La smart factory, nella sua definizione più ampia, è un sistema flessibile, in grado di ottimizzare la produzione e di adattarsi ai cambiamenti in maniera più o meno autonoma, attraverso l’integrazione di informazioni provenienti dal campo (OT – Operational Technology) e dai sistemi gestionali (IT – Information Technology). Ci focalizzeremo su un tema pratico, che permette di indirizzare meglio i benefici derivanti dall’applicazione degli strumenti del Piano Transizione 4.0, evoluzione della “Legge Calenda” che ha introdotto in Italia il Piano Industria 4.0, e che ha generato, secondo i dati di Confindustria, un aumento di 10,2 miliardi di investimenti nel 2017 per le PMI che precedentemente non avevano investito in tecnologie 4.0 negli anni precedenti. Vedremo una possibile architettura per ricavare l’OEE – Overall Equipment Effectiveness (e, di conseguenza, rispettare uno dei requisiti di una smart factory), e come utilizzarlo nella pratica per ottenere da subito un miglioramento dell’efficienza attraverso l’integrazione dei sistemi di fabbrica e gestionali.
Indice degli argomenti
Dal Piano Industria 4.0 al Piano Transizione 4.0
“Si stima che gli investimenti agevolati in tecnologie 4.0 nel 2017 abbiano prodotto, tra gennaio 2017 e marzo 2019, una maggiore crescita occupazionale nelle imprese che ne hanno beneficiato, rispetto ad imprese simili che non ne hanno beneficiato, di circa 7 punti percentuali. L’aumento degli occupati ha riguardato soprattutto giovani, operai specializzati e i conduttori di impianti e macchinari, anche in imprese localizzate nel Mezzogiorno” (Centro Studi Confindustria, 10/10/2020)
Se consideriamo i beni riconosciuti dal MISE nell’Allegato A del Piano Industria 4.0 come “funzionali alla trasformazione tecnologica e digitale delle imprese secondo il modello Industria 4.0”, troviamo che i requisiti di interconnessione, ulteriormente dettagliati nella circolare dell’Agenzia delle Entrate 4/E del 2017, prevedono che:
scambi informazioni con sistemi interni (es.: sistema gestionale, sistemi di pianificazione, sistemi di progettazione e sviluppo del prodotto, monitoraggio, anche in remoto, e controllo, altre macchine dello stabilimento, ecc.) e/o esterni (es.: clienti, fornitori, partner nella progettazione e sviluppo collaborativo, altri siti di produzione, supply chain, ecc.) per mezzo di un collegamento basato su specifiche documentate, disponibili pubblicamente e internazionalmente riconosciute (esempi: TCPIP, HTTP, MQTT, ecc.); (Ulteriori chiarimenti in materia di “interconnessione” e “integrazione automatizzata” – Pag. 12)
il requisito di integrazione di tipo informativo con il sistema logistico può essere soddisfatto attraverso l’impiego di beni immateriali tra quelli citati dall’allegato B (software, sistemi e system integration, piattaforme e applicazioni) e anche con l’impiego di più sistemi operanti in modo concorrente e complementare (ad esempio: inoltro di istruzioni e/o part-program da sistema CAD/CAM, rilievo dati e generazione indice di efficacia totale di un impianto Oee da sistema MES) (pag. 14).
OEE come misura e come strumento di ottimizzazione
L’Overall Equipment Effectiveness (OEE) misura l’efficacia totale di un impianto attraverso la misurazione di tre caratteristiche importanti:
- La disponibilità (Availability), misurata come il tempo in cui l’impianto è disponibile per la produzione
- L’efficienza (Effectiveness) che fornisce una misura della velocità di produzione attuale rispetto a quella pianificata
- La qualità (Quality) delle unità prodotte, indicata come percentuale di prodotti conformi rispetto al totale della produzione
Questi KPI (OEE, Availability, Quality, Effectiveness), nati con le iniziative di Lean Production e formalizzati dalla norma ISO 22400, permettono di comprendere l’effetto delle azioni adottate nel sistema produttivo, e di fornire una misura oggettiva della loro efficacia.
La disponibilità di queste informazioni, la loro condivisione con tutti gli attori coinvolti nel ciclo produttivo (dal responsabile di stabilimento all’operatore di macchina), e la definizione univoca permettono di far parlare le persone attraverso un vocabolario comune e una interpretazione univoca, evitando fraintendimenti.
“Senza dati sei solo un’altra persona con un’opinione”, E. Deming
Nelle iniziative di Industria 4.0 l’interconnessione con macchine intelligenti permette di calcolare in real time e senza (o minimo, come vedremo) intervento manuale questi KPI, e di condividerli con tutti gli interessati. È la logica della smart factory.
L’integrazione OT/IT per la misura efficace dell’OEE
Facciamo l’esempio di un tornio CNC, dotato di connessione alla rete OT e gestito attraverso un sistema ERP/MES sulla rete IT, per descrivere come sia possibile calcolarne l’OEE, per ciascuna delle sue componenti:
- L’availability è composta da più misure, alcune ricavabili in automatico dalla macchina, dove ciascuna installazione ha un diverso modo per ricavare i tempi indicati dalla ISO 22400
Alcune informazioni, tipicamente quelle di tipo “Actual”, possono essere ricavate direttamente dalla macchina, ad esempio:
- Actual Unit Down Time, ricavato dalla somma dei tempi in cui il PLC rileva un fermo per allarme
- Actual Setup Time, ricavato dalla somma dei tempi in cui lo stato della macchina è impostato su “Manuale”
- Actual Unit Processing Time, ricavato dalla somma dei tempi in cui la macchina è impostata su “Automatico”
Altre informazioni invece sono ricavabili dai sistemi ERP o MES, dove si svolgono le attività di pianificazione, come ad esempio:
- il Planned Operation Time, dal calendario di fabbrica dell’ERP o del MES
- Il Planned Down Time, ricavato dalla somma dei tempi di intervento degli ordini di manutenzione inseriti sull’ERP
- L’effectiveness è ricavata in parte dal PLC, con la misura dell’output di produzione effettivo, e in parte dal sistema ERP, attraverso l’indicazione della produzione oraria teorica per uno specifico prodotto
- La quality può essere ricavata sia manualmente, attraverso le dichiarazioni di scarto presenti sul MES, che automaticamente, nel caso la macchina sia dotata di sistemi di rilevazione della non conformità integrati con il PLC
Queste misurazioni possono essere archiviate in un DB, o meglio in un Data lake, arricchendole sia con informazioni gestionali (es. il numero dell’Ordine di produzione, il codice prodotto, il codice lotto, …) che con informazioni di processo (es. la velocità del mandrino, il consumo elettrico, la matricola dell’utensile, …) che permettono in un secondo tempo di effettuare analisi mirate o di individuare le condizioni che hanno portato ad anomalie nella produzione di un lotto specifico.
Le componenti architetturali di una soluzione smart factory
Il modello di riferimento per le architetture Industria 4.0 è il RAMI 4.0, sviluppato da Platform Industrie 4.0, l’iniziativa del governo tedesco per la modernizzazione dell’industria, e inserito dalla Commissione Europea nel Digital Transformation Monitor.
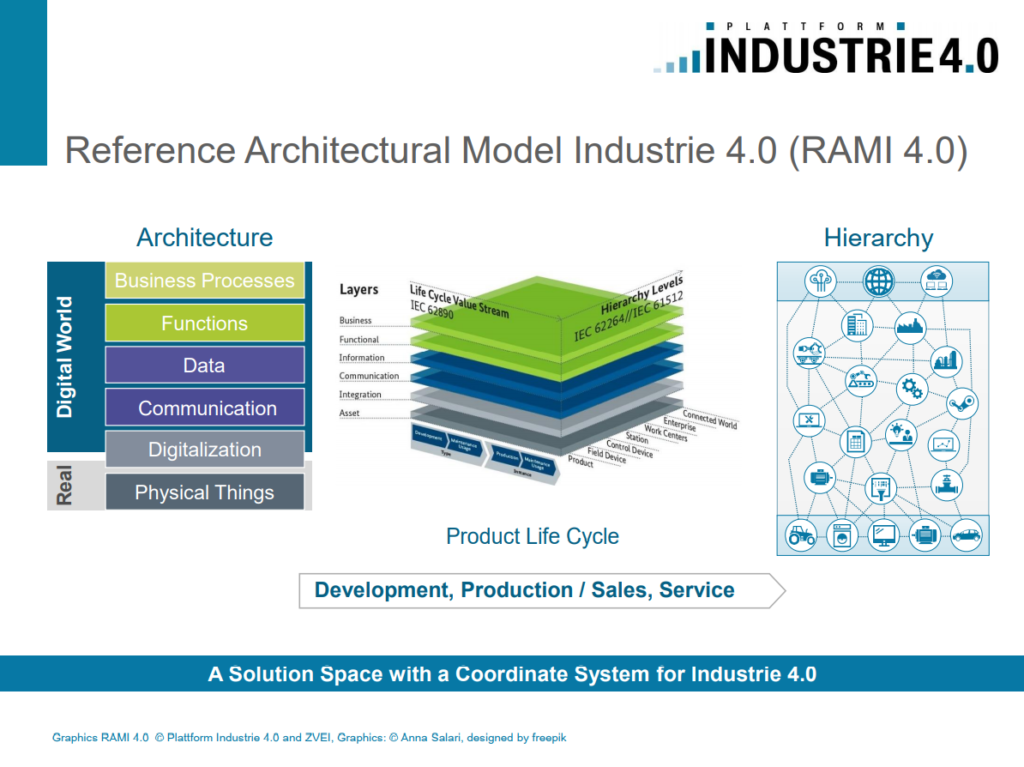
Nel modello RAMI 4.0 vengono descritti tre diversi assi, relativi alla Gerarchia di fabbrica (dove sono descritte le relazioni tra sistemi, le comunicazioni e le interazioni tra Mondo Connesso, Smart Factory e Smart Products), al Ciclo di vita del prodotto (dallo sviluppo alla manutenzione) e, l’Architettura che utilizzeremo come modello per questo esempio.
Se riprendiamo il nostro caso del calcolo dell’OEE possiamo vedere come, per ottenere l’informazione (che è al livello di Business Process), è necessario interagire con l’oggetto fisico, digitalizzarne l’informazione, comunicare con un sistema di raccolta e integrare i dati necessari.
Per raccogliere l’informazione dal tornio serve quindi più componenti di architettura che:
- Convertano il dato fisico in digitale, e normalmente questa funzione è svolta dal controllo numerico a bordo della macchina, che utilizza i vari sensori per raccogliere le misure fisiche
- Comunichino in maniera sicura le informazioni provenienti dal campo verso lo strato di elaborazione/memorizzazione. Una possibilità è costituita da un gateway IoT che traduce il dialetto specifico del PLC (standard come OPC/UA o Modbus, oppure proprietario) in un formato digitale (come ad esempio un messaggio MQTT) e lo invii in maniera sicura su un canale TCP/IP, per la successiva elaborazione al livello di raccolta dati
- Raccolgano le informazioni provenienti dai sistemi gestionali ERP o MES e li integrino nel flusso di elaborazione proveniente dal campo
- Elaborino le informazioni per ottenere la misurazione dei KPI dell’OEE, integrando dati OT ed IT
- Visualizzino le informazioni attraverso cruscotti in grado di rappresentare al meglio le informazioni per l’uso da parte delle persone interessate
Scendendo a livello di implementazione, le componenti descritte prima possono essere realizzate con un’architettura moderna basata su servizi Cloud, ad esempio in questo modo:

In questo modo è possibile realizzare un’applicazione modulare, che può essere estesa in futuro senza vincolare l’azienda all’uso di soluzioni monolitiche, permettendo di misurare l’OEE (e di soddisfare parte dei requisiti di interconnessione previsti dal Piano Transizione 4.0).
Il beneficio per le persone coinvolte nella gestione della produzione è la disponibilità di un linguaggio comune per indirizzare al meglio i processi di miglioramento della produzione.
In un’ottica di miglioramento continuo, l’introduzione di un sistema di misura dell’OEE coerente con Industria 4.0 attraverso un’architettura standard, permette di migliorare da subito, con un impatto relativamente basso sui processi e sulle persone, l’efficienza della produzione, ponendo le basi per le successive fasi di adozione delle pratiche della Smart factory.