Meccatronica: questo termine, chiaramente una crasi di meccanica e elettronica, apparve per la prima volta in un documento dell’azienda giapponese Yaskawa Electric Company, verso la fine degli anni Sessanta. Elettronica e meccanica insieme, quindi. Ma la definizione migliore, a detta di molti, è quella data da Fukada e Harashima nel 1996: “Meccatronica sono quei sistemi che presentano una integrazione sinergica di ingegneria meccanica, elettronica e sistemi di controllo intelligenti”.
L’importanza di questa definizione sta nell’evidenziare come le tre componenti fondamentali che costituiscono i sistemi meccatronici non siano una subalterna all’altra ma si bilancino già nella progettazione.
Che differenza c’è tra i dispositivi meccatronici e quelli elettro-meccanici? Una differenza significativa: in questi ultimi, infatti, il movimento viene generato da fenomeni fisici di natura elettrica. Nella meccatronica è invece l’elettronica In pratica, nei dispositivi meccatronici le componenti elettroniche sono integrate nei sistemi meccanici fino a divenire parte integrante degli stessi.
Indice degli argomenti
Meccatronica, origini e principali campi di applicazione
Lo sviluppo della meccatronica ha seguito il processo evolutivo delle tecniche di progettazione e di controllo, che passa per microcomputer, computer embedded e microcontrollori.
Sono nati così gli elementi meccatronici, espressione con la quale si intendono gli attuatori (regolatori, convertitori e trasformatori di energia) che comandano il moto; i sensori, che rilevano le variabili di stato di un processo e i dispositivi di controllo (o regolatori), i quali elaborano, secondo determinate regole, le variabili di stato rilevate e inviano agli attuatori istruzioni di comando in modo che questi intervengano correttamente nel processo in corso, in relazione alle necessità.
La meccatronica ha origine nell’ambito della modellistica, della simulazione e della prototipazione dei sistemi di controllo e ai sistemi di Motion Control e dalla necessità per le industrie manifatturiere di essere maggiormente competitive. Produttività, flessibilità e qualità del prodotto sono requisiti sempre più determinanti; il processo di progettazione tradizionale, caratterizzato da una rigida successione di fasi in cui gli aspetti meccanici, elettrici e informatici vengono trattati separatamente e sequenzialmente, non è in grado di soddisfare queste esigenze. L’approccio meccatronico, invece, considera in modo congiunto i differenti processi di progettazione.
I principali campi di applicazione della meccatronica sono la robotica, l’automazione industriale, la biomeccatronica, l’avionica, i sistemi meccanici automatici degli autoveicoli e gli azionamenti elettrici.
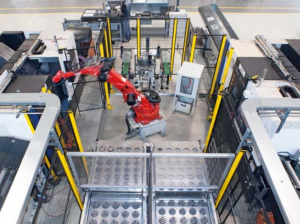
L’innovazione ottenuta sostituendo dispositivi meccanici con dispositivi elettronici caratterizzati da funzionalità analoghe è decisamente un’interpretazione riduttiva della meccatronica. Una visione più ampia si ha quando la progettazione delle parti meccaniche è effettuata in funzione delle prestazioni ottenibili dai dispositivi elettronici opportunamente selezionati.
Nell’interpretazione giapponese del termine, per meccatronica si intende l’applicazione congiunta e coordinata di un insieme di tecnologie tutte coinvolte nella realizzazione di particolari dispositivi meccanici. La movimentazione controllata costituisce uno dei settori innovativi in cui risulta conveniente utilizzare l’approccio meccatronico per elevare la qualità delle prestazioni e migliorare la convenienza economica.
La meccatronica permette di affrontare in modo organico, interdisciplinare, problematiche relative alla progettazione di sistemi complessi e fortemente integrati: robot, macchine utensili, dispositivi servocomandati per autoveicoli, aerei e altro ancora. Il ricorso alla meccatronica consente di:
– realizzare la relativa movimentazione controllata senza sovradimensionare né la struttura meccanica né i componenti
– rendere il sistema economicamente più conveniente,
– ottenere migliori prestazioni funzionali, minori costi di gestione e manutenzione
– rendere nel contempo più semplice per gli utenti il controllo e la diagnostica di processi sempre più complessi
Alla base di questo tipo di applicazioni vi è la possibilità di creare, mediante attuatori regolabili, moti elementari controllabili con precisione con adeguate prestazioni dinamiche.
La meccatronica nel settore automobilistico
Uno dei settori in cui la meccatronica si è maggiormente sviluppata negli ultimi anni è quello dell’automotive. Un esempio fra tutti è costituito dal sistema a iniezione elettronica che ha sostituito il vecchio carburatore. Dalla metà degli anni Settanta si è iniziato a studiare quali componenti di un’autovettura potessero essere migliorati, in termini di prestazioni, sostituendo le componenti meccaniche con componenti meccatroniche. Sono nati così i sistemi per il controllo elettronico della frenata, cosiddetto ABS (Automatic Braking System) e quello per il controllo elettronico della accelerazione TCS (Traction Control system).
L’ABS, ormai di serie anche sulle utilitarie, mette in relazione la velocità di rotazione degli pneumatici con l’accelerazione rilevata dai sensori, modulando di conseguenza la pressione del circuito idraulico in maniera da evitare il bloccaggio delle ruote. Il TCS funziona in maniera opposta, regolando l’iniezione elettronica per evitare lo slittamento delle gomme durante l’accelerazione.
Di più recente introduzione è il controllo dinamico del veicolo (VDC), in grado di controllare anche la rotazione angolare e le conseguenti accelerazioni centrifughe.
A questi sistemi si aggiungono il computer di bordo (che consente di visualizzare le principali componenti di stato del veicolo, dalla velocità al consumo istantaneo), l’ASR che consente di integrare nel controllo della trazione, frenata e stabilità, garantendo l’intervento elettronico per limitare al minimo le condizioni di instabilità del veicolo.
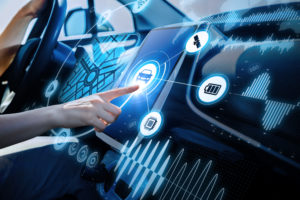
Le cifre della meccatronica italiana
Quanto vale il settore della meccatronica in Italia? Stando ai numeri è decisamente un elemento portante della nostra economia. Le imprese meccatroniche in Italia sono oltre 122mila, pari al 28% del manifatturiero complessivo, e impiegano un totale di oltre un milione e mezzo di addetti. Con circa 120 miliardi di euro di valore aggiunto prodotto, il comparto contribuisce per l’8% al Pil del Paese.
L’export della meccatronica italiana vale 215 miliardi di euro, pari a circa il 15% sul totale delle esportazioni (448 miliardi), con una tendenza ancora in crescita.
Nel primo trimestre del 2018, il giro d’affari complessivo della meccatronica è cresciuto del 3,6%, e la produzione metalmeccanica ha fatto registrare una crescita dei volumi realizzati pari al 4,4% rispetto ai primi tre mesi dell’anno precedente.
Le competenze necessarie per lavorare nella meccatronica
Per quanto riguarda la formazione, la meccatronica è considerata una branca dell’ingegneria che coniuga in maniera sinergica discipline ingegneristiche: meccanica, elettronica, informatica, del software, dell’automazione, della progettazione di sistemi
Nell’istruzione superiore di secondo grado la figura di riferimento è quella del “tecnico superiore di tecnologie digitali per l’industria”, una specializzazione che si acquisisce frequentando un apposito corso della durata di 2 anni istituito nel 2018 dal Gruppo Meccatronici e ICT e Servizi alle Imprese di Assolombarda. Oltre ad avere una formazione comune a tutti i tecnici superiori, specifica di area tecnologica, il tecnico superiore di tecnologie digitali deve possedere conoscenze specialistiche riguardanti le logiche della trasformazione digitale, la gestione di big data, cloud e Internet of things.
Fra le capacità ci sono quelle di saper intervenire in remoto, di interpretare le informazioni di funzionamento degli impianti per prevenire i guasti, di utilizzare tecnologie di realtà aumentata per incrementare l’efficacia della manutenzione. È richiesta altresì esperienza delle tecniche di additive manufacturing, di progettazione e modellizzazione software in ambito meccatronico e capacità di gestire progetti (project management).
Le aree industriali in cui è richiesta la figura di tecnico superiore di tecnologie digitali sono:
• Smart lifecycle, che comprende il processo di sviluppo di un nuovo prodotto, la gestione del ciclo di vita e la gestione dei fornitori collegata a questi due primi aspetti;
• Smart supply chain, che comprende le attività proprie della gestione integrata della supply chain, ovvero la pianificazione dei flussi fisici (vendite, scorte, canali distributivi, produzione, etc.), la gestione degli eventi (monitoraggio e reazione agli scostamenti dal pianificato) oltre che la gestione dei fornitori nell’alveo di queste due attività;
• Smart factory, che comprende i processi core della manifattura (produzione, logistica interna ed esterna, manutenzione, qualità, sicurezza e rispetto delle norme).
I nuovi tecnici dell’industria devono possedere inoltre un elevato livello di “comprensione digitale” che consenta di interagire con i nuovi sistemi manifatturieri. Si richiede anche che siano in grado di comprendere, completare e sviluppare nuovi sistemi digitali, tecnologie di ultima generazione, applicazioni e strumenti. Serve poi la capacità di impiegare e disegnare nuove soluzioni di intelligenza artificiale e di data analytics e saper leggere in maniera critica e complessa le informazioni ricavate. In ambito cybersecurity è necessario comprendere come il digitale accresca l’intera catena del valore della manifattura.
Nel nostro Paese, però, le competenze necessarie alle industrie sono ancora carenti. Durante l’ultima edizione del World Manufacturing Forum, tenutasi nel 2019 e dedicata proprio alle competenze, uno studio intitolato “Skills for the future of manufacturing” ha quantificato l’impatto potenziale dello skill shortage in Italia da qui al 2028, se non verrà colmato il gap di competenze, in una perdita di circa 173 miliardi di pil, cioè lo 0,6% del pil potenziale ogni anno.
(pubblicato per la prima volta il 27 aprile 2020)