Nel corso del Convegno di presentazione dei dati dell’Osservatorio Industria 4.0 della School of Management del Politecnico di Milano , Sergio Terzi, direttore dell’Osservatorio, è intervenuto illustrando i risultati di una ricerca ad hoc sul tema specifico del ‘che fare’ per la digitalizzazione della fabbrica, ovvero del processo produttivo, e in particolar modo sugli standard cui fare riferimento in tale percorso. Una tematica la cui conoscenza, che un anno fa rivelava un pesante ‘digital divide’ da parte delle nostre imprese, oggi s’incomincia a diffondere.
Prima di entrare nel discorso va detto che la classica piramide della digitalizzazione di fabbrica data dall’incrocio dei vari livelli operativi con i relativi processi di integrazione orizzontale e verticale (figura 1), oggi grazie a fenomeni come il cloud, lo sviluppo software per componenti (app e microservizi) e soprattutto l’IoT tende a essere sempre più destrutturata. Grazie alla potenza di sistemi capaci di realizzare una filiera informativa più corta e integrata che dalla cattura dei dati sul campo giunge sino alle analisi per i decisori aziendali, la vecchia ‘piramide’ si appiattisce e si trasforma in un nuovo modello. In questo schema (figura 2) che oggi è ancora una visione ma, sostiene Terzi, si sta mano a mano realizzando, i sistemi per la gestione del business e quelli per la gestione della produzione, il ciclo di vita del prodotto e il controllo fisico delle linee e dei macchinari si integrano e completano nel realizzare la ‘digital enterprise’ nel senso più proprio di tale espressione.
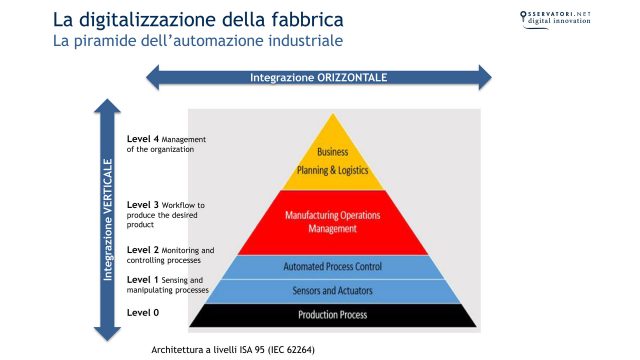
In questa visione è ovviamente fondamentale il ruolo dell’interoperabilità, che è la capacità di sistemi che comprendono non solo impianti e macchine ma anche, stante l’IoT, prodotti e componenti, di comunicare e interagire con altri sistemi. Come è intuibile, ciò si può fare se vengono stabiliti degli standard comuni, che quanto più saranno adottati e diffusi tanto più potranno dare, oltre al plus operativo dell’interoperabilità dei sistemi, altri due vantaggi di rilevanza strategica: primo, ridurre i costi di produzione ed essere più competitivi grazie a un migliore rapporto prezzo/qualità; secondo, evitare di legarsi a un vendor che, osserva Terzi, “magari sta dall’altra parte del mondo”.
La standardizzazione, e di conseguenza l’interoperabilità, è spinta da organizzazioni di vario profilo e struttura. Terzi ha citato alcuni tra i più rilevanti per l’Industry 4.0, come l’OMAC (Organization for Machine Automation & Control), l’Industrial Internet Consortium, l’Obiect Management Group, la OPC Foundation e PLCopen (che insieme hanno proposto la OPC Unified Architecture), ma l’indagine dell’Osservatorio ne ha considerati molti di più, a partire come ovvio dal corpo normativo ISO.
Di standard si parla da tempo in molte sedi e, recentemente, anche a livello governativo. Nella circolare n. 4/E relativa al Piano Nazionale Industria 4.0 che il 30 marzo scorso il Ministero dello Sviluppo Economico ha inviato alle Direzioni regionali e provinciali, nonché agli uffici dell’Agenzia delle Entrate, si legge: “…l’interconnessione ai sistemi informatici di fabbrica con caricamento in remoto di istruzioni e/o part program [elementi di controllo numerico – ndr] è soddisfatta se il bene scambia informazioni con i sistemi interni [segue elenco – ndr] per mezzo di un collegamento basato su specifiche documentate, disponibili pubblicamente e internazionalmente riconosciute”. In altre parole (il corsivo è nostro) su degli standard.
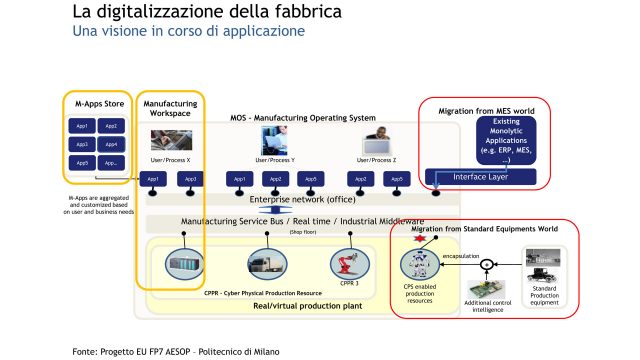
Gli standard IoT per la fabbrica
Nel tema della standardizzazione entra ovviamente anche il discorso sull’Industrial IoT, sull’impiego cioè delle possibilità dell’IoT in fabbrica. Si tratta di un’area che secondo le analisi dello stesso Osservatorio ha raccolto nel 2016 il 63% dei progetti d’Industria 4.0, per un mercato di circa un miliardo di euro, ed è stato quello in maggiore crescita, con un +27% rispetto all’anno prima. Esiste in merito un’architettura già consolidata e codificata dall’Industrial Internet Consortium che abilita diverse funzionalità, dalla gestione dei dispositivi all’acquisizione e gestione dei dati e alla sicurezza.
Il tavolo di lavoro tecnico dell’Osservatorio ha mappato sulle cinque categorie funzionali identificate per l’Industrial IoT i diversi standard internazionali relativi a tali funzionalità (figura 3).
L’Osservatorio ha elaborato diversi scenari relativi a vari progetti di preinstallazione, in particolare relativi all’Industrial IoT, che hanno confermato la fattibilità di implementazioni basate su standard disponibili. Ad esempio, per il controllo del processo di produzione (uno degli scenari più probabili e diffusi) lo standard che comanda è l’OPC-UA, cioè la già citata OPC Unified Architecture sviluppata congiuntamente da OPC e PLCopen. Un server OPC-UA dialoga da una parte via Ethernet con un client di uguale standard connesso al sistema MOM (Manufacturing Operations Management, fruibile anche come cloud PaaS) dal quale riceve i dati di produzione; e dall’altra, via EtherCAT, con la macchina a controllo numerico, che non deve subire alcun adeguamento. A questo punto il server OPC-UA, che ‘vede’ la macchina fisica, ne può realizzare il gemello digitale e il MOM, agendo sul ‘digital twin’ può modificare la configurazione della macchina reale secondo bisogno. Oltre all’OPC-UA, gli altri standard sono semplici protocolli di comunicazione: il diffuso EtherCAT (o un qualsiasi altro protocollo di tipo fieldbus che sia adottato dalla macchina in causa), e l’MQTT (Message Queue Telemetry Transport) su Tcp/Ip che è il protocollo base per il trasporto dati nell’IoT.
Da tutto questo discorso sugli standard emergono alcuni messaggi positivi. E il primo è, come sottolinea Terzi, “…che oggi, 2017, abbiamo a disposizione, grazie all’evoluzione tecnologica e metodologica, standard e riferimenti attraverso i quali poter lavorare”. In altri termini, prosegue Terzi “chiunque voglia domani realizzare nella propria azienda un progetto di Industria 4.0 per collegare e connettere le proprie macchine sappia che non deve inventare nulla. Basta che segua ciò che è già stato studiato ed è stato codificato”.