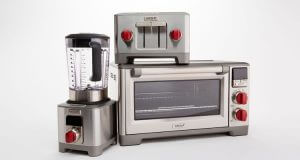
Una sede centrale a Madison, nel Wisconsin, e filiali nel cinque continenti, Sub-Zero è un’azienda privata (di proprietà della famiglia Bakke, che l’ha fondata negli anni Cinquanta) con un organico di un migliaio di dipendenti, che produce frigoriferi da incasso a marchio proprio ed elettrodomestici da cucina come cappe aspiranti, macchine per caffè, piani cottura, cantinette per vino, forni da incasso e a microonde con il brand Wolf.
La società due anni fa ha aperto un nuovo impianto a Goodyear, in Arizona, introducendo nel processo produttivo anche 60 nuovi elettrodomestici. Il progetto avviato tre anni fa, battezzato “New Generation Collaboration Initiative”, rappresentava una sfida importante per l’IT di Sub-Zero. I team di sviluppo e integrazione necessitavano di una comunicazione continua e di una più ampia collaborazione sulle attività di ideazione e sviluppo. Una situazione penalizzata dal fatto di dover far dialogare con costanza le linee di business (LOB) e i team di sviluppo presenti nella sede operativa di Madison con la facility di produzione di Goodyear senza dover per forza organizzare un meeting fisico presso una delle due sedi.
Grazie alla tecnologia TelePresence e wireless Cisco e alle videocamere smart di Librestream, la
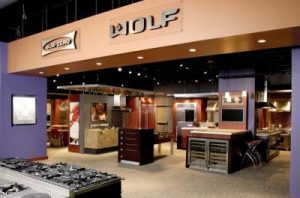
società è stata in grado di collegare i team di ingegneri attraverso sessioni video live, attivando nuove forme di sviluppo collaborativo in tempo reale con i propri colleghi sparsi nel mondo (ma anche con fornitori e distributori), riducendo sensibilmente errori e bug, con il risultato di un deciso miglioramento della produttività e la riduzione del time-to-market. I cicli d’introduzione dei nuovi prodotti si sono accorciati in misura variabile dal 10 al 20% a seconda delle referenze mentre i fermi macchina si sono ridotti tra il 5 e il 10% e hanno permesso all’azienda di risparmiare in media 2.500 dollari per ciascuna linea di produzione. I risparmi sulle attività di test sul campo si attestano, invece, nell’ordine dei 100mila dollari l’anno. Come? Semplicemente utilizzando il video in abbinamento ad applicazioni di diagnostic data streaming.
Indice degli argomenti
Migliora la qualità e la produttività dello staff

I vertici della società si erano imposti obiettivi ambiziosi, con un timing particolarmente accelerato legato al lancio quasi simultaneo di 60 nuovi prodotti. A tutto questo sia aggiungeva la necessità di adeguarsi a rigorosi requisiti di controllo qualità e all’obiettivo di migliorare la produttività dello staff.
La soluzione realizzata prevede l’integrazione di funzionalità di mobile video, streaming video e mobile conferencing all’interno del procedimento produttivo, per trarre il massimo vantaggio dall’infrastruttura creata per supportare una connessione pervasiva di macchinari e persone in ottica IoT. Oggi anche i fornitori sono coinvolti attivamente nelle procedure di condivisione delle problematiche di produzione. Tutti sono in grado di partecipare a sessioni di live video sicure, con funzionalità di onscreen mark-up e tecniche avanzate di annotazione video (la cosiddetta telestration) e condivisione delle immagini, accelerando il processo di decision making.
Come evidenziato in questa case history, l’uso di telecamere smart e connesse di Librestream, unite all’infrastruttura di rete di Cisco, hanno permesso agli ingegneri di Sub-Zero di operare con logiche Industry 4.0 da remoto per vedere, parlare e interagire gli uni con gli altri attraverso il proprio tablet o computer. Nell’arco di due anni, Sub-Zero è riuscita a integrare il mobile video internamente e con i fornitori esterni, ottenendo un risparmio che oscilla dal 10 al 20% dei costi di processo: oggi i team sono in grado di mostrare gli ultimi prototipi ai colleghi dei diversi stabilimenti usando le funzionalità telestrate delle videocamere smart per comprendere se ci sono imperfezioni o errori di progettazione e intervenire tempestivamente.
All’interno del nuovo stabilimento di Goodyear, il team IT ha ottenuto il duplice risultato di migliorare la flessibilità
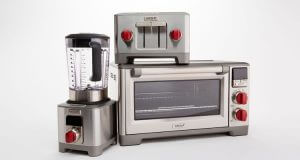
e ridurre i tempi di fermo machine grazie alla possibilità di connettersi direttamente ai tecnici esperti senza dover attendere una loro visita in sede, così da riuscire a intervenire quotidianamente sui problemi senza rallentare il ritmo della produzione. Sub-Zero stima un risparmio interno di 2.500 dollari l’ora per ciascuna linea produttiva, con una riduzione diretta del 5-10% dei fermi macchina relativi ai problemi di design e progettazione dei prodotti e un risparmio annuo di 40mila dollari legato alle trasferte dei soli ingegneri.
Con l’IoT cresce l’intelligenza in fabbrica
Nelle ispezioni sul campo, Sub-Zero oggi ha ridotto il numero di ingegneri richiesti grazie alla possibilità di operare
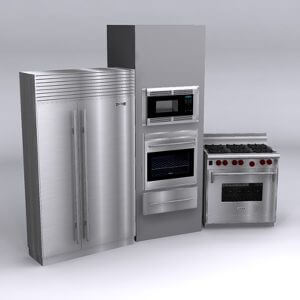
in teleconferenza con i colleghi presenti in sede attraverso le applicazioni di mobile video. Un procedimento che normalmente richiedeva la presenza contestuale presso la casa del cliente di due persone oggi si risolve mandando una persona, il che ha permesso di ottenere risparmi per circa 100mila dollari (risparmi medi per ciascun intervento compresi tra i 2.500 e i 5.000 dollari) e ridotto i tempi di intervento da un paio di giorni a poche ore.
In futuro, la società ha intenzione di incorporare le funzionalità di mobile video collaboration in modo pervasivo all’interno del processo di audit dei fornitori, così come nell’organizzazione dei servizi sul campo, migliorando la customer experience sia per i clienti finali che per i partner manutentori.
Il ruolo di Cisco nella Predictive Maintenance dei robot di FANUC con Artificial Intelligence, IoT e Cloud
Industria 4.0, le startup nel mirino di H-Farm e Cisco
Cisco, Cefriel e Italtel insieme per un Made in Italy 4.0 a base di IoT e Industria 4.0
Immagini fornite da Sub-Zero
Cisco
case History
Digitaliani