Passare dalla fabbrica connessa alla fabbrica intelligente. La sfida oggi per le imprese che hanno intrapreso un percorso Industry 4.0 è basata su due temi fondamenti: da una parte tornare ad avere sempre, anche quando è apparentemente lontano, una massima attenzione al cliente finale e dall’altra focalizzare l’attenzione sui processi di trasformazione dei dati della fabbrica connessa in conoscenza.
«I processi di innovazione messi in moto dall’IoT stanno cambiando radicalmente il panorama competitivo delle imprese – osserva Simone Marchetti, Digital Supply Chain, Sales Development Manager -, e in un contesto di imprese e organizzazioni che vedono crescere in modo esponenziale la disponibilità di dati, il valore è sempre di più nella conoscenza”. Una conoscenza che deve essere messa sempre più spesso in relazione con il fattore tempo. “Il valore – prosegue Marchetti – è nel rapporto tra “Information e Latency“». Tra la quantità e qualità delle informazioni e la rapidità con cui si riesce a trasformarle in conoscenza e in azioni che hanno una diretta rilevanza per il business.
La conoscenza legata a macchine, ambienti, processi, modalità di reazione con clienti è alla base di una trasformazione digitale che si concretizza in fenomeni come la service transformation o “servitizzazione” delle imprese, oppure come la domanda crescente di Hyper customization che sta alla base di nuovi modelli di business, e ancora come un revamping, questa volta concreto e reale, dei principi di customer centricity e parallelamente con un abbandono dei “vecchi” modelli di supply chain a silos verso una logica di supply chain lineare che è nello stesso tempo connessa e integrata.
Indice degli argomenti
Smart Factroy: come e dove cercare nuove forme di competitività
In questo contesto per le imprese del manifatturiero in particolare, la vera domanda è come e dove conquistare una nuova competitività. «La sfida – osserva Marchetti – è nella capacità di unire i due grandi vettori di innovazione interni ed esterni: da una parte la digitalizzazione delle operation che portano alla digital enterprise e dall’altra i processi di digitalizzazione (e comprensione e conoscenza) della customer experience. La convergenza e integrazione di questi due motori di innovazione sono alla base di un vero Digital business e possono essere rappresentati in una sorta di road map che partendo dal business tradizionale ha visto la fase della “Ad hoc digitization”, la “Extented digitization”, e con la fase di ideazione e sviluppo di nuovi modelli di business approda appunto al Digital business».
Centralità del cliente e centralità dei dati
Calare questa road map di digitalizzazione sul mondo del manifatturiero per Oracle significa pensare a una fabbrica che grazie alla capacità di connessione sia nella condizione di seminare intelligenza e di valorizzare, in tempo reale, le informazioni prodotte in forma integrata con tutte le altre componenti aziendali. Per raggiungere questo obiettivo è necessario orchestrare tutti i componenti ed è necessario poterlo fare con un framework di applicazioni Cloud che permettano alle imprese prima di tutto di sperimentare e poi di gestire il passaggio in produzione con un time to market che sia il più possibile rispettoso delle logiche di competitività del mercato nel quale operano. Velocità e precisione sono i due imperativi del digital business.
Le applicazioni disponibili in Cloud permettono ai clienti di disegnare percorsi più rapidi e veloci con un controllo puntale sui costi. La Realtà Aumentata permette di aggiungere informazioni sulla realtà a beneficio degli operatori 4.0 che sono così nella condizione di accelerare i processi di conoscenza o che possono disporre di supporto informativo e formativo per essere più veloci e precisi nelle loro azioni.
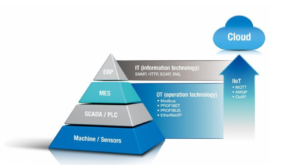
I Big Data e gli analytics permettono di mettere a fattori comune il valore dei dati e di individuare con la data science i pattern e i modelli sui quali lavorare per conoscere meglio i comportamenti dei clienti o per indirizzare meglio l’utilizzo delle macchine o per prevenire e gestirne la manutenzione. I Big data portano poi verso le applicazioni di Intelligenza artificiale che a loro volta accelerano il passaggio dalla conoscenza delle tematiche di fabbrica all’azione sulla produzione e sui prodotti stessi.
La robotica applicata all’Industria 4.0 con le competenze dell’Operatore 4.0 apre a sua volta un altro grande filone di innovazione che fa riferimento alla robotica collaborativa e dunque anche a temi di organizzazione del lavoro, di formazione e di sicurezza. E si arriva così anche alla sicurezza, sia nell’accezione di cybersecurity che sappia comprendere tanto il dominio IT quanto quello OT, sia nel senso di Risk management, per una visione e gestione di tutti i fattori di rischio dell’impresa, da quelli fisici legati alla sicurezza di stabilimento a quelli specifici legati ai dati, sino a quelli correlati alla gestione del business, come possono essere la prevenzione dell’impatto di un guasto in fabbrica sulle vendite in modo da prevenire e gestire il rapporto con i clienti. In questo scenario Marchetti osserva anche l’importanza del ruolo di soluzioni tecnologiche come la Blockchain che permettono di rivedere e riorganizzare le logiche organizzative e di governance delle supply chian e delle filiere estese.
Il ruolo strategico del Cloud
Come orchestrare questi nuovi parametri di business? La risposta è per Oracle sempre più indirizzata al Cloud, in particolare al framework di applicazioni che consente di attuare le grandi priorità dell’Industria 4.0 a partire dalle logiche di convergenza tra IT e OT per scendere ai 4 punti chiave della fabbrica intelligente che sono rappresentati da
- Interoperabilità tra sensori, macchine, ambienti e persone
- Possibilità di sviluppare logiche di Digital Twin, ovvero di creazione di copie virtuali di progetti e problematiche presenti nel mondo reale con la massima fedeltà
- Automazione delle attività di assistenza attraverso sistemi che possono supportare le persone nella gestione di task “trasferibili” alle “macchine”
- Decentralizzazione delle decisioni con soluzioni e device che sono nella condizione di assumere e gestire livelli decisionali in autonomia sulla base di regole predefinite
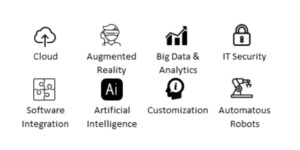
Con la gestione della convergenza IT e OT gli applicativi in Cloud sono nella condizione di entrare nel ciclo gestionale dell’azienda e di sfruttare le informazioni che arrivano dall’Industrial IoT. Le Oracle Cloud Application mettono a disposizione delle aziende la possibilità di disporre, in modo veloce, delle applicazioni negli ambiti più rilevanti per lo sviluppo di soluzioni Smart Factory, vale a dire Internet of Things, Intelligenza Artificiale e Blockchain.
Proprio per creare una sorta di “ponte” tra le prospettive e le aspirazioni dell’Industria 4.0 e la realtà delle imprese italiane Oracle ha voluto preparare una simulazione che grazie alla collaborazione strategica con la società Rexroth del Gruppo Bosch, permette di “toccare con mano” i vantaggi concreti del passaggio dalla fabbrica connessa, che mette a valore la capacità di connessione dell’Internet of Things, alla Fabbrica intelligente, che permette alle aziende di intervenire a 360 gradi sulle leve di business attuali e potenziali.
La leva innovativa è nella cultura e nella collaborazione tra IT e OT
Sergio Gimelli, Sales Consultant Director Oracle, ricorda innanzitutto che la grande sfida è prima di tutto quella di coniugare l’incontro tra IT e OT e di portare le concrete opportunità della digital transformation nello stabilimento e in tutta la fabbrica.
Gimelli presenta questa esperienza con Lorenzo Zerbi, Responsabile sales product management, Electric Drives and Controls di Bosch Rexroth anche nella prospettiva di una integrazione IT – OT a livello di provider e competenze.
Nello specifico poi Gimelli ci tiene a precisare come il suo percorso professionale sia effettivamente partito dal mondo OT, delle operations di fabbrica, per poi passare al “digitale” e all’IT e proprio questa esperienza su entrambi i “campi” lo porta oggi a considerare che chi intende, come Oracle e i suoi partner, fornire soluzioni, servizi, supporto per la trasformazione digitale, deve partecipare al confronto IT e OT. Portare soluzioni, mettere a disposizione applicazioni e competenze per portare le imprese dalla “connessione spinta” alla Smart Factory significa affrontare un percorso di integrazione tra due “visioni” del digitale per l’impresa.
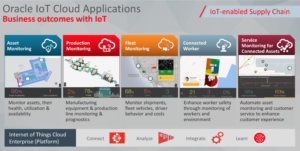
E proprio per questo per Gimelli occorre partire dalla considerazione che il rapporto IT e OT va visto prima di tutto sul tema dei dati. “Per chi arriva dall’OT la fabbrica connessa non è una novità, la vera innovazione è nella capacità di integrare e far convergere i processi di innovazione dell’IT con quelli dell’OT. In altre parole, la vera sfida – prosegue Gimelli – è nell’integrazione tra i due mondi”.
Nello specifico poi il tema dell’OT è da leggere nella definizione di obiettivi chiari e precisi da assegnare al lavoro sui dati: “Occorre cioè – rileva – avere ben chiaro cosa fare con i dati, come gestirli e come accelerare e mettere in relazione tutti i processi di trasformazione in conoscenza”.
Controllo e guida della fabbrica da remoto e in real time
Al centro dell’esperienza presentata da Oracle abbiamo un direttore di produzione di una impresa del manifatturiero. E’ in viaggio per lavoro e riceve un messaggio sms dai sensori IoT che rilevano un problema. La messaggistica è uno dei “segnali” della fabbrica connessa, ma con la soluzione sviluppata grazie al framework di applicazioni Oracle quest’azienda si è arricchita di contenuti Smart Factory. Grazie a questa soluzione il direttore di fabbrica può disporre in remoto può di un digital twin dello stabilimento nel quale si è attivato l’alert. Il direttore di produzione è in questo modo nella condizione di controllare le fabbriche presenti in diverse parti del mondo, disponendo di una rappresentazione fedele (digital twin) degli stabilimenti e delle attività.
Da remoto può disporre di informazioni che lo aiutano a individuare il problema e a fornire indicazioni per risolverlo ma soprattutto, a prescindere al fatto che ci sia la segnalazione di un problema, il manager è nella condizione di avere sotto controllo i kpi di riferimento della produzione con diversi livelli di dettaglio e di approfondimento. Può infatti vedere che le fabbriche in Italia hanno performance inferiori di una determinata percentuale rispetto alla loro normale capacità produttiva, mentre gli stabilimenti in un altro paese sono “sotto pressione” e può controllare chiaramente i kpi di ciascun stabilimento. Anche se in viaggio e non in condizioni normali il direttore ha gli strumenti per scendere nel dettaglio dell’analisi delle linee di produzione in difficoltà e può raffinare l’analisi sino a individuare il problema in modo preciso, nello stesso tempo ha gli elementi per prevenire i rischi collegati a un sovraccarico di lavoro nello stabilimento in una diversa area del mondo e ha gli elementi di analisi per mettere in relazione la produzione in Italia e la produzione in un altro paese con le attività commerciali correnti dell’azienda.
I Kpi della Connected factory e della Smart factroy
Per questo tipo di analisi il direttore di produzione non dispone solo dei Kpi delle macchine, non si ferma alle “connected machine“, ma ha la possibilità di mettere in relazione, in tempo reale, questi dati con il tipo di produzione, con le richieste dell’area vendite, con gli impegni con i clienti e con le performance su tutta la filiera, nel caso di gestione di situazioni eccezionali. Ovvero dispone di informazioni che gli permettono di valutare correttamente tutti i rischi collegati a una molteplicità di interventi. Nello specifico di questa simulazione il direttore di produzione arriva al livello di dettaglio di capire che ci sono un certo numero “prodotti” a rischio di consegna. Nella sua vista completa il direttore di produzione è nella condizione di vedere subito l’impatto del problema sul business e di disporre degli strumenti per gestire questo impatto, sia dal punto di vista degli interventi nello stabilimento, sia per quanto riguarda le azioni correttive sul business.
Il manager può verificare direttamente, in live, il comportamento dei parametri di produzione interessanti per risolvere il problema e può approfondire la conoscenza sui dettagli che considera più significativi, come possono essere ad esempio la possibilità di “ascoltare” una eventuale vibrazione anomala della macchina e può metterla in relazione con gli altri dati per fare un assessment delle possibili conseguenze nel tempo e preparare delle contromisure.
In conclusione il direttore di fabbrica può disporre di tutti gli elementi per sviluppare una corretta strategia e un piano d’azione specifico ed è nella condizione di intervenire da remoto sui parametri della fabbrica e sulle principali leve operative dello stabilimento.
Ma come osserva Gimelli la fabbrica non vive da sola, “non è solo produzione”, deve anzi essere in relazione costante, attiva e bidirezionale, ad esempio con il gestionale ERP, che deve essere sempre più collegato con la produzione e, a sua volta, con le applicazioni di business e dunque anche in linea con le vendite e con i clienti.
Dai sensori IoT ai clienti
In assoluto il modello permette di portare intelligenza nella relazione tra sensori di fabbrica intesi come i terminali più vicini alla produzione e i dati e con la conoscenza delle esigenze dei clienti per sviluppare analisi in tempo reale e per avere delle viste, non solo del “comportamento” delle macchine connesse, quanto delle relazioni tra le performance di vendita e le performance di stabilimento.
A questo livello di analisi, verifica e controllo si aggiunge poi quello che arriva dalle applicazioni di machine learning. Gimelli mette in evidenza che nella fabbrica la conoscenza non è mai statica ma è costantemente legata alla dinamica di produzione sulla base di una serie di informazioni e di dati che arrivano da una molteplicità di fonti che sono soggette a una molteplicità di relazioni. Ed è qui che si collocano le soluzioni di Machine Learning che sono nella condizione di “suggerire” alle macchine come comportarsi, piuttosto che accelerare i processi decisionali che comprendono anche la conoscenza continua che arriva dalle macchine stesse. Portare questa conoscenza in connessione con le applicazioni gestionali consente alle aziende di disporre di una serie di raccomandazioni, di suggerimenti e indicazioni che permettono di unire l’esperienza degli operatori OT con la conoscenza prodotta dalle macchine stesse.