L’ultimo Osservatorio MECSPE sul terzo quadrimestre 2021, pubblicato a marzo 2022, fotografa una manifattura italiana che, nel 39% dei casi, si considera sostenibile. La ricerca, condotta su un campione di 980 aziende manifatturiere del nostro paese, si focalizza sulle azioni che le imprese hanno messo in campo per diventare più sostenibili e che comprendono soprattutto l’utilizzo di dispositivi a basso consumo energetico, l’acquisto di macchinari di nuova generazione e l’installazione di impianti di produzione di energia da fonti rinnovabili. Il dato conferma quanto già comunicato dal Centro Studi di Confindustria nel novembre 2021, quando aveva non solo sottolineato la solidità e la ripresa del nostro tessuto manifatturiero, ma anche il suo primato mondiale in termini di ridotte emissioni di CO2. Ciò non toglie che persista tuttora una scarsa conoscenza dei parametri ESG (Environmental, Social and Governance), come si ricava dal fatto che solo un’azienda su 3 fra quelle intervistate dall’Osservatorio MECSPE dichiari di averne sentito parlare. E poiché si tratta di criteri che diventeranno sempre più importanti per valutare l’impatto ambientale di un’attività economica e per indirizzare i capitali degli investitori, è opportuno che entrino a far parte quanto prima della cultura organizzativa delle aziende in generale e di quelle manifatturiere in particolare.
Indice degli argomenti
Cos’è la manifattura sostenibile
La crisi pandemica prima e quella della guerra in Ucraina poi hanno fatto capire che la manifattura sostenibile non è l’ennesima versione del greenwashing applicato al mondo della produzione. Non a caso il Piano nazionale di ripresa e resilienza (PNRR), nato sulla spinta dell’emergenza sanitaria, prevede forti investimenti a sostegno della transizione green dei processi di produzione. Allo stesso tempo, l’eccessiva dipendenza italiana dal gas russo, emersa drammaticamente dallo scoppio del conflitto, ha rimesso al centro dell’agenda politica l’esigenza di accelerare gli iter autorizzativi per la realizzazione di impianti di rinnovabili. Nell’attesa che questo accada, le aziende possono ottimizzare i loro cicli produttivi concentrandosi sull’efficientamento dei processi, dall’acquisto dei materiali e dei semilavorati alla riduzione degli sprechi fino a un uso più oculato dell’energia. Per farlo, occorre che si affidino a quelle tecnologie digitali in grado di offrire piena visibilità a ciò che accade in fabbrica. Da questo punto di vista, non ci può essere transizione green nel manifatturiero che non sia accompagnata da una profonda digital transformation. Per questo si parla di twin revolutions, cioè di rivoluzioni gemelle, con riferimento alla transizione verde e a quella digitale. Un binomio che uno studio di Atos Italia e Ambrosetti dell’anno scorso ha ben evidenziato, calcolando che il digitale potrà influire per più del 50% lungo il percorso di decarbonizzazione di 8 dei settori maggiormente coinvolti nei consumi di emissioni inquinanti del paese, uno dei quali è ovviamente il settore manifatturiero.
Manifattura sostenibile: definizione di metodologie e strumenti
Il passo iniziale di un’azienda manifatturiera che intenda puntare sulla sostenibilità è quello della pianificazione. I dati dell’Osservatorio MECSPE, infatti, nel mostrare la diffusa volontà delle realtà che operano nel comparto a rendere i loro processi più sostenibili, fanno intuire contemporaneamente il rischio di un approccio parcellizzato, come si ricava dalla insufficiente conoscenza degli indicatori ESG da parte di molti intervistati. Esistono oggi delle metodologie, a cui abbinare specifici strumenti, con le quali è possibile analizzare a livello sistemico e di dettaglio l’impatto ambientale di impianti di produzione, sistemi produttivi e singole macchine. Per esempio, il metodo Life Cycle Assesment (LCA), definito dalla norma ISO 14040, consente di quantificare sia gli input (uso di energia, materie prime, acqua e suolo) sia gli output (emissioni, rifiuti, scarti) durante il ciclo di vita di un prodotto-sistema. Gli strumenti abbinati al metodo LCA si basano sulla modellazione dei sistemi di produzione e fondano la loro attendibilità sull’accuratezza dei dati provenienti dallo shop floor. Ne deriva lo stretto legame con la dotazione tecnologica che deve poter attingere tramite sensoristica IoT a informazioni quantitativamente e qualitativamente rilevanti per poi convogliarli nelle piattaforme di analisi. Generalmente il metodo LCA viene abbinato al Life Cycle Costing (LCC), regolamentato dalla normativa ISO 15686, che permette di valutare i costi lungo l’intero ciclo di vita di un prodotto, un impianto, un insieme di componenti o perfino un singolo componente. Gli strumenti combinati LCA-LCC danno così un quadro esaustivo della carbon footprint insieme ai costi a cui un’azienda manifatturiera sostenibile va incontro.
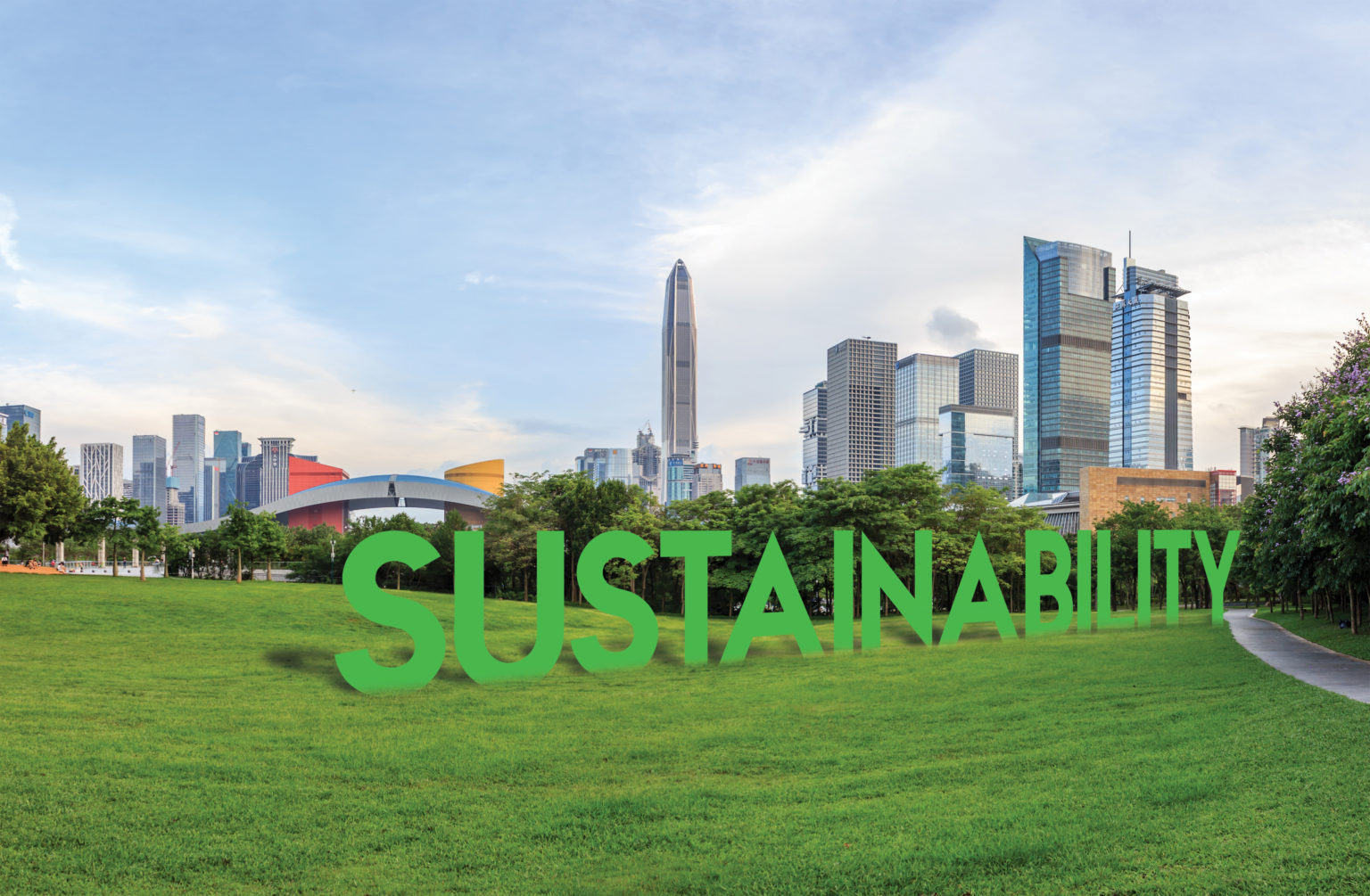
Efficienza energetica
All’interno delle metodologie LCA e LCC una voce fondamentale per una manifattura sostenibile è quella dei consumi energetici. Una manifattura che voglia essere sostenibile non può limitarsi soltanto a installare dei pannelli fotovoltaici, approfittando anche degli incentivi previsti a tale scopo, per innescare meccanismi energetici virtuosi. Tanto più che, come si ricava dai dati statistici pubblicato da Terna, il comparto manifatturiero risulta essere in assoluto quello più energivoro del nostro paese, con il 39% dei consumi elettrici nazionali assorbiti. Da qui l’importanza di mettere in atto una serie di strategie e soluzioni che anzitutto monitorino il reale livello di efficienza energetica di impianti e stabilimenti e, in secondo luogo, aprano la strada all’implementazione di tutte quelle pratiche che riducano gli sprechi energetici. Rientrano fra queste pratiche, che di solito vengono indicate con l’espressione Design per efficienza energetica, lo sviluppo di nuovi materiali e l’analisi dei consumi energetici che incidono direttamente sulla produzione o indirettamente su tutte le attività a contorno (ventilazione, illuminazione, riscaldamento, raffreddamento ecc.). Per una manifattura sostenibile, quindi, la progettazione deve puntare a ottenere il risultato dell’efficienza energetica facendo leva su due aspetti concomitanti. Da un lato, deve selezionare metodi di produzione e layout di fabbrica che garantiscano consumi energetici ottimali, dall’altro deve contemplare una gestione del ciclo di vita dei prodotti e una supply chain in cui l’energia non si disperda. Infine, non vanno sottovalutati i consumi accessori rispetto a quelli generati dagli impianti produttivi che si riferiscono, per esempio, ai sistemi di raffreddamento o agli impianti idraulici e pneumatici. L’efficienza energetica nella manifattura sostenibile, in sostanza, va perseguita con un criterio organico e onnicomprensivo.
Design for disassembly
Ai due pilastri del contenimento dell’impatto ambientale e dell’efficientamento energetico, la manifattura sostenibile può aggiungerne un altro con cui progettare fin dall’inizio l’utilizzo delle componenti a fine vita del prodotto. Questo tipo di progettazione integrata prende il nome di Design for disassembly (DfD) e consiste in una metodologia che prevede il riciclo delle parti smontabili di un oggetto ai fini di un successivo impiego industriale o di uno smaltimento meno oneroso. Pur godendo di maggiore longevità nell’area dell’edilizia e dell’architettura, ormai lo si sta sperimentando con successo nel manifatturiero proprio perché il DfD risponde a quel modello di economia circolare su cui si sofferma anche il PNRR. Il Piano nazionale di ripresa e resilienza, nello specifico, associa il tema dell’economia circolare a obiettivi ben precisi nel riciclo dei rifiuti urbani: 55% entro il 2025, 60% entro il 2030, 65% entro il 2035 e una limitazione del loro smaltimento in discarica non superiore al 10%. In realtà, il Design for disassembly mira a introdurre parametri che semplificano il disassemblaggio in vista non soltanto del conferimento nei rifiuti, ma anche del re-manufacturing e del riuso. I suoi principi, di conseguenza, vertono sull’architettura, le connessioni e i materiali che fanno parte di un prodotto. Una minimizzazione del numero di componenti e di materiali, così come la riduzione degli elementi di fissaggio o il contenimento delle tipologie di materiali impiegati rappresentano altrettante opportunità di ottimizzazione dei tempi e dei costi, oltre a salvaguardare l’ambiente dal depauperamento di materie prime che saranno sempre meno disponibili.
Demanufacturing
Se il DfD introduce un modello di progettazione per il riuso dei materiali o il loro migliore conferimento, il demanufacturing è la disciplina che porta il disassemblaggio nell’ambito dei prodotti elettronici. Ha lo scopo di riuscire a salvare circuiti, processori, schede madri, alimentatori, cavi e unità ancora più elementari quali filo, acciaio, plastica, alluminio, rame ecc. Si tratta di un’operazione di estrema complessità per la quale occorrono sistemi modulari e flessibili che comprendono la possibilità di ispezioni visive, di attività di de-saldatura laser, di riscaldamento a infrarosso per la rimozione di componenti e così via. A ciò si aggiunge l’alternanza di processi manuali con stazioni robotizzate in base alle parti da scomporre. Una tale complessità corrisponde a un aggravio dei costi che finora non ha permesso al demanufacturing di trasformarsi nella nuova frontiera della produzione. Il modello dell’obsolescenza programmata resta saldamente al suo posto, come del resto testimonia la carenza di microchip che sta mettendo in crisi il settore automobilistico, e non solo, dall’avvento della pandemia. Certamente, se il demanufacturing intende candidarsi a scardinare i paradigmi produttivi tradizionali dovrà avvalersi dell’alleanza delle aziende manifatturiere sostenibili con tutti gli stakeholder con cui a vario titolo è in rapporto. Le sperimentazioni svolte anche in Italia parlano di uno stretto legame tra aziende del comparto elettrodomestico con centri di ricerca e istituzioni, a dimostrazione del fatto che l’economia circolare, nel proprio cerchio, deve includere un numero quanto più ampio di attori.