Supply chain sotto stress: gli effetti della pandemia sulla resilienza delle filiere sta portando alla luce tutte le vulnerabilità associate a modelli di approvvigionamento che hanno sottostimato i margini di rischio, ordinari e straordinari.
Dal momento che il COVID-19 ha portato al lockdown, la gran parte delle supply chain ha temporaneamente sospeso la produzione mentre i fornitori di servizi logistici non possono più trasportare merci senza problemi, in particolare oltre confine. Anche chi ha saputo diversificare i fornitori in maniera più lungimirante e strategica, sta accusando il contraccolpo.
In questa situazione d’emergenza, è ancora possibile garantire ai clienti i prodotti che desiderano quando li desiderano? È possibile una ripartenza della produzione in sicurezza, pianificando gli scenari di lungo periodo?
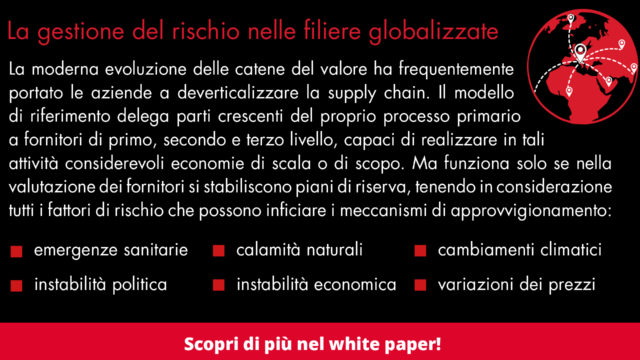
Indice degli argomenti
La gestione del rischio nelle filiere
In uno stato di emergenza, i vincoli alla mobilità e ai trasporti minacciano la disponibilità dei materiali una volta esaurite le attuali scorte. In tutto questo, le politiche di outsourcing che hanno posto la Cina al centro della maggior parte delle catene di approvvigionamento globali, nel medio e nel lungo termine rendono ancora più arduo stimare i tempi di una ripresa alla normalità. Nella transizione tra la Fase 1 e la Fase 2 le aziende manifatturiere che non si sono fermate, stanno comunque lavorando a basso regime a causa delle restrizioni legate a virus che impediscono a tutti i lavoratori di spostarsi verso le fabbriche. Durante la normale produzione la visibilità sulla catena di approvvigionamento è la chiave dell’efficienza e dell’agilità. Ma quando si verificano interruzioni critiche delle forniture, la visibilità diventa quanto mai cruciale per comprendere l’impatto dell’interruzione sul resto della catena in modo che l’ecosistema possa pianificare e agire, sviluppando percorsi verso nuovi fornitori alternativi.
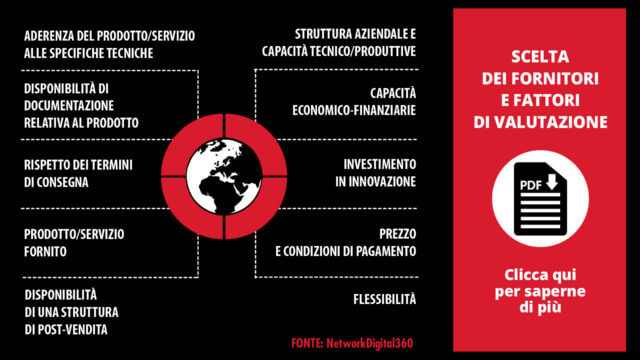
Supply chain tutte da ridisegnare
Dimentichiamoci i modelli di produzione e di sviluppo che abbiamo conosciuto fino ad oggi. Dimentichiamoci delle filiere logistico-produttive che, grazie alla globalizzazione, ricercavano nuove economie di scala finalizzate a ridurre i costi del lavoro e dei materiali, portando efficienza nei processi primari, affidandosi a modelli di global sourcing. Dimentichiamoci anche di alcune pratiche lean che, celebrando la razionalizzazione e l’ottimizzazione, hanno spinto le aziende a ridurre progressivamente le scorte di materie prime, componenti e prodotti finiti lungo la supply chain. Per fronteggiare la crisi della produzione e dei trasporti ma anche per potenziare la salute e la sicurezza dei lavoratori, le supply chain verranno tutte ridisegnate. Una delle chiave di volta sarà diversificare in modo più agile e resiliente i fornitori.
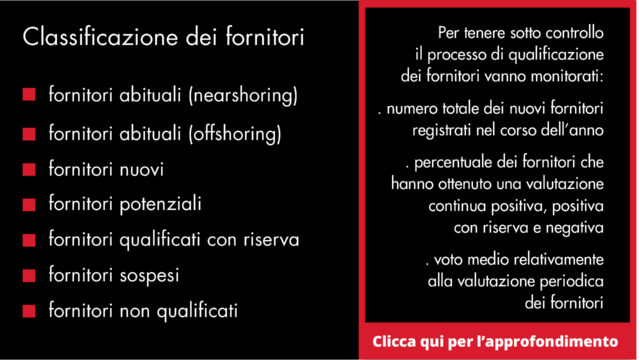
Nuove economie di scala: dall’offshoring al nearshoring
Per garantire maggiore rapidità, e soprattutto visibilità e controllo, diventeranno meno globali e più locali. Già da tempo al fenomeno dell’offshoring delle fabbriche verso il Lontano Oriente aveva fatto seguito il reshoring o quanto meno il near-shoring verso fornitori più vicini e maggiormente allineati ai fusi orari e alle regolamentazioni di produzione e consegna nazionali. Tutti questi due fenomeni subiranno una nuova accelerazione. L’obiettivo primario? Ridurre la complessità della catena di approvvigionamento.
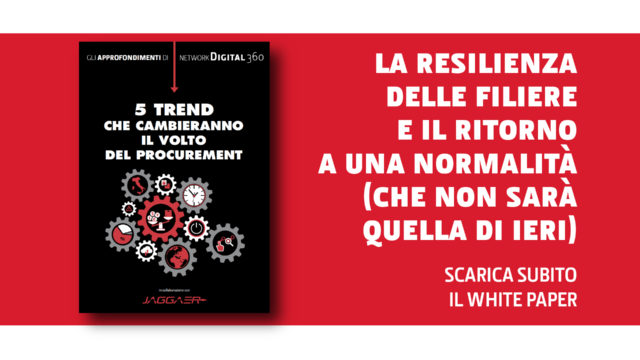
Digitalizzazione della supply chain
Al di là delle contromisure sanitarie, la premessa indispensabile sarà digitalizzare tutti i processi di approvvigionamento. Eliminando la necessità di usare la carta e la firma manuale a supporto della gestione di ordini, bolle di consegna e fatture, le informazioni messe a sistema consentiranno di velocizzare le procedure e di introdurre meccanismi di controllo, valutazione ed analisi sempre più avanzati a supporto dei processi decisionali. Integrazione e interoperabilità saranno abilitate da un crescente ricorso alle tecnologie che potenzieranno lo smartworking ma anche il controllo a distanza di mezzi di produzione, remotizzando anche molte attività di supervisione dei processi industriali, di manutenzione e perfino di installazione di impianti e macchinari complessi, tramite ad esempio l’impiego di mixed reality.
Le tecnologie che aiutano a fare la differenza nelle filiere
Supply chain management oggi più che mai significa ampliare la prospettiva: al raggiungimento degli obiettivi aziendali di breve (budget) e medio (piano) periodo, che pure sono fondamentali, si affianca la questione essenziale della sostenibilità del modello di business di fronte ai cambiamenti che si verificano incessantemente con modi e tempistiche non predicibili.
In questo contesto l’eProcurement automatizza e formalizza la gestione dei contratti di fornitura, integrando un sistema di monitoraggio del rischio in un unico ambiente online. Oltre a ridurre i rischi operativi, la tecnologia permette alle aziende di monitorare sistematicamente una pluralità di istanze come obblighi contrattuali, esposizioni, scadenze, modifiche rinnovi, recessioni e via dicendo. In questo modo si aumenta la visibilità sull’intero ciclo di vita del contratto, riducendo il rischio di operare senza le corrette coperture contrattuali.
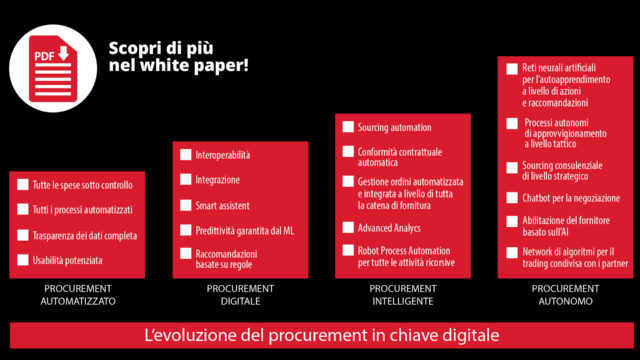
I vantaggi della digital transformation
Tra i plus delle soluzioni automatizzate, infatti, c’è la qualità di una reportistica dettagliata ma anche la possibilità di avvalersi di sistemi di valutazione e segnalazione supportati dall’Intelligenza Artificiale e dal Machine Learning. Grazie all’uso di algoritmi evoluti, l’ufficio acquisti può avvalersi di criteri di valutazione multipli di tipo descrittivo, diagnostico, predittivo e prescrittivo, con una visualizzazione dei dati sempre chiara e immediata, per uno spend management allo stato dell’arte. Inoltre, grazie a un sistema centralizzato, l’archiviazione documentale è protetta e sicura, offrendo massima flessibilità nel recupero di tutte le informazioni.
In questo modo è possibile gestire con efficienza le revisioni contruattuali e monitorare i vari flussi approvativi. È così che l’ufficio acquisti aumenta la visibilità e il controllo sulla filiera, identificando immediatamente canali alternativi al subentrare di una crisi legata a default finanziario, avarie tecniche degli impianti produttivi, problematiche geopolitiche, modifica di leggi e/o regolamenti, calamità naturali, emergenze sanitarie e così via. Facendo la differenza nel presente e nel futuro.
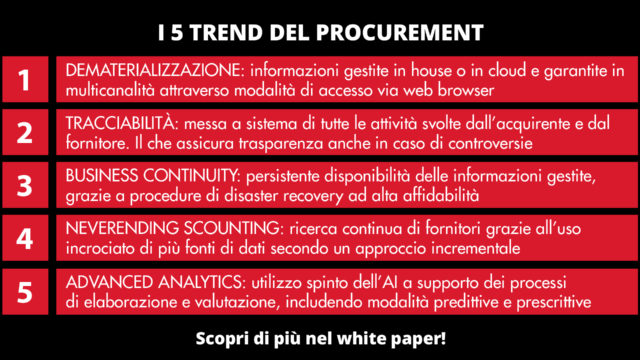
Digitalizzazione delle filiere: 3 casi di studio
Semplificare i processi di approvvigionamento impone alle aziende un processo di autoanalisi. Gli esperti citano tre storie di successo emblematiche
#1 Blount Fine Foods coniuga automazione e integrazione
Blount Fine Foods è un’azienda americana fondata nel 1880 con sede a Fall River, Massachusetts, che produce zuppe e salse. Il brand ha reimplementato il proprio ERP di riferimento per ridurre la complessità della catena di approvvigionamento.
“Tra i nostri clienti abbiamo anche catene di negozi di alimentari, distributori di servizi di ristorazione e altri venditori che vendono zuppa ai consumatori – ha spiegato Mike Backus, direttore dei sistemi informativi aziendali di Blount -. Le zuppe sono vendute negli Stati Uniti con i marchi Blount, Legal Sea Foods e Panera Bread. Al momento stiamo trasformando i nostri sistemi informativi, lavorando alla reimplementazione del nostro ERP per sfruttare le nuove modalità di gestione della supply chain abilitate dall’evoluzione della piattaforma, integrando tutte le funzionalità logistiche per ridurre la complessità della catena di approvvigionamento”.
Blount aveva implementato la prima versione del suo gestionale nel 2005. Si trattava di un sistema appositamente progettato per i produttori di processi. Prima che il team tecnologico di Blount iniziasse il progetto di reingegnerizzazione, la società aveva più di 100 database Access tutti intercollegati tra loro e integrati all’ERP. Con la migrazione l’azienda voleva sfruttare il modulo di pianificazione dei requisiti dei materiali utilizzando l’automazione per gestire meglio gli articoli da produrre, le materie prime acquistare e le spedizioni, riducendo quanto più possibile il lavoro manuale.
“Volevamo ridurre gli sprechi – ha sottolineato Backus -, ottenere le giuste quantità di ordini, lo stock minimo adeguato gestendo al meglio le situazioni in cui non siamo in grado di spedire gli ordini dei clienti per intero come, ad esempio, non abbiamo abbastanza prodotti. Da un lato stiamo cercando di personalizzare la relazione con i clienti raccogliendo maggiori informazioni sulle loro esigenze e i loro desiderata. Dall’altro, puntiamo a rendere la nostra attività più efficiente”.
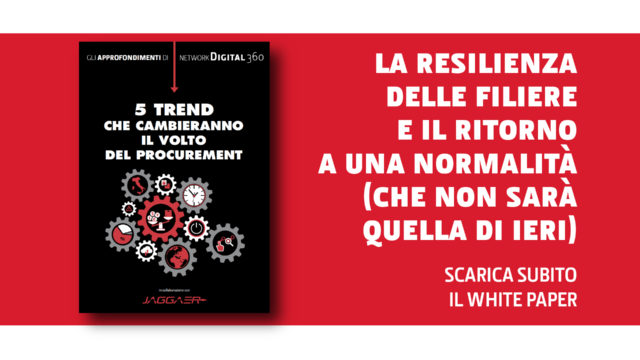
#2 The Wenger Group sceglie la digital transformation
The Wenger Group è un’azienda familiare con sede a Rheems, in Pennsylvania, che da 75 anni opera nell’industria di pollame, suini e latticini. La società gestisce otto sedi di macinazione di mangime in Pennsylvania e una nel Maryland, fornendo anche la vendita di uova e uova, servizi di allevamento e pollastre nella regione del Medio Atlantico.
“Per semplificare la nostra catena di approvvigionamento utilizziamo un sistema di Enterprise Content Management (ECM) – ha spiegato Michelle Lombardo Smith, business analyst di The Wenger Group -. Abbiamo intenzione di espandere il nostro portafoglio in modo da poter essere più resistenti alle catastrofi ed essere più agili e resilienti. Già nel 2015 eravamo intervenuti per digitalizzare le nostre procedure. La gestione cartacea, infatti, non ci consentiva di acquisire i dati delle operazioni in modo costante e tempestivo anche perché le registrazioni prodotte dai nel corso dei processi di produzione venivano archiviate in varie posizioni fisiche, limitando l’accesso ai documenti. Abbiamo implementato un sistema di gestione dei contenuti aziendali con un componente del flusso di lavoro che va a semplificare la supply chain, automatizzando alcuni processi e mettendo a sistema tutte le informazioni”.
I vantaggi dell’automazione sono diversi, a partire dall’audit trail, dal monitoraggio, dalle approvazioni automatizzate, dalla generazione di report e da una qualità dei dati raccolti impensabile attraverso una gestione cartacea.
La documentazione, infatti, include le schede di dati di sicurezza che forniscono l’elenco delle sostanze chimiche impiegare nei mulini del Gruppo e gli ingredienti utilizzati nei mangimi. Queste informazioni oggi sono tutte tracciate e rintracciate, archiviate elettronicamente, rendendo così i dati sempre immediatamente accessibili e puntuali all’insegna della massima trasparenza ed efficienza.
“Ora siamo in grado di identificare i prodotti chimici in base alla loro locazione – ha aggiunto Lombardo Smith -, nonché i diversi livelli di ingredienti, in modo da poter facilmente identificare dove potrebbe essere qualcosa se avessimo bisogno di fare un richiamo su un particolare articolo. La digitalizzazione dei processi oggi risolve anche il tema della scansione e l’elaborazione dei ticket di consegna: siamo riusciti a ridurre i tempi di elaborazione della fattura da sei a tre ore, riducendo sensibilmente tutti gli errori di fatturazione. Il nostro prossimo obiettivo è di spostare il nostro ERP su cloud”.
#3 Posh rende agile la sua catena di fornitura
Perfectly Posh, con sede a Salt Lake City, è una società che si occupa di cura della pelle e da 8 anni a questa parte distribuisce i suoi prodotti attraverso un sistema di porta a porta attraverso una nutrita community che organizza anche feste in casa o eventi online. Il brand partecipa anche a eventi dei fornitori, organizza raccolte fondi ma vende anche online attraverso formule BtB e BtC tutti i suoi prodotti, tra cui saponi, creme per mani e viso, lavaggio del viso e scrub per il corpo.
“I nostro modello di business è consentire alle persone di acquistare i nostri prodotti o di venderli come preferiscono – ha raccontato Jonee Woodard, COO di Perfectly Posh -. I clienti possono acquistare direttamente, acquistare all’ingrosso per rivendere od operare come terzisti di società di e-commerce. Il che significa che la nostra supply chain deve essere estremamente agile sia in termini di forniture che di consegne, con un’elaborazione degli ordini in tempo reale”.
Alcuni ordini della società sono ordini al dettaglio molto grandi, nell’ordine delle migliaia di dollari, mentre altri sono solo ordini a unità singola. In entrambi i casi, l’azienda deve procedere a elaborarli in modo efficace ed efficiente.
“Abbiamo scelto una piattaforma che, da un punto di vista plug-and-play, ci permette di collegare back end e front end in modo estremamente funzionale, integrando il gestionale con il nostro fornitore logistico ma anche con il nostro sito Web di e-commerce Salesforce e con il nostro sistema di gestione degli ordini. Il tutto integrato a uno strumento di analisi. In questo modo abbiamo risolto il circolo virtuoso dell’informazione: trasmettiamo gli ordini, il provider logistico ci invia tutti i dettagli della transazione che poi, a nostra volta, condividiamo con i nostri clienti. In tutto questo è essenziale che tutte le applicazioni siano perfettamente sincronizzate e funzionino in tempo reale perché non c’è tempo di caricare o scaricare ordini o di capire la disponibilità a livello di inventario”.
L’ultimo consiglio alle aziende che puntano a rendere agile la propria supply chain? Non guardate tanto a ciò che vi serve nell’immediato. Focalizzatevi su un sistema che vi garantisca massima scalabilità rispetto alle vostre esigenze nel medio e nel lungo termine.