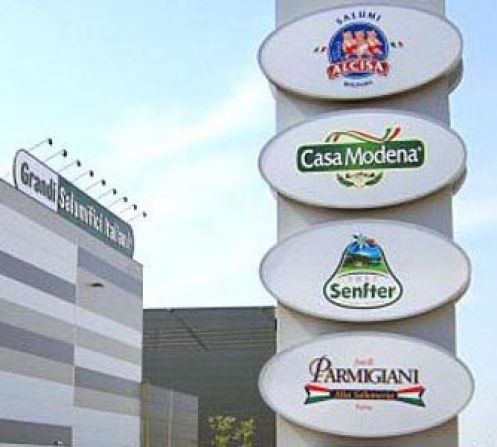
La Cool/Cold Chain, o logistica del freddo, è la movimentazione dei prodotti freschi a qualità garantita grazie alle tecnologie, per esempio tramite l’uso dell’Rfid e di una sensoristica capace di segnalare ogni variazione di temperatura lungo tutta la filiera. Il monitoraggio automatico costante, che triangola tag, lettori e intelligenza di sistema, assicura che i prodotti siano altamente controllati in qualsiasi stagione o condizione climatica.
Le variazioni di temperatura infatti possono alterare la qualità di un alimento compromettendo proprietà organolettiche e nutritive. D’altra parte, per tutelare la salute dei consumatori, il deperimento del prodotto è talmente controllato da GDO e aziende del largo consumo che spesso in fase di consegna i prodotti sono respinti solo per vizi di forma, cioè per letture delle temperature non corrispondenti alla realtà a causa delle escursioni termiche tra ambiente frigorifero ed esterno.
Per Grandi Salumifici Italiani la quantità di merce respinta per questo motivo era pari allo 0,5% della produzione: 30 tonnellate di prodotti su 120mila ogni anno. Una quantità che, per legge, doveva andare distrutta anche se era assolutamente integra e ottima, come verificavano ogni volta in GSI quando controllavano i prodotti di ritorno.
Indice degli argomenti
L’esigenza di eliminare lo spreco dello 0,5% della produzione
Nel ripensare ex novo il magazzino, GSI ha deciso quindi di gestire la logistica del freddo ad alta automazione, sia per aumentare velocità ed efficienza, sia per ridurre inutili sprechi, inaccettabili anche eticamente, soprattutto in tempi di crisi economica. Con Id Solutions e l’Rfid Lab di Parma, GSI ha quindi introdotto la radiofrequenza a supporto delle procedure di movimentazione, inserendo tag Rfid nei pallet e sensori wireless IoT di temperature nelle tratte dei camion.
Multispecialista, multicanale e con una forte presenza internazionale, il Gruppo Grandi Salumifici Italiani ha un assortimento di tutte le produzioni tipiche italiane, con i marchi Casa Modena, Senfter, F.lli Parmigiani, Cavazzuti e Gasser. Conta 12 stabilimenti in Italia, 4 società all’estero per un totale di 1700 dipendenti e una rete vendita di oltre 350 persone, oltre a una struttura commerciale per l’estero.
La piattaforma centrale di produzione a Bologna e la struttura di Ricerca e Sviluppo e Controllo Qualità lavorano in modo integrato, insieme alla rete logistica con 22 piattaforme di distribuzione in Italia e due con stock all’estero, in Germania e Francia. La reingegnerizzazione della logistica del freddo è stata capitanata dalla direzione Logistica e Supply Chain.
«Le nostre linee guida erano molto precise – racconta Ivano Poli, direttore Logistica & Supply Chain -: seguire il cliente nell’esigenza di avere lead time ordine/consegna sempre più brevi, ottimizzare le preparazioni riducendo gli errori, aumentare la velocità e la sicurezza dei processi di lavorazione, l’efficienza e il controllo nei trasporti e il presidio della temperatura lungo tutta la supply chain».
Tempi di scarico ridotti del 25%
Il fulcro del progetto è stata la nuova base logistica interporto di Bologna a cui i vari stabilimenti GSI consegnano attraverso una decina di trasportatori: 30mila metri quadri di superficie che ospitano quasi 40mila pallet (circa 35mila fresco, 1600 salami e 2800 circa secco), disposti su sette livelli. La tecnologia Rfid ha coinvolto 3mila referenze. Grazie a picking dinamico e sincronizzazione delle informazioni, sono stati velocizzati i processi e azzerati gli errori, supportando una movimentazione in uscita pari a 400mila unità logistiche consegnate a oltre 30mila clienti.
Il sistema di sensori wireless invece è stato mirato al controllo della variazione termica lungo la supply chain. Dalla collaborazione tra GSI e l’Rfid Lab è nato un modello realizzato dal Dipartimento di Ingegneria Industriale dell’Università di Parma, testato su diverse tipologie di prodotti, e basato su variabili come massa del prodotto, temperatura alla partenza, temperature in viaggio, e permanenze temporali a tali temperature, con rilevazione è su ogni singola referenza.
«La gestione dei carichi attraverso un sistema semaforiale di sicurezza – aggiunge Poli – è stato accolto molto positivamente dagli operatori: quando hanno visto la velocità dei passaggi hanno subito capito vantaggi e praticità, e ora chiamano “telepass” i gate Rfid. La preparazione dei Trc oggi è davvero veloce e soprattutto molto più sicura».
«Attraverso una dashboard accediamo via cloud al sistema di gestione in standard Gs1. Ogni codice SSCC in spedizione è identificato con etichetta Rfid. Il sistema di tracciabilità automatica delle spedizioni identifica il carico dei prodotti sui camion in attesa alle bocche di carico/scarico attrezzate con varco Rfid. I risultati del progetto sono l’eliminazione degli errori in spedizione e nei dati, e un miglior servizio ai destinatari che automatizzano il ricevimento e controllo se attrezzati con banchine di ricevimento Rfid. Inoltre i tempi di scarico si sono ridotti del 25%».