A fine maggio si è svolto nel parco fieristico di Parma SPS IPC Drives Italia 2016. Essendo l’Italia il secondo produttore europeo, dopo la Germania, per i macchinari e i sistemi di produzione, quella di Parma è una delle più grandi manifestazioni del settore. Non stupisce quindi che la Siemens, che pur essendo una multinazionale tedesca ha una presenza, sia quantitativa che qualitativa, molto importante nel Paese, abbia indetto di recente una conferenza stampa per illustrare lo stato delle cose e ciò che si sta sviluppando in questo campo.
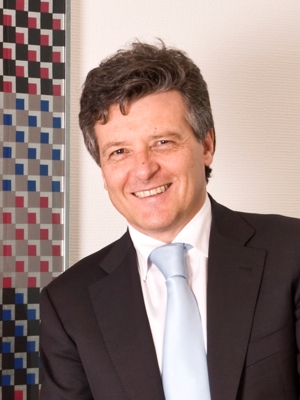
Giuliano Busetto, Country Divisions Lead Digital Factory e Process Industries and Drives (titolo descrittivo delle due divisioni da lui guidate) ha esordito citando i risultati economici sia di Siemens Italia, che nel 2015 ha segnato un aumento del fatturato totale superando gli 1,77 miliardi di euro, sia delle ‘sue’ divisioni: DF e PID. Queste, dopo una lieve flessione congiunturale nel 2013, hanno segnato nel biennio ’14-15 una crescita costante sia nelle revenue che nell’ordinato (che in questo campo hanno andamenti sfalsati nel tempo) e oggi realizzano più del 50% dell’intero giro d’affari della filiale italiana. Motori di questo successo, per Busetto, sono: l’attenzione ai costruttori di macchinari e alle relative realtà-guida; la forte crescita nel packaging spinta dal centro di competenza globale di Bologna; un nuovo sviluppo nel food & beverage; il consolidamento nell’automotive (citando i record di flessibilità e time-to-market della FCA Maserati di Grugliasco) e infine la divulgazione e promozione dei temi relativi alla nuova frontiera del manufacturing, la cosiddetta Industry 4.0.
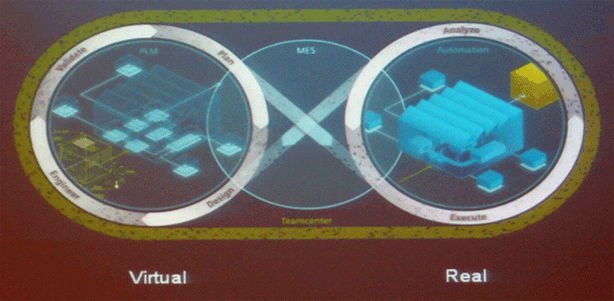
Questa, in poche parole, prevede di ripensare la produzione sul concetto di un modello operativo che integri le attività di Plm, Mes e automazione in un processo a ciclo chiuso e self-feeding, che allinei e tenga allineati il mondo virtuale con quello reale per tutto il ciclo di vita del prodotto, dal progetto al servizio post-vendita attraverso un ‘gemello virtuale’ del prodotto/servizio sul quale anticipare i problemi e testare le soluzioni prima di trasferirle nel reale. Come si può intuire, non è un’idea del tutto nuova e non è solo Siemens che vi sta lavorando. Ma giungere a una piattaforma software che abiliti il ciclo chiuso di cui s’è detto non è facile. Sia per la complessità dei processi da integrare sia, come ha osservato Busetto, “per il difficile ma indispensabile dialogo con chi fa macchine e impianti, che è poi quello che decide”. Su questa strada Siemens ha però il vantaggio di avere già creato, con la Digital Enterprise Software Suite, un unico data model per tutte le informazioni tecniche usate dai sistemi Plm e Mes. Con il Closed Loop Manufacturing (vedi figura) si tratta di fare un passo avanti trasformando il data model già validato nel mondo virtuale in dati direttamente comprensibili ed eseguibili dai sistemi di automazione. Che possono quindi dare un feed-back tale per cui ogni modifica operata in fabbrica, nel reale, sarà disponibile per agire sul ‘gemello virtuale’ attivando un ciclo virtuoso in cui i due mondi si ottimizzano a vicenda.