mondo del manufacturing, tanto che, secondo Gartner, già oggi il 48 per cento delle imprese che stanno lavorando a progetti basati sull’Internet of Things stanno utilizzando “gemelli digitali”.
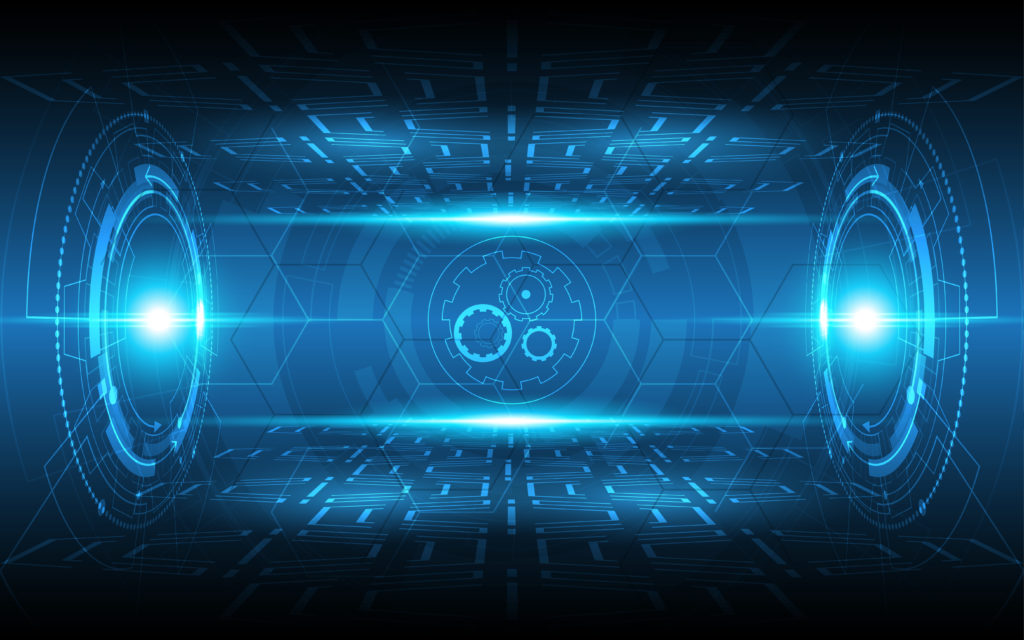
Il valore dei dati
Se implementare un Digital Twin è condizione indispensabile in ogni progetto di smart manufacturing, dal momento che senza il gemello digitale è impossibile identificare i KPI e individuare le aree sulle quali intervenire, è altrettanto vero che la sua implementazione richiede metodo.
Sempre secondo Gartner, è importante che l’intera value chain sia coinvolta perché tutti gli aspetti e tutti i processi vengano presi in esame in maniera olistica e strutturata.
Non solo.
Sempre secondo Gartner è indispensabile che tutte le attività siano correttamente documentate, con protocolli standardizzati, così da poter intervenire e modificarle in tempo reale a seconda delle necessità.
Un Digital Twin richiede anche l’utilizzo di dati e informazioni da fonti diverse, dal momento che difficilmente si può conoscere in anticipo la natura dei modelli di simulazione: per questo motivo Gartner invita i responsabili IT coinvolti nel progetto di a definire che consenta l’accesso e l’utilizzo dei dati provenienti da più fonti.
La extended value chain
Appare chiaro che ogni strategia che porti l’azienda a muoversi in una logica di smart manufacturing non possa limitarsi a una riflessione sul risparmio di costi sul miglioramento della produttività: in gioco ci sono processi di innovazione dei prodotti e dei servizi mai affrontati in precedenza e sicuramente non con l’attuale intensità.
Si tratta di raggiungere nuovi livelli di intelligenza, orchestrazione e ottimizzazione lungo tutta la catena del valore. Per questo l’attenzione dei responsabili del progetto deve concentrarsi su tre asset chiave: l’asset tecnologico, rappresentato ad esempio da tutte le iniziative di Industrial Internet of Things, il ciclo di vita del prodotto, la gestione della catena del valore.
Quest’ultimo è probabilmente l’aspetto sul quale meno spesso si concentra l’attenzione. Eppure, è proprio nell’ottimizzazione dell’intera catena del valore che emerge tutta la potenzialità dei progetti di smart manufacturing.
Affrontare un progetto di smart manufacturing con un occhio attento all’impatto sull’intera value chain significa sganciarsi da un approccio di breve termine e acquisire una visione strategica e di lungo termine grazie a nuovi livelli di collaborazione con partner e fornitori.
Una value chain ben gestita consente di integrare processi, ridurre gli inventari, migliorare i livelli di servizio, con un miglioramento complessivo sia dei prodotti sia dei livelli di soddisfazione dei clienti.
È chiaro che si tratta di un cambiamento culturale importante, che richiede nuovi livelli di trasparenza tra i partner dello stesso ecosistema.
Dal POC al pilota fail fast learn fast
Dati i livelli di complessità fin qui descritti, i progetti di smart manufacturing richiedono di essere affrontati con la corretta metodologia.
Uno degli elementi cruciali della fase progettuale è rappresentato dai POC, i Proof of Concept. Si tratta di una vera e propria piattaforma sulla quale pianificare tutti i dettagli di una implementazione, prima ancora di pensare a un roll out su un processo o addirittura sull’intera organizzazione.
Un POC è di fatto il primo passo verso la risoluzione di uno specifico problema. Per questo motivo il primo passo per la definizione di un POC è aver ben chiari quali sono i cosiddetti “pain” che si desidera indirizzare, quali sono i problemi operativi, gli obiettivi da raggiungere, le metriche di riferimento.
La fase successiva prevede la creazione di un prototipo.
Obiettivo di un POC è avere un impatto economico minimo: si parla di sperimentazione, dunque i risultati potrebbero non essere quelli desiderati e dunque bisogna ricominciare daccapo. In questo scenario, appare evidente l’importanza di poter contare su una piattaforma cloud per la raccolta, l’elaborazione e l’analisi dei dati provenienti dalle macchine e dai sensori.
La terza fase di un POC è quella della validazione dei risultati: i dati, trasformati in informazioni, possono essere utilizzati per identificare aree di inefficienza o problemi.
Se il POC dà dunque esito positivo, si può passare alla sua replica su un numero maggiore di macchine o di linee di produzione.
È questa una fase critica, dal momento che aumentando i livelli di complessità (più macchine, più linee, più dati) i risultati potrebbero non essere quelli desiderati, cosa che imporrebbe una ulteriore revisione del POC.
Solo dopo aver superato anche quest’ultima fase è possibile passare allo step finale con il rollout globale del processo.
Alterna e lo smart manufacturing
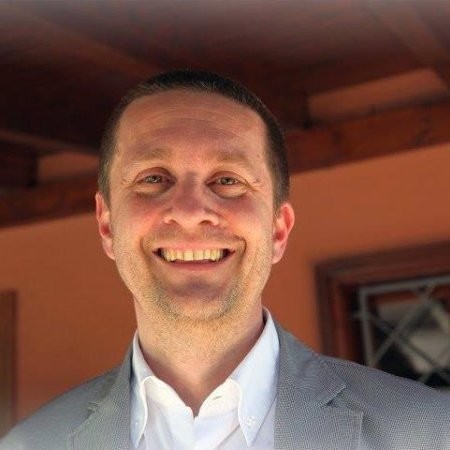
Di queste tematiche si occupa Alterna, system integrator e società di consulenza attiva su tutto il territorio nazionale che vanta oltre 25 anni di esperienza nell’ambito del Discrete Manufacturing.
Partner di riferimento di Microsoft, Alterna, parte di Altea Federation, ha sviluppato una propria practice proprio nell’ambito dello smart manufacturing e della smart factory, nella quale un ruolo chiave è giocato dal cloud e dalla piattaforma Azure Sphere.
“Accompagniamo le aziende che si avvicinano al mondo dello smart manufacturing supportandole in tutte le fasi del loro percorso di trasformazione”, spiega Fabio Paracchini, che segue direttamente questa practice.
“Il nostro ruolo è aiutare le aziende a migliorare e rendere più efficienti i loro processi produttivi valorizzando gli asset che già possiedono. Partiamo dagli assessment, dai POC e arriviamo all’industrializzazione dei processi in una logica fail fast, move fast, accelerando dunque un percorso che per molte realtà oggi rappresenta la vera spinta competitiva. La soluzione di Smart Factory proposta da Alterna è un’opportunità per le aziende di incrementare flessibilità, efficienza e produttività, grazie alla digitalizzazione e alla connettività dei flussi, migliorando al tempo stesso la qualità del lavoro delle persone e dell’ambiente che le circonda”.