Alstom è una multinazionale con 26mila dipendenti nel mondo focalizzata sul trasporto, con una produzione che va dai tram, ai vagoni delle metropolitane fino ai treni ad alta velocità. L’attività prevede anche soluzioni chiavi mano soprattutto nei paesi in via di sviluppo dove fornisce l’intero sistema di trasporto, comprese le opere civili necessarie.
In Italia il Gruppo ha 2.700 persone che lavorano nelle 8 sedi distribuite su tutto il territorio nazionale, 4 delle quali sono centri di eccellenza mondiale. Una di queste è il sito produttivo di Savigliano, in Piemonte, specializzato in treni ad alta velocità; qui sono stati prodotti i treni Italo di Ntv. Il nuovo treno regionale Coradia Meridian per Trenitalia e il Pendolino di ultima generazione per l’operatore ferroviario svizzero e per le ferrovie polacche, sono “i primi a beneficiare dell’industria digitale”, spiega Luigi Lugaro, Plm Corporate Project Manager di Alstom Italia, che sintetizza: “In questo impianto entrano i profili di alluminio ed esce il treno certificato e collaudato”. Il sito di Savigliano ha come missione industriale la gestione completa del ciclo del prodotto dalle fasi di ricerca, allo sviluppo e ingegnerizzazione, fino alla validazione, alla certificazione dell’agenzia nazionale della sicurezza, alla consegna sul binario del treno finito.
“La sfida principale per l’alta velocità è sul time to market, per soddisfare l’esigenza dei clienti che richiedono tempi sempre più brevi. Al momento si è arrivati a 12-13 mesi per sviluppare un nuovo prodotto. La commessa sui treni regionali di Trenitalia è stata vinta garantendo la consegna in 12 mesi, ma essendo ormai diventato uno standard, va ulteriormente ridotto per essere competitivi”, afferma Lugaro.
Indice degli argomenti
La realtà virtuale entra in fabbrica
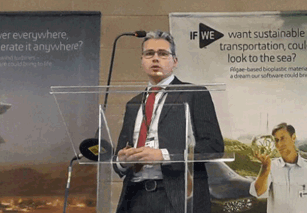
Luigi Lugaro, Plm Corporate Project Manager di Alstom Italia
Fino a 4 anni fa veniva realizzata una pre-serie, costituita da 1 a 4 treni per ottimizzare i processi e utilizzare il ritorno di esperienza dal manufactuting. Ma ormai questo processo è stato cancellato anche grazie all’introduzione della Virtual Room (vedi riquadro) che ha come obiettivo la validazione non solo dei prodotti, ma anche dei processi: gli operai, all’inizio del lancio di una nuova produzione, possono comprendere il prodotto, simulare le situazioni più difficili, catturare il ritorno di esperienza. “In alcune fasi, come la finitura dove è difficile introdurre i robot, utilizzati ad esempio nella lastratura, sono gli operai a dare il valore aggiunto. Grazie alla Virtual Room – spiega Lugaro – è possibile andare in produzione con una situazione più consolidata che ci permette di anticipare le modifiche che in passato avvenivano in fase di produzione, portandole a livello digitale con tempi di reazione inferiori e maggiore flessibilità”.
La sfida della riduzione dei costi è particolarmente importante per i treni regionali dove la competizione si gioca anche con aziende locali e di paesi in via di sviluppo.
“Questa sfida si vince lavorando sui costi indiretti di struttura e sui costi diretti di produzione”, nota Lugaro.
La maggiore competitività si ottiene con la riduzione dei costi di sviluppo prodotto, migliorando l’efficienza dell’esecuzione, adottando una struttura snella con centri di eccellenza e stabilimenti dedicati a certi processi di produzione. Il punto centrale è portare in fase di prototipazione virtuale le problematiche, le simulazioni a livello di carico industriale e di possibili scenari di localizzazione, per avere sui vari centri produttivi un’esecuzione eccellente, con l’obiettivo di progettare, produrre e validare un treno ogni 10 mesi.
Un ambiente collaborativo costruito bottom up
L’adozione del sistema informativo di fabbrica gioca un ruolo essenziale per introdurre miglioramenti capaci di ridurre i costi di esecuzione. “La situazione di partenza vedeva tool diversi non armonizzati e con differenti metodologie per ogni processo, dove l’unico strumento standard per far parlare i diversi sistemi era excel, con il risultato di avere tante attività a basso valore e tanti errori”, ricorda Lugaro. Il progetto lanciato un anno e mezzo fa ha invece portato all’introduzione di una struttura snella, al monitoraggio delle performance, standardizzato i processi, automatizzato gli elementi a basso valore aggiunto. “Sono stati creati processi molto robusti introducendo il concetto di anticipazione sia in termini di sviluppo prodotto e ingegnerizzazione sia di situazioni critiche che si possono verificare in fabbrica”, aggiunge Lugaro.
Le tavole con i disegni tridimensionali arrivano direttamente in officina su monitor, grazie a sistemi Cad arricchiti non solo dalla presentazione tridimensionale, ma da note sui dettagli (ad esempio la saldatura), con la visione completa dell’ordine di produzione che contiene tutto quanto serve; è disponibile anche un sistema di messaging verso l’ufficio di ingegneria per eventuali chiarimenti.
Le soluzioni tecnologiche adottate utilizzano l’integrazione fra l’Erp Sap, gli applicativi Delmia di Dassault Système per la parte di processo e simulazione, Mes di Dassault Apriso per la parte di esecuzione. Il progetto si è sviluppato in una logica bottom up a partire dall’esecuzione e il supporto agli operai per passare poi alla fase più alta di digitalizzazione dell’ingegneria. Questa scelta deriva anche dal fallimento di un precedente progetto e approccio, pensato in logica top down, che partiva dalla digitalizzazione dell’ingegneria per andare sull’industrializzazione e arrivare infine al manufacturing.
I benefici riguardano anche la riduzione dei costi sulla qualità, grazie alla documentazione sempre aggiornata, senza errori e inconsistenze, e il transfer knowledge grazie alla possibilità di inviare la documentazione per la costruzione nei diversi siti. Un esempio è una importante commessa da 6 miliardi di euro in Sud Africa per la costruzione di mille treni che richiedeva un’elevata localizzazione. “L’ottimizzazione del technology transfer ha consentito elevati risparmi nella costruzione di uno stabilimento di assemblaggio molto più snello”, conclude Lugaro.
La Virtual Room Già dotata di strumentazione 3D dedicata alla formazione (come ad esempio una saldatrice virtuale), la sede di Savigliano è la prima fabbrica Alstom al mondo ad avere una sala dedicata alla realtà virtuale utilizzata per la progettazione dei treni e dei loro componenti e la simulazione dei processi produttivi. Nella fase di progettazione preliminare, gli ingegneri hanno a disposizione un modello virtuale del treno sempre più completo, che permette di ampliare lo spettro delle simulazioni possibili, che vanno dalle operazioni di verifica di interferenze, a quelle di montaggio, di ergonomia, di abitabilità e di incarrozzamento. Per poter fare tutto ciò, la Virtual Room è dotata di avanzate attrezzature che consentono l’immersione e l’interattività nell’ambiente virtuale: attraverso telecamere adeguatamente disposte e sensori applicati sugli occhiali 3D utilizzati dagli ingegneri e dagli operatori della produzione, si arriva ad essere virtualmente all’interno del modello del treno; grazie a opportuni sensori applicati sulle mani e sugli arti, l’operatore può simulare il montaggio e lo smontaggio delle varie parti costituenti il treno. La realtà virtuale può essere utilizzata anche per la scelta della configurazione e del design degli interni, tramite il rendering virtuale del veicolo, il progettista e il cliente possono infatti navigare all’interno del treno e scegliere, con grande anticipo rispetto alla realizzazione definitiva, colori, ambienti e soluzioni costruttive. |